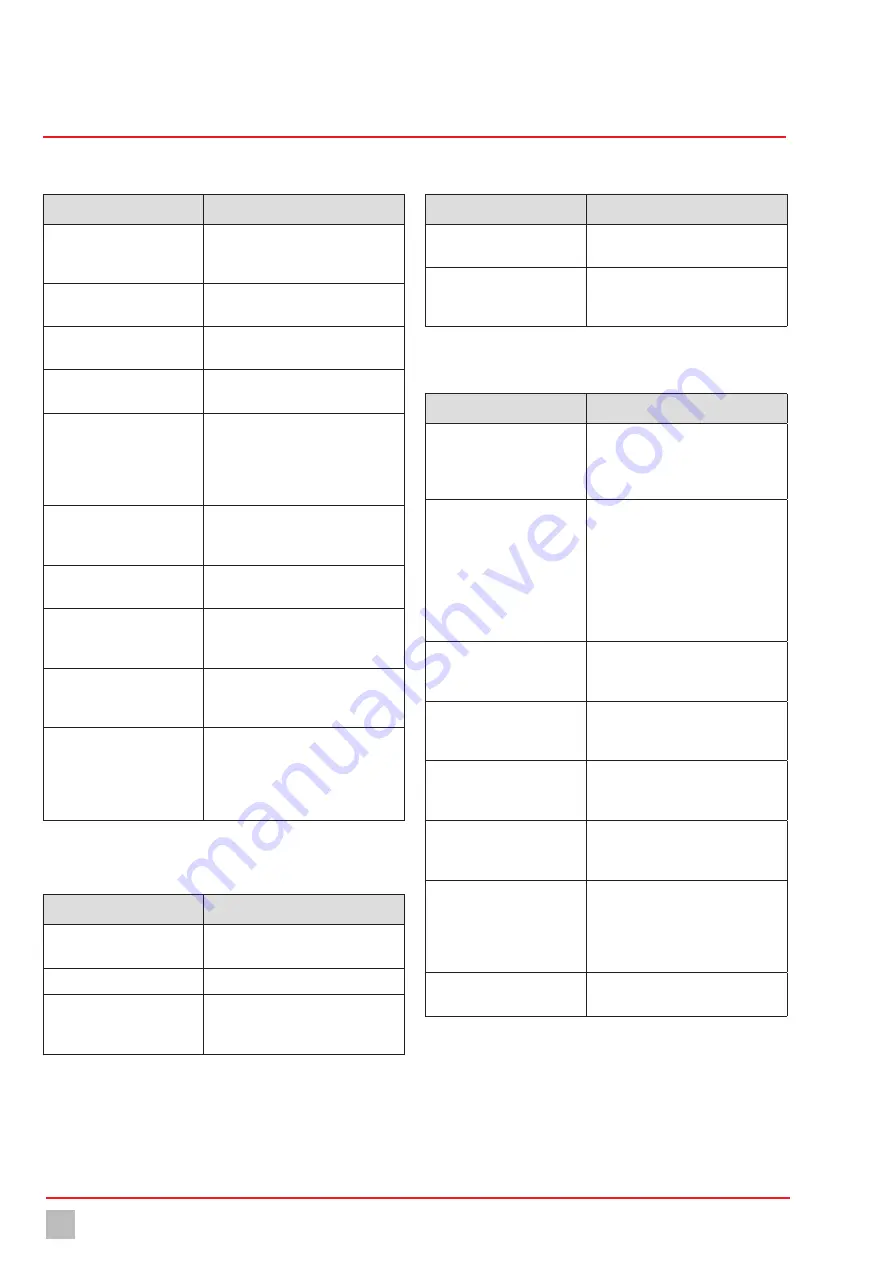
38
© Lutz-Jesco GmbH 2020
BA-10491-02-V01
Piston diaphragm dosing pump
MEMDOS KMS LB/LA
Operating instructions
13.1.3 Delivery rate varies
Possible cause
Remedy
Valve leaking or blocked
è
Clean the valve and vent the
dosing pump.
è
Tighten the screw connections.
Valve damaged (e.g. valve
balls)
è
Remove the damaged parts or
install a new valve.
Suction line is leaking
è
Seal the leak locations or replace
the parts.
Suction line is blocked (e.g.
screen in foot valve)
è
Clean the suction line.
Viscosity too high
è
Possibly reduce the concentration
of the dosing medium or increase
the temperature.
è
Install spring-loaded valves.
è
Increase the pipe diameter.
The drive motor's electrical
data does not match that of
the mains supply
è
Check the electrical installation.
Suction side pressure too high
(pump siphoning)
è
Install a back-pressure valve in
the pressure line.
Pressure peaks due to
acceleration with long suction
lines
è
Install a suction pressure
regulator.
Imprecise dosing due to
changeable positive and
negative suction heads.
è
Install a suction pressure
regulator.
System backpressure too
high (measured at discharge
connection of dosing pump)
è
Clean blocked injection nozzle.
è
Install pulsation dampeners to
reduce pressure peaks if pipes
are too long.
è
Check the safety valves.
Tab. 32: Type of fault: Delivery rate varies
13.1.4 No stroke movement observed
Possible cause
Remedy
Dosing pump set to zero
stroke.
è
Set the stroke length adjusting
knob correctly.
Current supply interrupted
è
Reconnect the current supply
The drive motor's electrical
data does not match that of
the mains supply
è
Check the electrical installation.
Tab. 33: Type of fault: No stroke movement observed
13.1.5 Dosing pump delivery rate too high
Possible cause
Remedy
Suction side pressure too high
(pump siphoning)
è
Install a back-pressure valve in
the pressure line.
Pressure peaks due to
acceleration with long suction
lines
è
Install a suction pressure
regulator.
Tab. 34: Type of fault: Dosing pump delivery rate too high
13.1.6 Diaphragm is torn or tears too often
Possible cause
Remedy
Too little or no back pressure
è
The back pressure must be
increased so that the hose
diaphragm is able to return to its
original position.
Hose diaphragm fitted
incorrectly.
è
The hose diaphragm must be
installed in the pump in such a
way that the high shoulder is
directly adjacent to the opening of
the dosing head. This position can
be read off from a material code
letter on the upper side of the
hose diaphragm.
Shut-off valves closed
è
Open the shut-off valves. Inspect
the dosing pump for possible
damage.
Pressure peaks due to
acceleration with long suction
lines
è
Install a suction pressure
regulator.
The materials are not suitable
for the dosing medium being
used
è
Check the resistance of the
materials.
Diaphragm not screwed up to
the end stop on the dia-
phragm rod
è
Screw a new diaphragm up to the
end stop.
System backpressure too
high (measured at discharge
connection of dosing pump)
è
Clean blocked injection nozzle.
è
Install pulsation dampeners to
reduce pressure peaks if pipes
are too long.
è
Check function of safety valves.
Media sediment in dosing
head
è
Clean the dosing head.
Tab. 35: Type of fault: Diaphragm is torn or tears too often