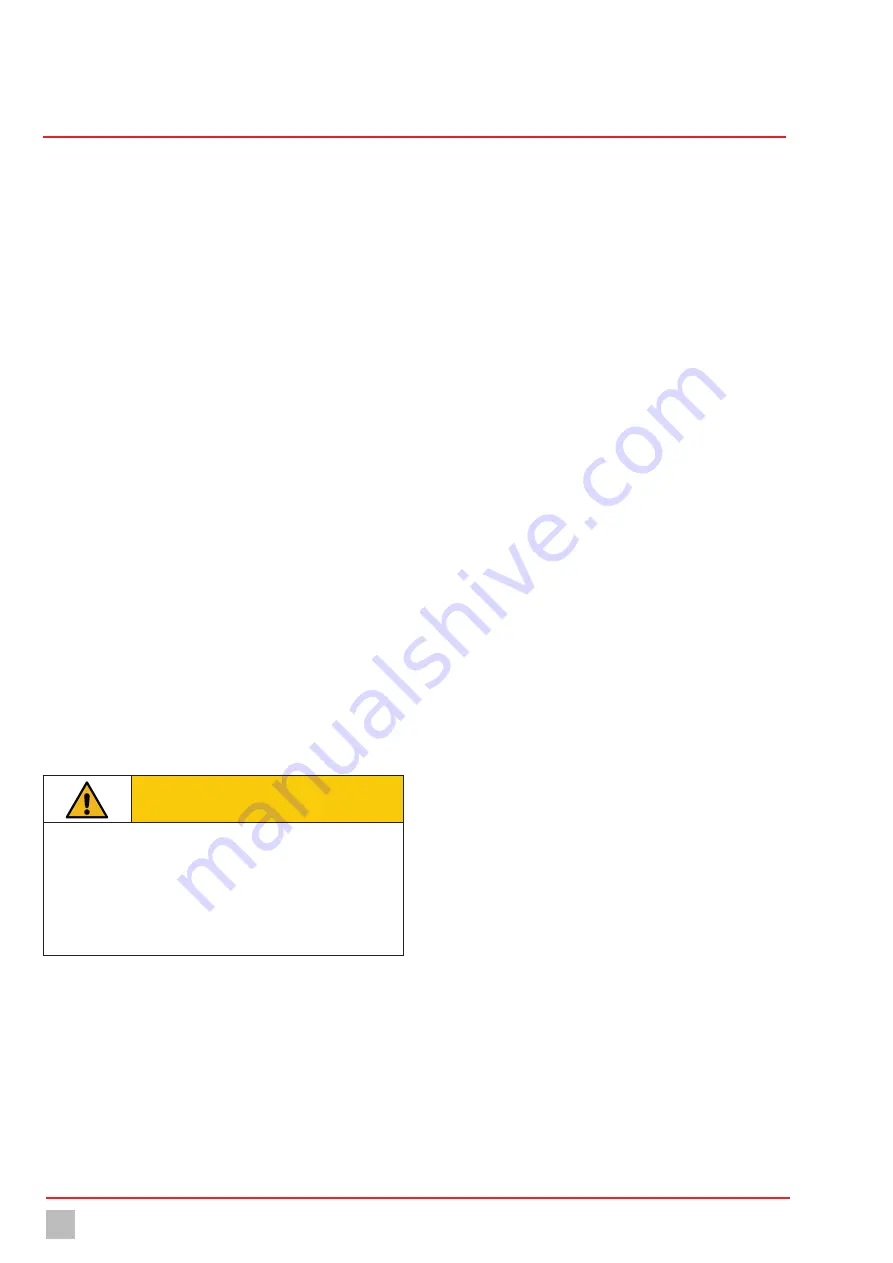
Hydraulic installations
20
© Lutz-Jesco GmbH 2020
BA-10491-02-V01
Piston diaphragm dosing pump
MEMDOS KMS LB/LA
Operating instructions
8.2 General installation
n
All piping must be fixed. The system piping must not exert any force
on the connections and valves of the dosing pump.
n
Clean and blow out all piping before connecting the piping to the
pump.
n
Apply pipe sealant economically and only to the external threads.
n
Do not connect pipes whilst the dosing head connections are connect-
ed to the pump.
n
The suction line may not be smaller than the pump connections.
n
The suction line should be straight and maintained as short as possi-
ble. It should also be fitted with the minimum possible number of
bends, T-pieces and other fittings.
n
To ensure easier pump maintenance, we recommend installing shut-
off valves: Do not install a shut-off valve between the pressure con-
nection and the system pressure control valve.
n
Installing a screen in front of the suction line provides protection
against foreign bodies.
n
The process system requires a separate safety valve to protect it
against excessive pressure. You should maintain an adequate safety
factor in plastic piping systems.
n
The installation of a bypass valve facilitates venting when starting a
pump, in order to permit the re-circulation procedure of the fluid back
to the tank.
8.3 System piping
n
This means that steel piping should be connected to the dosing pump
via flexible pipe sections.
n
The nominal diameters of the pipework and the installed fittings
should be rated the same as or greater than the nominal diameters of
the dosing pump's suction and pressure valves.
n
The suction line should be kept as short as possible.
n
You should avoid intertwined hoses.
n
Avoid loops, since air bubbles can collect.
CAUTION!
Danger of personal injury and material damage!
Before connecting connection pipes and fittings, first remove the dos-
ing head connections, otherwise unnecessary forces will impinge upon
the piping system.
ð
Remove the dosing head connections before connecting the con-
nection pipes and fittings.
8.4 Suction and pressure valves
These are single- or double-ball bearing or spring-loaded valves which
can only work properly when mounted in a vertical direction. The condi-
tion of the valves has a significant impact on the function and the dosing
accuracy of the dosing pump. All valves have arrows on them, these indi-
cate the flow direction. These arrows must always point upwards.
8.5 Hydraulic accessories
The following chapter is intended to give you an overview of installation
options.
Please note that these operating instructions are no substitute for the in-
structions supplied with the accessories in each case. The corresponding
documentation supplied with the product applies to safety information
and provides exact instructions on assembly.
8.5.1 Injection nozzle
If the pressure line enters a main line, it is advisable to install an injection
nozzle.
Injection nozzles have three main functions:
n
Dosing the medium into a main line
n
Preventing flowback into the pressure line through a non-return valve
Notes on assembly:
n
Double-ball injection nozzles must be installed into the main line verti-
cally from the bottom. You can install hose and spring-loaded injection
nozzles any way you like.
n
With dosing media that tend to crystallize, it is advisable to carry out
installation into the main line from the bottom. This prevents the inclu-
sion of air bubbles.
n
Many dosing media tend to contaminate the injection nozzles, which
can lead to blockages. In cases like this, it is advisable to install an in-
jection nozzle that is easy to dismantle and block off.
8.5.2 Pressure-relief valve
Pressure relief valves have an important safety function for protecting the
dosing pump and the associated pipes and fittings. The dosing pump can
generate a pressure that is many times the rated one. A blocked pressure
line can lead to dosing medium escaping.
Impermissibly high pressure can develop as follows:
n
the shut-off valves are closed even though the dosing pump is run-
ning,
n
pipes block.
At an appropriate pressure, a pressure relief valve opens a bypass line
and protects the system in this way from damage caused by over-pres-
sure.
Notes on assembly:
n
The line for returning dosing medium from the pressure relief valve
must be routed to the dosing tank or to a collecting pan.
n
The pressure in the dosing tank must not be too high so that it is pos-
sible to accommodate the returned dosing medium.
n
As an alternative, the system can return dosing medium into the suc-
tion line in front of the dosing pump. In this case, there must not be a
non-return valve or a foot valve in the suction line.
n
You should install the pressure relief valve as close as possible to the
dosing head.
8.5.3 Back-pressure valve
Back-pressure valves are required in the following cases:
n
There are considerably fluctuating system pressures