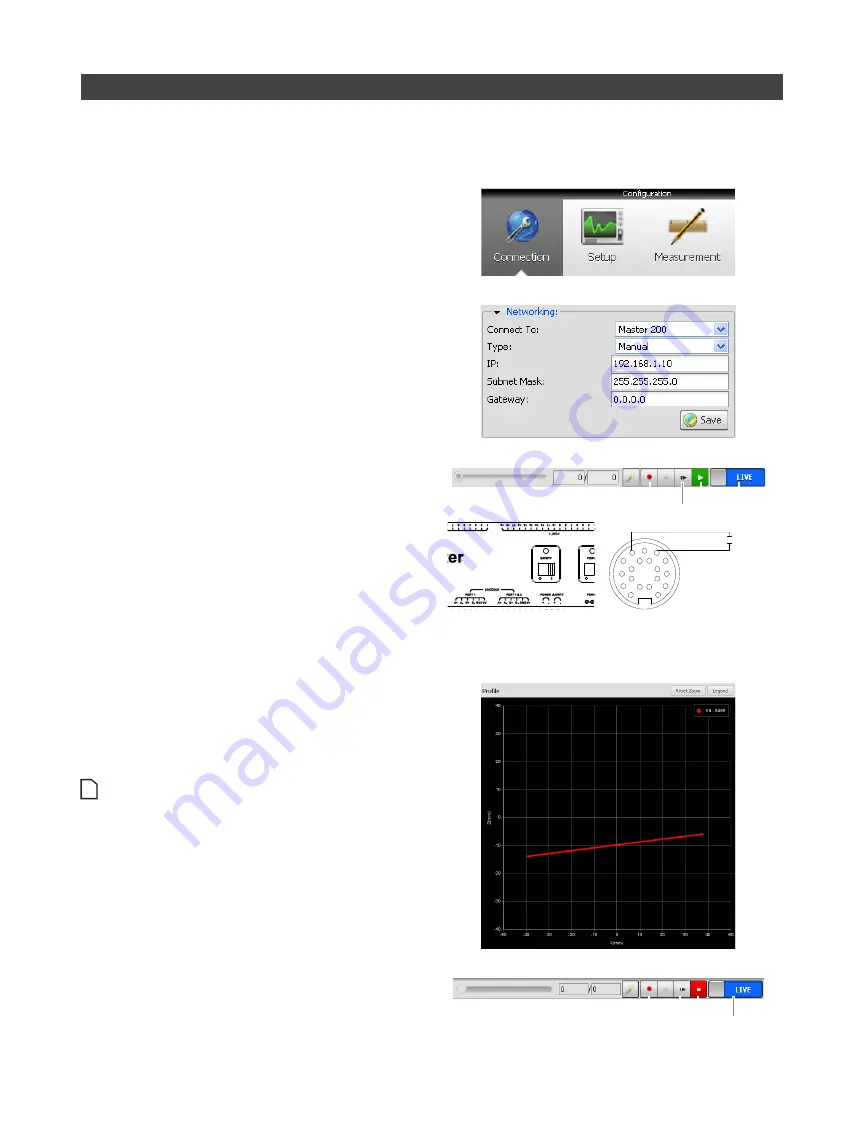
Getting Started • 29
Gocator 2000 Family
Running a Sensor for the First Time
After connecting, laser profiling can be exercised to verify basic sensor operation.
To run a sensor for the first time:
1
Select the Connection Page.
2
Specify the Connect To setting.
The Connect To setting specifies whether the
sensor system is standalone, connected to a Master
200 or a Master 400/800/1200/2400. For single
sensor operations select Standalone or Master 200.
3
Ensure that the Data Source selector is
showing LIVE.
RECORD
SNAPSHOT
START
DATA SOURCE
4
Ensure that the Laser Safety Switch is enabled
or the Laser Safety input is high.
5
Select the Setup Page.
6
Press the Start Button to start the sensor.
The Start Button is used to run sensors
continuously, while the Snapshot Button is used to
trigger a single profile.
Master 200
Sa
5V - 48VDC
Safety_in-
Standalone
7
Move a target into the laser plane.
If a target object is within the sensor’s measurement
range, the Data Viewer will display the shape of the
target and the sensor’s Range Indicator LED will
illuminate.
If you cannot see the laser, or if a profile is
not displayed in the Data Viewer, refer to the
Troubleshooting section (page 160) in this guide.
8
Press the Stop Button.
You should now see the laser turn off.
RECORD
SNAPSHOT
STOP
DATA SOURCE
Summary of Contents for Gocator 2000 Family
Page 1: ...User s Manual Gocator 2000 Family Version 2 2 1 0 Revision A...
Page 164: ...Specifications 164 Gocator 2000 Family Envelope 61 25 40 5 4 15 82 9 95 7...
Page 166: ...Specifications 166 Gocator 2000 Family Envelope 33 90 80 2 9 84 3 99 7 10 6...
Page 168: ...Specifications 168 Gocator 2000 Family Envelope 190 210 33 141 3 155 7 4 11...
Page 170: ...Specifications 170 Gocator 2000 Family Envelope 33 300 400 214 9 229 2 10 3 3 2...
Page 172: ...Specifications 172 Gocator 2000 Family Envelope 33 400 500 216 2 230 6 3 9 11...