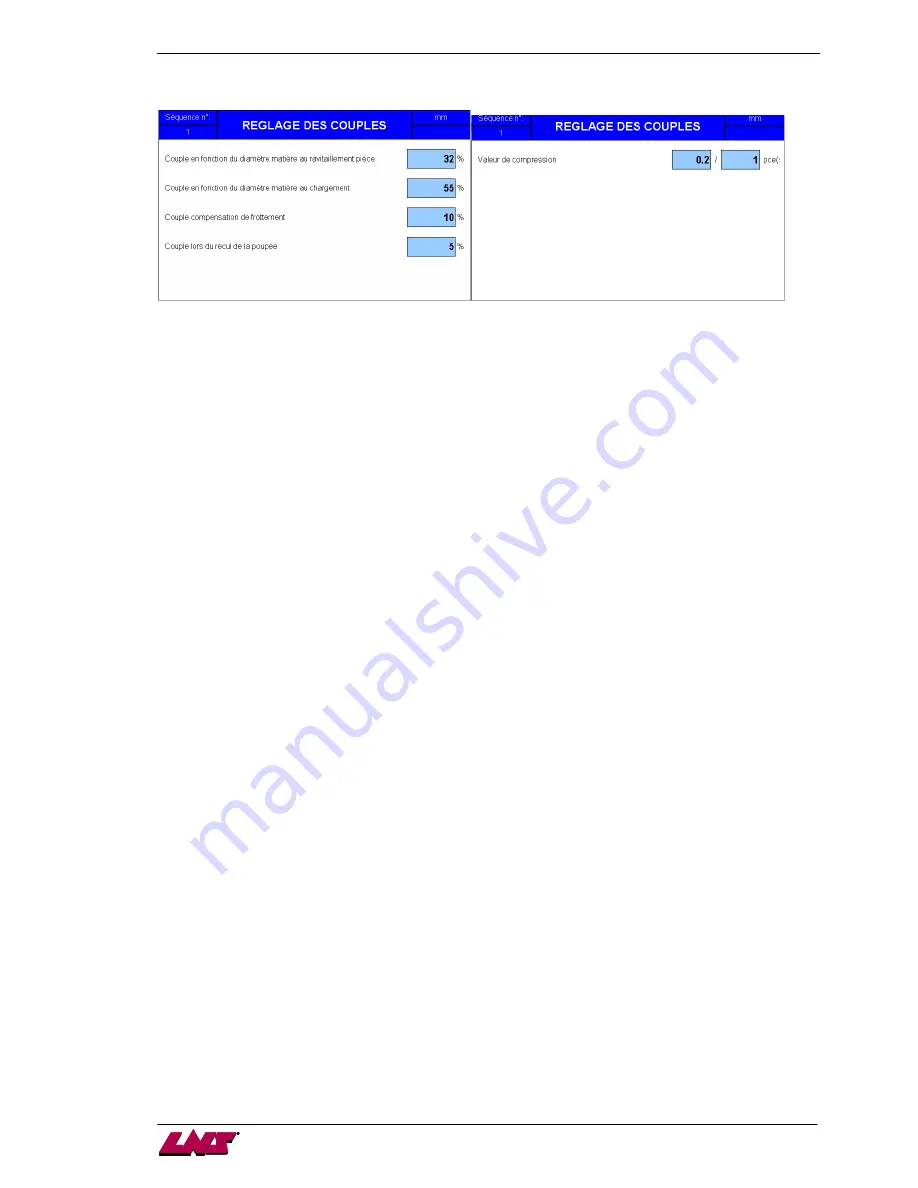
CHAPTER 8: HANDLING
81
EXPRESS 220 S2/320 S2
4.2.4. Torques
Depending on the diameter of the bar, the bar feed system will automatically select an appropriate
pushing torque and speed.
The operator may modify this selection if necessary.
When the material to be loaded has a high specific weight, the torque must be significant. The contrary
applies if the specific weight of the bars is low.
Torque set according to the diameter of the material for the bar loading (%)
This torque must be sufficient so that the bar can defeat the various frictions during positioning,
particularly in the clamp.
Depending on the bar diameter, the feeder suggests a suitable thrust torque.
Torque rate during loading according to bar diameter (%)
Same principle as for the couple fast forward, applied this time to loading.
Couple for compensation of friction during machining with tailstock Machine (%)
This torque must be sufficient so that the bar does not have to pull the pusher when the headstock
advances. However, if this force is excessive, when the headstock back, the bar can flex if it is of small
diameter.
Support Couple of the material against the machine tool during the recoil of the headstock with
the opening clamp (%)
This torque must be sufficient so that the bar remains pressed against the tool when the headstock back.
However, if this force is excessive, the tool may break.
Compression value
(only valid with the synchronization system and for a sliding headstock lathe)
This parameter sets the compression value of the bar to track the movement between the headstock and
the advance of the pusher.
It can be defined for the supply of each piece (indicate "1" in the right field) or all the parts X (indicate the
desired number in the right field).
Summary of Contents for Express 220 S2
Page 1: ......
Page 2: ......
Page 3: ......
Page 6: ...CHAPTER 1 BASIC PRINCIPLES 3 EXPRESS 220 S2 320 S2 CHAPTER 1 BASIC PRINCIPLES...
Page 12: ...CHAPTER 2 TECHNICAL DATA 9 EXPRESS 220 S2 320 S2 CHAPTER 2 TECHNICAL DATA...
Page 14: ...CHAPTER 2 TECHNICAL DATA 11 EXPRESS 220 S2 320 S2 2 1 Left front loading 3 m...
Page 15: ...12 CHAPTER 2 TECHNICAL DATA EXPRESS 220 S2 320 S2 2 2 Right front loading 3 m...
Page 16: ...CHAPTER 2 TECHNICAL DATA 13 EXPRESS 220 S2 320 S2 2 3 Left front loading 2 m...
Page 17: ...14 CHAPTER 2 TECHNICAL DATA EXPRESS 220 S2 320 S2 2 4 Right front loading 2 m...
Page 19: ...16 CHAPTER 2 TECHNICAL DATA EXPRESS 220 S2 320 S2...
Page 20: ...CHAPTER 3 SYSTEM START UP 17 EXPRESS 220 S2 320 S2 CHAPTER 3 SYSTEM START UP...
Page 26: ...CHAPTER 4 ELECTRICS 23 EXPRESS 220 S2 320 S2 CHAPTER 4 ELECTRICS...
Page 40: ...CHAPTER 5 PNEUMATICS 37 EXPRESS 220 S2 320 S2 CHAPTER 5 PNEUMATICS...
Page 45: ...42 CHAPTER 5 PNEUMATICS EXPRESS 220 S2 320 S2...
Page 46: ...CHAPTER 6 HYDRAULICS 43 EXPRESS 220 S2 320 S2 CHAPTER 6 HYDRAULICS...
Page 50: ...CHAPTER 7 GENERAL DESCRIPTION 47 EXPRESS 220 S2 320 S2 CHAPTER 7 GENERAL DESCRIPTION...
Page 64: ...CHAPTER 8 HANDLING 61 EXPRESS 220 S2 320 S2 CHAPTER 8 HANDLING...
Page 96: ...CHAPTER 8 HANDLING 93 EXPRESS 220 S2 320 S2...
Page 97: ...94 CHAPTER 8 HANDLING EXPRESS 220 S2 320 S2...
Page 98: ...CHAPTER 9 MALFUNCTIONS MAINTENANCE 95 EXPRESS 220 S2 320 S2 CHAPTER 9 MALFUNCTIONS MAINTENANCE...
Page 109: ...106 CHAPTER 9 MALFUNCTIONS MAINTENANCE EXPRESS 220 S2 320 S2 3 SERVO AMPLIFIER ALARMS...
Page 110: ...CHAPTER 9 MALFUNCTIONS MAINTENANCE 107 EXPRESS 220 S2 320 S2...
Page 111: ...108 CHAPTER 9 MALFUNCTIONS MAINTENANCE EXPRESS 220 S2 320 S2...
Page 112: ...CHAPTER 9 MALFUNCTIONS MAINTENANCE 109 EXPRESS 220 S2 320 S2...
Page 113: ...110 CHAPTER 9 MALFUNCTIONS MAINTENANCE EXPRESS 220 S2 320 S2...
Page 115: ...112 CHAPTER 9 MALFUNCTIONS MAINTENANCE EXPRESS 220 S2 320 S2...
Page 116: ...CHAPTER 10 APPENDICES 113 EXPRESS 220 S2 320 S2 CHAPTER 10 APPENDICES...