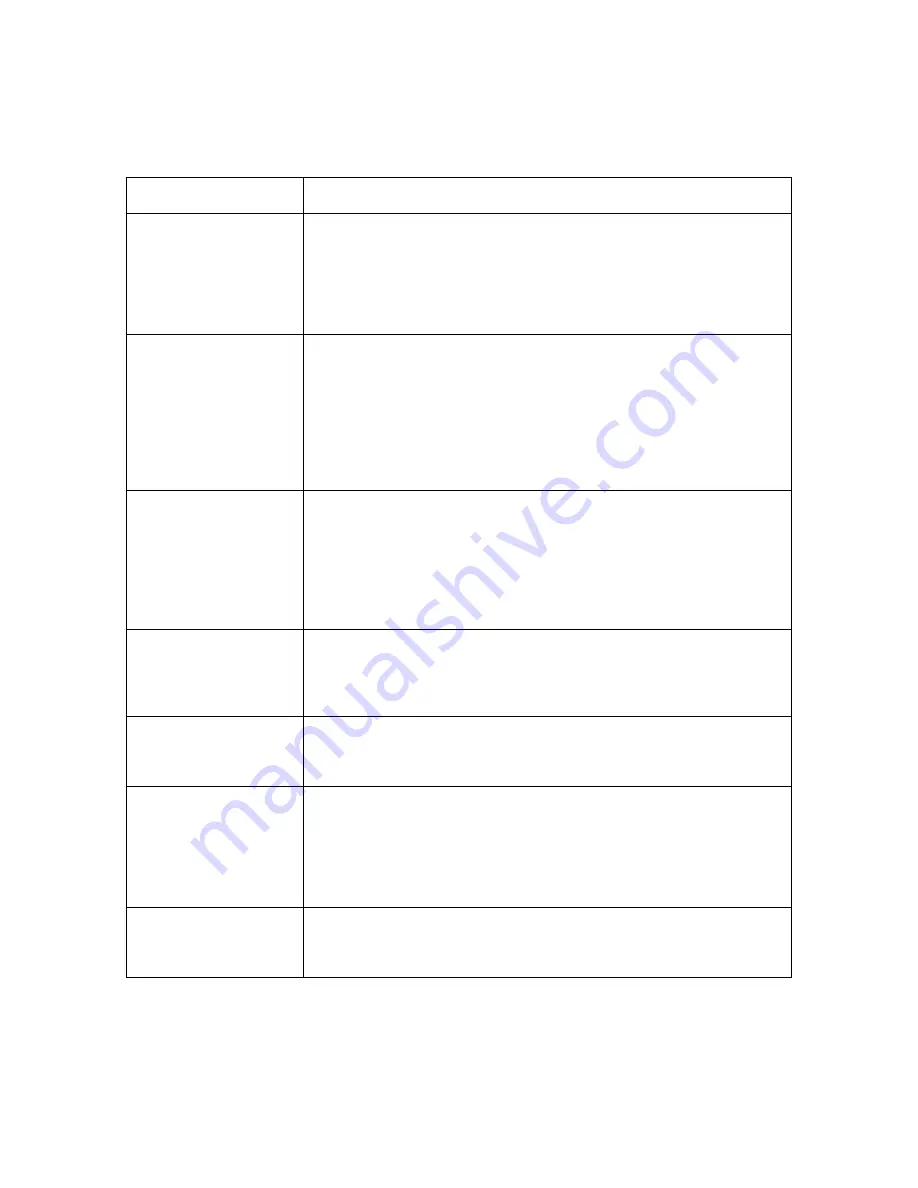
DRIVE FAULTS
89
Troubleshooting
ERROR/FAULT CODE
PROBABLE CAUSE/ — CORRECTIVE ACTION
400
MOTOR OVERLOAD FAULT ---
Indicates that the drive has delivered
excess motor amps for a significant period of time. Refer to #83 and
#84 for proper set-up. Check for dragging elevator brake or weakened
motor field. A motor overload fault does not automatically shut down
the drive, but is annunciated via the ALARM relay output K2. See
#182
401 EXCESSIVE
FIELD CURRENT ---
Indicates that measured motor field
current exceeded 125% of rated current #50. – Causes:
Partially shorted motor field coil. Check motor field.
Wrong data entry causing unstable motor field current regulator.
Review and verify settings for #49, 50, 51, 52, 54, & 55.
Mis-wiring of module A3. Verify that phasing is correct.
Wrong current tap at A3, TB4, or A3 SW1 setting. Verify.
Malfunction of motor field power circuit. Check module A3.
402
LOOP CONTACTOR FAULT
— The Loop Contactor auxiliary contact
does not pick up or drop out within the designated time as requested
by the DSD 412 drive. See #102. – Causes:
Defective Loop Contactor Aux. Check for proper feedback at TB1-7.
Defective Contactor. Check for open coil or mechanical binding.
Defective Pilot Relay LPR.
Interference from other elevator relay contact circuits.
403
FIVE-MINUTE FULL FIELD –
Indicates that the Drive and Field
Enable control circuit at TB1-9 was active for 5 minutes without starting
the drive. This can cause motor field burnout. Check car controller
relay logic.
404
OPEN ARMATURE CIRCUIT –
A large current error existed for ½
second. Check the DC link fuse F4. Check motor armature circuit
wiring. Check power poles in the DC loop contactor.
405
SAFETY CIRCUIT FAULT
— The Safety Circuit is not closed. The
Drive has detected that the Safety Circuit wired between TB3-1 and
TB3-6 on the Power Supply A4 was not closed for 100 MS before a
“Drive Run” command was given, or that it opened unexpectedly while
the loop contactor was closed. Check for intermittent connections in
the Safety Chain.
406
LOW LINE ALARM –
Indicates that the input AC line voltage sagged
more than 10% below nominal line volts as set at #9. This does not
shut down the drive but may be an indication that work is needed to
avoid future Low Line shut down faults, F904.
Summary of Contents for DSD 412
Page 1: ...DSD 412 DC Elevator Drive Technical Manual CS00407 rev 06...
Page 6: ...6...
Page 102: ...MAINTENANCE 102 Figure 24 Connector and E prom Locations...
Page 103: ...MAINTENANCE 103 Figure 25 Test Point Locations...
Page 115: ...OUTLINE DRAWING 100A 115 Figure 26 Drive Chassis Outline DSD 412 100 Amp...
Page 116: ...OUTLINE DRAWING 190A 116 Figure 27 Drive Chassis Outline DSD 412 195 Amp...
Page 117: ...OUTLINE DRAWING 300A 117 Figure 28 Drive Chasis Outline DSD 412 300 Amp...
Page 118: ...LAYOUT DRAWING 100A 118 Figure 29 Layout DSD 412 100 Amp A3 A1 A2 A2 L1 NEG GND L2 L3 POS...
Page 119: ...LAYOUT DRAWING 195A 119 Figure 30 Layout DSD 412 195 Amp A3 A1 A2 A2...
Page 120: ...LAYOUT DRAWING 300A 120 Figure 31 Layout DSD 412 300 Amp A3 A1 A2 A2...
Page 121: ......