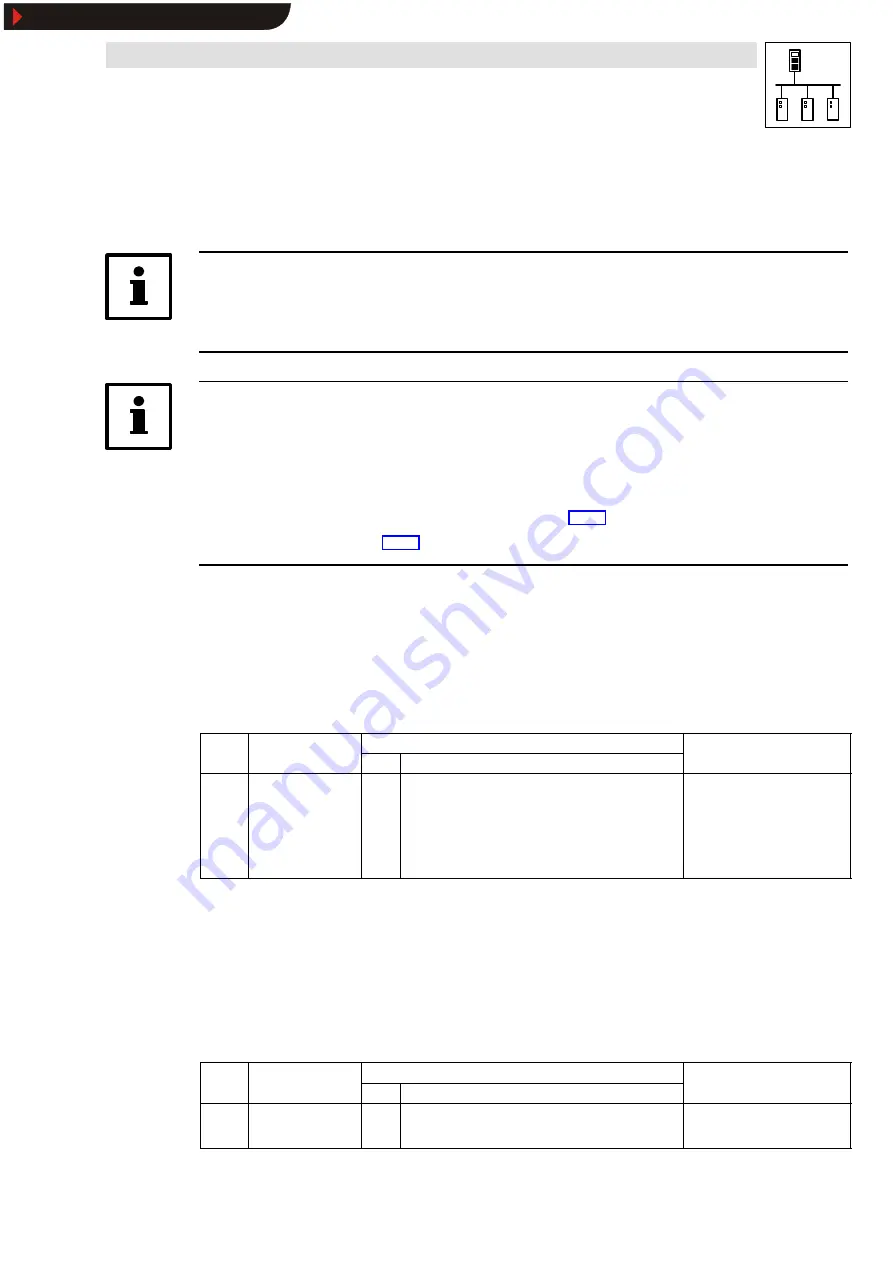
System bus (CAN) with Servo PLC & Drive PLC
Configuration (AIF interface)
4-1
l
PLC-Systembus EN 1.1
4
Configuration (AIF interface)
With an appropriate fieldbus module (e.g. 2175), you can use the AIF interface of the 9300 Servo PLC
or Drive PLC as an additional system bus interface.
Note!
If the fieldbus module plugged on the AIF interface and the integrated system bus interface are
connected to the
same
system bus network, please ensure that you have set
different
CAN
addresses and
different
identifiers for the interfaces!
Tip!
Changes in the CAN baud rate, the CAN addresses and the PDO identifiers are only accepted after
a reset node.
A reset node can be initiated by
•
A fresh power-on
•
a reset node command through an NMT command
•
a reset node via C0358
4.1
CAN baud rate
All participants must use the same baud rate for data transmission to enable communication via the
system bus.
•
The baud rate is configured via code C2351:
Code
LCD
Possible settings
Info
Lenze Choice
C2351 XCAN baud rate
0
0
500 kbit/s
1
250 kbit/s
2
125 kbit/s
3
50 kbit/s
4
1000 kbit/s
5
20 kbit/s
6
10 kbit/s
System bus baud rate
•
Save changes with C0003 = 1
•
Changes will only become
effective after a reset node!
4.2
CAN boot-up
Unless a higher-level host system controls the system bus initialisation and the status change from
pre-operational to operational, you can select a PLC or a drive controller as a “ quasi” master to fulfil
this task.
•
Configuration is made via code C2352:
Code
LCD
Possible settings
Info
Lenze Choice
C2352 XCAN mst
0
0
Boot-up not active
1
Boot-up active
Controller sends system bus
boot-up and is therefore “quasi”
master
Show/Hide Bookmarks