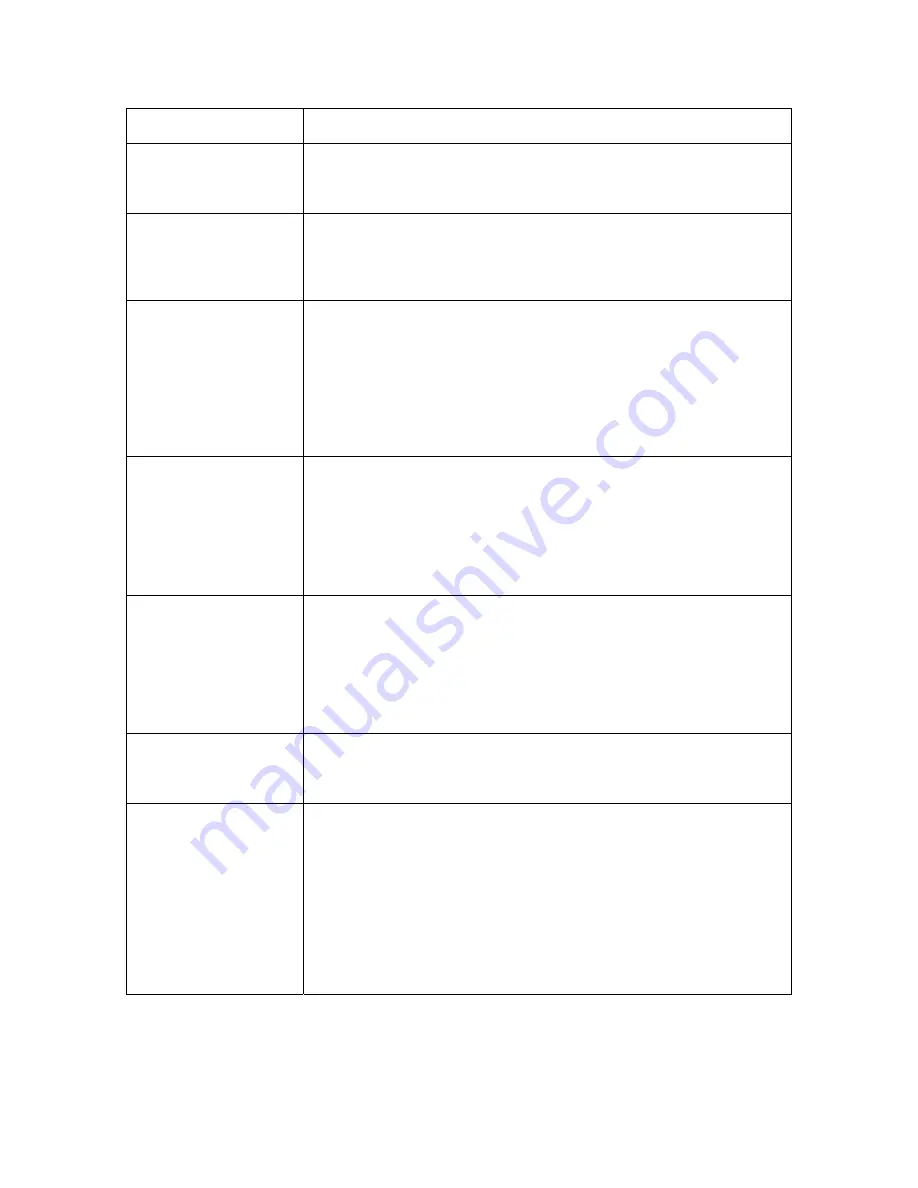
DRIVE FAULTS
91
ERROR/FAULT CODE
PROBABLE CAUSE/ — CORRECTIVE ACTION
414 SOFTWARE
COMPATABILITY
FAULT
--- Indicates that the PCU
(U13,U14) Version and or Revision won’t operate with the DCU
(U39,U40) installed in the drive.
1. Contact Magnetek
13-17, 21-26, 100-104,
112-114, 220-234,
240-254, 926
MISC FAULTS
- Problem with either hardware or software on the
Drive Control PCB. See list at Section 4.5.
Check and/or replace U13, U14, U39, U40 (EPROM’s).
Replace Drive Control PCB A1.
117 / 118
SERIAL COMMUNICATION FAULT
117 = Serial comm. not started within 20 seconds after drive reset or
power up.
118 = Valid serial comm. message not received for more than 150 MS.
1. Ensure that host is connected and sending valid messages.
2. Look for and correct electrical grounding noise interference
problem.
3. If Serial comm. is not being used do not set #110 to selection 3.
97 OVERSPEED
FAULT
- The motor speed has exceeded the trip level
set in function #12, as measured by the encoder. #12 is a percentage
of the motor speed value set in #11. Possible cause
Incorrect setting of #10, #11 or #12.
Poor speed regulator tuning - Check #40, 41 & 42
Velocity reference set above rated speed.
Intermittent velocity encoder.
98
TACH LOSS FAULT
- The drive does not see the encoder velocity in
proportion to armature voltage indication of speed. Refer to Function
explanations for #14 and #15.
Ensure that the encoder is working. Look for loose connections.
Raise the value for #14 if motor has high resistance.
Ensure that the contactor feedback circuit at A1TB1-7 does not close
before the armature power poles. See timing diagram Fig. 4.4.7.
99
REVERSED TACH FAULT
— The digital encoder and motor voltage
signals do not agree in direction of rotation. Probable cause: Encoder
leads are reversed. Reverse connections for A and A/NOT.
900
PCU LOOP FAULT
- The contactor did not close or opened
unexpectedly. Or the motor voltage exceeded 30% of rated motor
voltage #7 during Self-Tune #997. When this occurs, the Severe Fault
flag is set and the DSD 412 current reference is forced to zero
.
This
fault will shutdown the drive.
Check the contactor aux feedback circuit to TB1-7.
Check contactor and LPR coils for proper operation.
Check that power is being applied to LPR from the power supply at
TB3- 5. (Will be momentary until F900 occurs.) If not there, suspect
an internal relay failure. Replace A4, Power Supply PCB.
Summary of Contents for DSD 412
Page 1: ...DSD 412 DC Elevator Drive Technical Manual CS00407 rev 06...
Page 6: ...6...
Page 102: ...MAINTENANCE 102 Figure 24 Connector and E prom Locations...
Page 103: ...MAINTENANCE 103 Figure 25 Test Point Locations...
Page 115: ...OUTLINE DRAWING 100A 115 Figure 26 Drive Chassis Outline DSD 412 100 Amp...
Page 116: ...OUTLINE DRAWING 190A 116 Figure 27 Drive Chassis Outline DSD 412 195 Amp...
Page 117: ...OUTLINE DRAWING 300A 117 Figure 28 Drive Chasis Outline DSD 412 300 Amp...
Page 118: ...LAYOUT DRAWING 100A 118 Figure 29 Layout DSD 412 100 Amp A3 A1 A2 A2 L1 NEG GND L2 L3 POS...
Page 119: ...LAYOUT DRAWING 195A 119 Figure 30 Layout DSD 412 195 Amp A3 A1 A2 A2...
Page 120: ...LAYOUT DRAWING 300A 120 Figure 31 Layout DSD 412 300 Amp A3 A1 A2 A2...
Page 121: ......