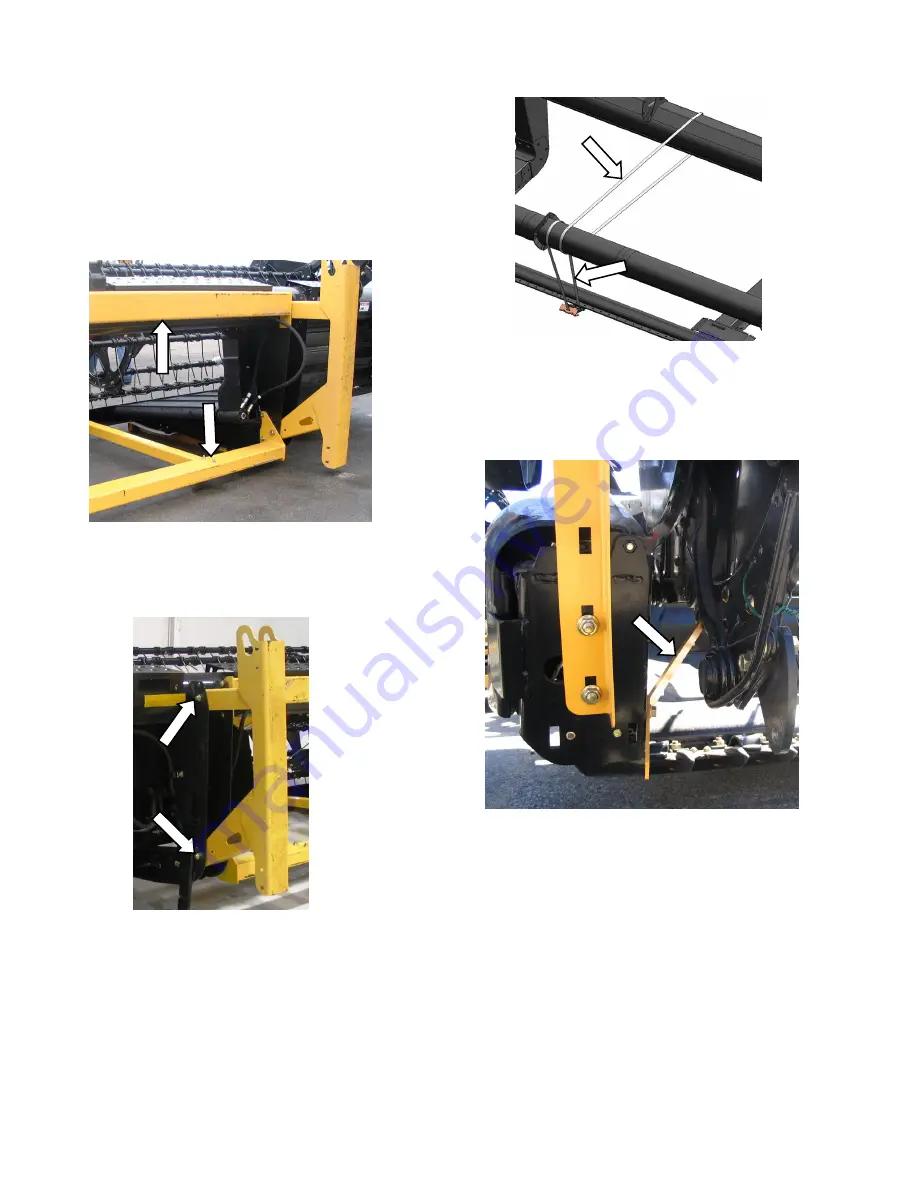
UNLOADING AND ASSEMBLY
Form # 169007
Model Year - 2009
10
STEP 3. REMOVE SHIPPING
SUPPORTS
The removable supports are painted yellow.
NOTE
Unless otherwise specified, discard
supports, and all shipping material and
hardware.
a. Remove six bolts securing lower support to
header legs and remove support.
b. Remove four bolts securing upper support to
header legs and remove support.
c. Remove the two shipping stands from each
header leg.
d. Cut banding securing reel to cutterbar and
backtube.
NOTE
Double reel headers may have banding
on each reel.
e. Remove reel anti-rotation brace between reel
and endsheet.