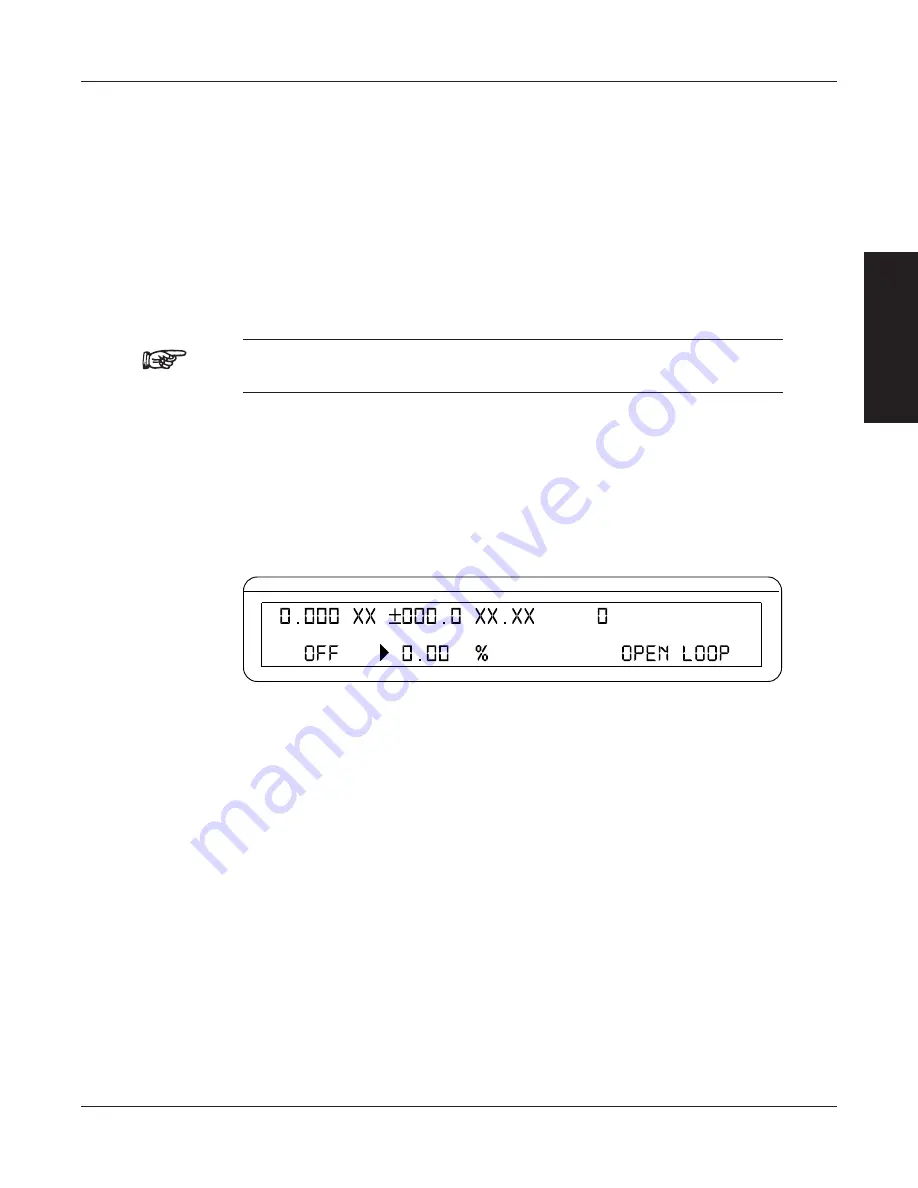
43
Magtrol Model DSP6001 Dynamometer Controller
Chapter 5 – PID Settings
SETUP
5.4.1.3
Setting Additional Scale Factor for D (Derivative)
1. Starting from the main menu, press and hold the D button. While holding the D button,
press SHIFT.
2. Use the D button to toggle through the letters in the unit (A, B, C, D, E, F, G, H and I).
3. Choose the letter that corresponds with the pre-determined setting provided in the Additional
Scale Factor Table shown in
Appendix F
.
4. Once the letter is chosen, press SHIFT to return to the main menu.
5.5
SETTING THE CORRECT PID’S FOR YOUR MOTOR
Note:
Each type of motor will have it’s own optimum PID setting at
different load points.
5.5.1
S
etting
tHe
piD
witH
an
U
nknown
M
otor
or
S
ySteM
If the user is unfamiliar with the characteristics of the motor under test, it is recommended to
begin in Open Loop Control mode. In doing so, the user can safely get an idea of the motor’s
performance.
1. To enter Open Loop Control mode, begin with the motor and brake OFF. Press and hold the
TORQUE SET button until a second beep is heard. The display will appear as follows:
POWER
BRAKE STATUS
SET POINT
SET POINT
P
I
D
TORQUE
SPEED
STATUS
Figure 5–2 Open Loop Control Menu
2. Set the percent excitation to zero.
3. Start the motor.
4. Slowly increase the excitation current to the brake.
5. Make a note of the torque and speed values of which the motor is capable.
6. To exit the Open Loop Control mode and return to the main menu, turn the motor and brake
OFF and press and hold the TORQUE SET button until a second beep is heard.
5.5.2
S
etting
tHe
piD
for
t
orqUe
C
ontroL
1. With the motor and brake OFF, set the desired Torque Set Point by pressing the TORQUE
SET button and using the UP
and DOWN
buttons and Decrease/Increase dial.
2. Set the P, I and D values to zero.
3. Turn the motor ON.
4. Turn the brake ON.
5. Slowly increase the P term until the torque read is about 25% of the desired load point.