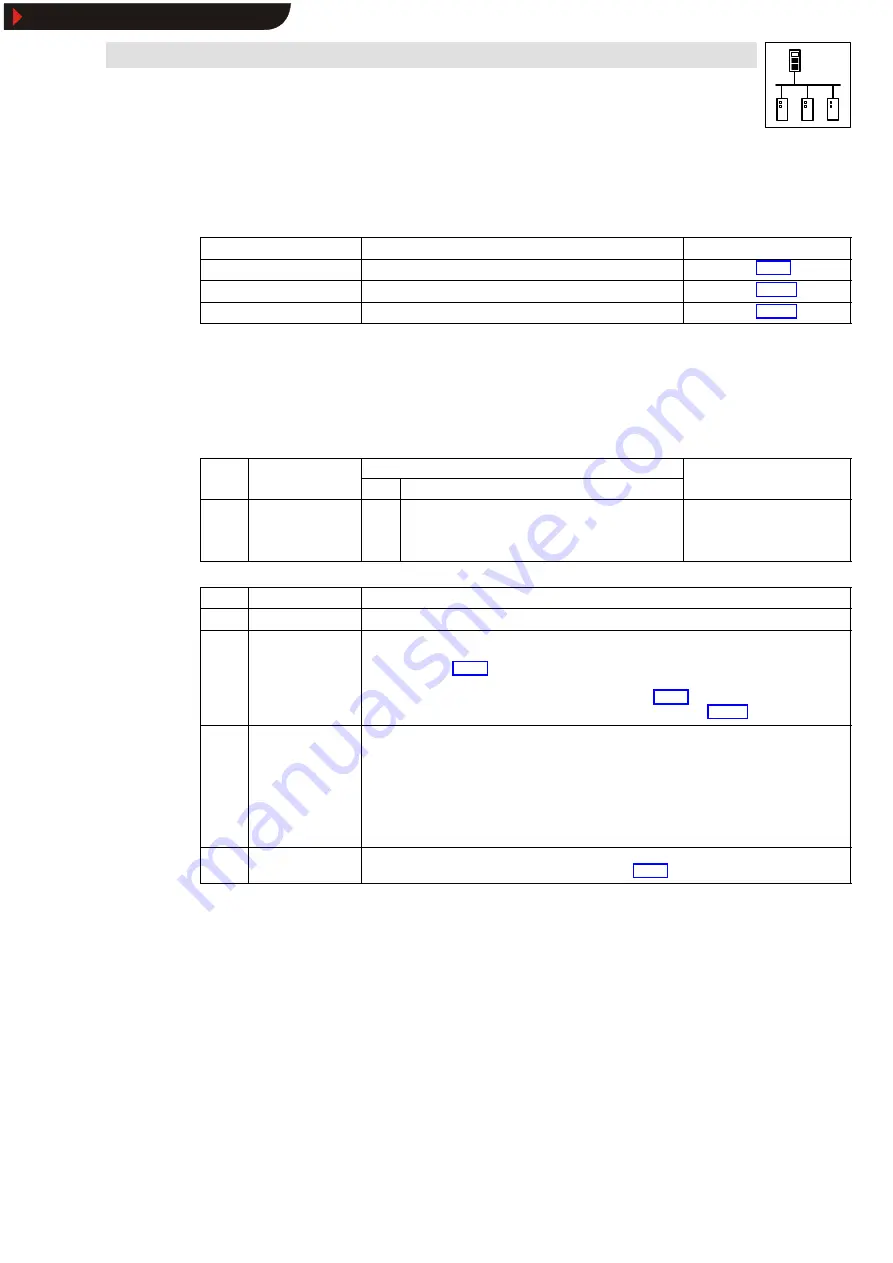
System bus (CAN) with Servo PLC & Drive PLC
Configuration
3-9
l
PLC-Systembus EN 1.1
3.11
Diagnostics
The following codes can be used for diagnostics:
Code
Display information
Info
C0359
Operating state of the system bus
Chapter 3.11.1
C0360
Number of transmitted and received telegrams
Chapter 3.11.2
C0361
Bus load (in %)
Chapter 3.11.3
•
Settings cannot be made via these codes.
3.11.1
Operating state of the system bus
Via C0359 you can display the operating state of the system bus:
Code
LCD
Possible settings
Info
Lenze Choice
C0359 CAN state
g
0
operational
1
Pre-operational
2
Warning
3
Bus Off
System bus status
C0359
Operating state
Info
0
operational
The system bus is operational. The PLC can transmit & receive parameter and process data.
1
Pre-operational
The PLC can transmit & receive parameter data.Process data are ignored.
A status change from
pre-operational
to
operational
can be initiated by:
•
the CAN master
•
a reset node
– via C0358, if the PLC was configured as a “quasi” master.
– via the binary input signal “reset node” at the
CAN_Management SB
2
Warning
The PLC has received faulty telegrams and no longer takes an active part in the system bus, i.e. it is no
longer possible to transmit data from the PLC.
Possible causes:
•
A missing bus termination
•
Insufficient screening
•
Potential differences in the grounding of the control electronics
•
the bus load is too high
•
The PLC is not connected to the system bus
3
Bus Off
The PLC has decoupled itself from the system bus because too many faulty telegrams were received.
•
The reaction to this status can be configured via C0595.
Show/Hide Bookmarks