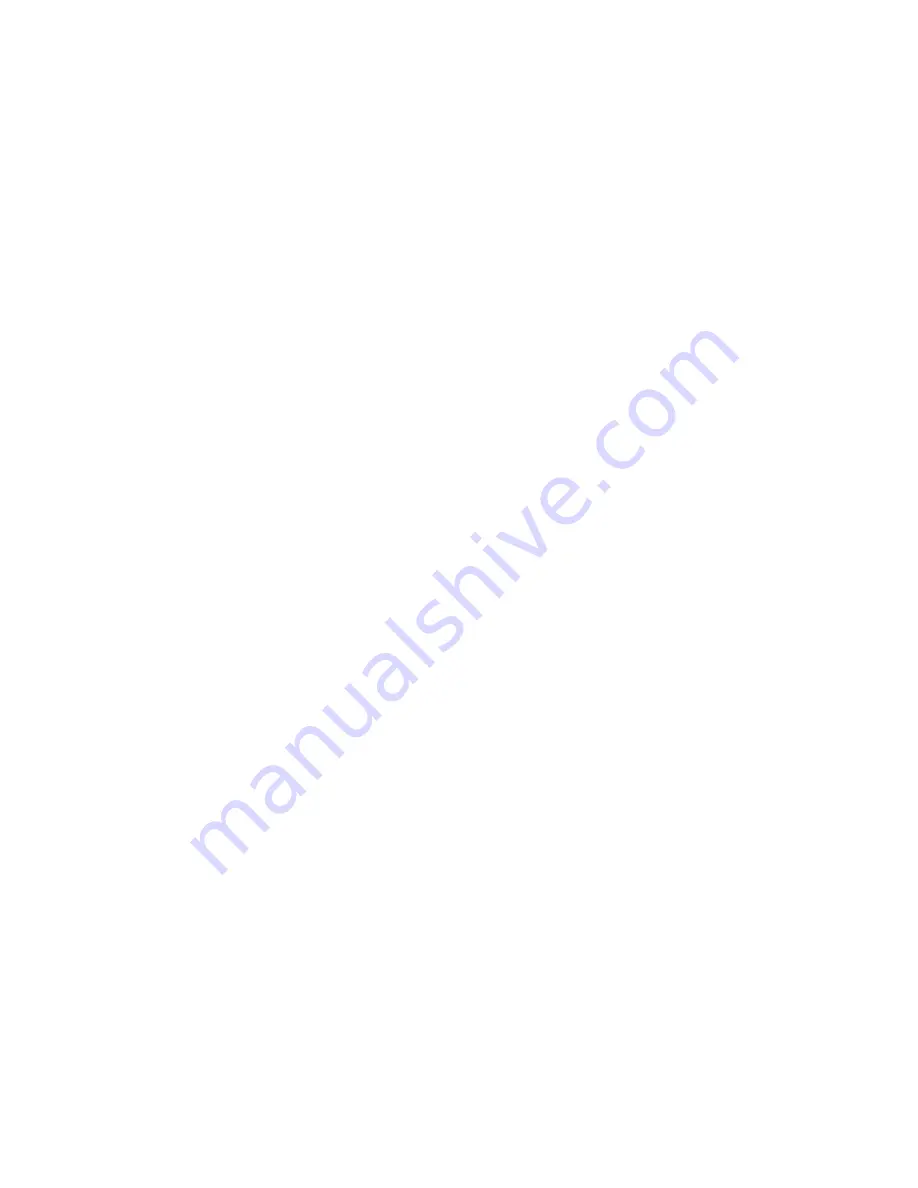
DRIVE SETUP AND ADJUSTMENT
56
pre-set speed selects are used, set this value
to 0, off. If a gain switch will be from the serial
link, set this value to 1, ON. [function 104 on
and function 110 set for analog or pre-set
speeds results in no gain switching.]
Function # 105
Gain Switch Speed
Units: PU
Range: 0.00 – 1.10
Default: 1.10
This function is only used if function 104 is off.
The value determines the speed where
velocity regulator gain is switched. If the
speed reference is below the value of function
105, the closed loop gain will correspond to
that set by function 40. If the speed reference
value is above set point function 105, then
closed loop bandwidth will be as set in
function 39.
Function # 107
Tach Rate Gain
Units: %
Range: 0.00 - 30.00
Default: 0.00
This value adjusts the gain of differential
encoder/tach rate feedback. It can be useful
to help attenuate vibration and rope
resonance effects. Disable this function by
setting the value to zero. If using this feature,
keep the setting as low as possible consistent
with good operation.
Function #110
Reference Mode Select
Units: Logic
Range: 1 - 4
Default: 2
This function allows the user to select the
source of the velocity reference signal.
Setting this value to 1
enables the drive to
follow the magnitude and direction polarity of
an external analog reference, and external
ramp/slew limit rates function 21.
Setting this value to 2
(default) enables the 1
of 7 internal pre-set speed selects via
function 151 through 157 (preset speeds) and
function 170 through 181 (accel/decel, jerk
rates). See also function 115 for direction
control and function 150 for speed selects.
Setting this value to 3
enables serial link
control of the velocity reference, and external
ramp/slew limits rates of function 21.
Setting this value to 4
enables a uni-polar
analog reference to be used with external
direction logic commands. External
ramp/slew limit rates of #21 will also be used.
Function #111
Arched Travel Disable (Jerk Abort)
Units: Logic
Range: 0 (Off) – 1 (On)
Default: 1 (On)
Previously named Jerk Abort Enable. When
ON, changing the speed reference to a value
less than or equal the actual speed will cause
the S-Curve reference generator to
immediately stop acceleration, and begin to
decel if appropriate. When OFF, changing the
reference to a lower speed will cause a jerk-
out (of any existing accel) and jerk-in to a
decel sequence. If done while accelerating,
Arched Travel will be the result.
Function #112
Encoder Feedback Enable
Units: NUM
Range: 0 (Off) – 1 (On)
Default: 1 (On)
Setting this value to 0, off, enables the
Armature Voltage Feedback Mode to operate.
This parameter must be set to 1 for normal
operation of the drive. When in this mode the
encoder feedback monitor function 601 will
still be active to allow for troubleshooting,
however this signal will not affect speed
regulation. This mode is intended for
maintainance and troubleshooting only.
Function #113
Armature Voltage @ Max Speed
Units: VDC
Range: 0 - 650
Default: 100
This parameter will control the speed which
the motor will reach when operating in the
Armature Voltage Feedback Maintainance
Mode. The theory would be that the motor will
operate up to this level of VDC if given a
100% speed command. The speed can be
increased or decreased by either raising
(Increase Speed) or lowering (Decrease
Speed) this number or reducing (Increase
Speed) or increasing (Decrease Speed)
function 50 'Rated Field Current'.
Summary of Contents for DSD 412
Page 1: ...DSD 412 DC Elevator Drive Technical Manual CS00407 rev 06...
Page 6: ...6...
Page 102: ...MAINTENANCE 102 Figure 24 Connector and E prom Locations...
Page 103: ...MAINTENANCE 103 Figure 25 Test Point Locations...
Page 115: ...OUTLINE DRAWING 100A 115 Figure 26 Drive Chassis Outline DSD 412 100 Amp...
Page 116: ...OUTLINE DRAWING 190A 116 Figure 27 Drive Chassis Outline DSD 412 195 Amp...
Page 117: ...OUTLINE DRAWING 300A 117 Figure 28 Drive Chasis Outline DSD 412 300 Amp...
Page 118: ...LAYOUT DRAWING 100A 118 Figure 29 Layout DSD 412 100 Amp A3 A1 A2 A2 L1 NEG GND L2 L3 POS...
Page 119: ...LAYOUT DRAWING 195A 119 Figure 30 Layout DSD 412 195 Amp A3 A1 A2 A2...
Page 120: ...LAYOUT DRAWING 300A 120 Figure 31 Layout DSD 412 300 Amp A3 A1 A2 A2...
Page 121: ......