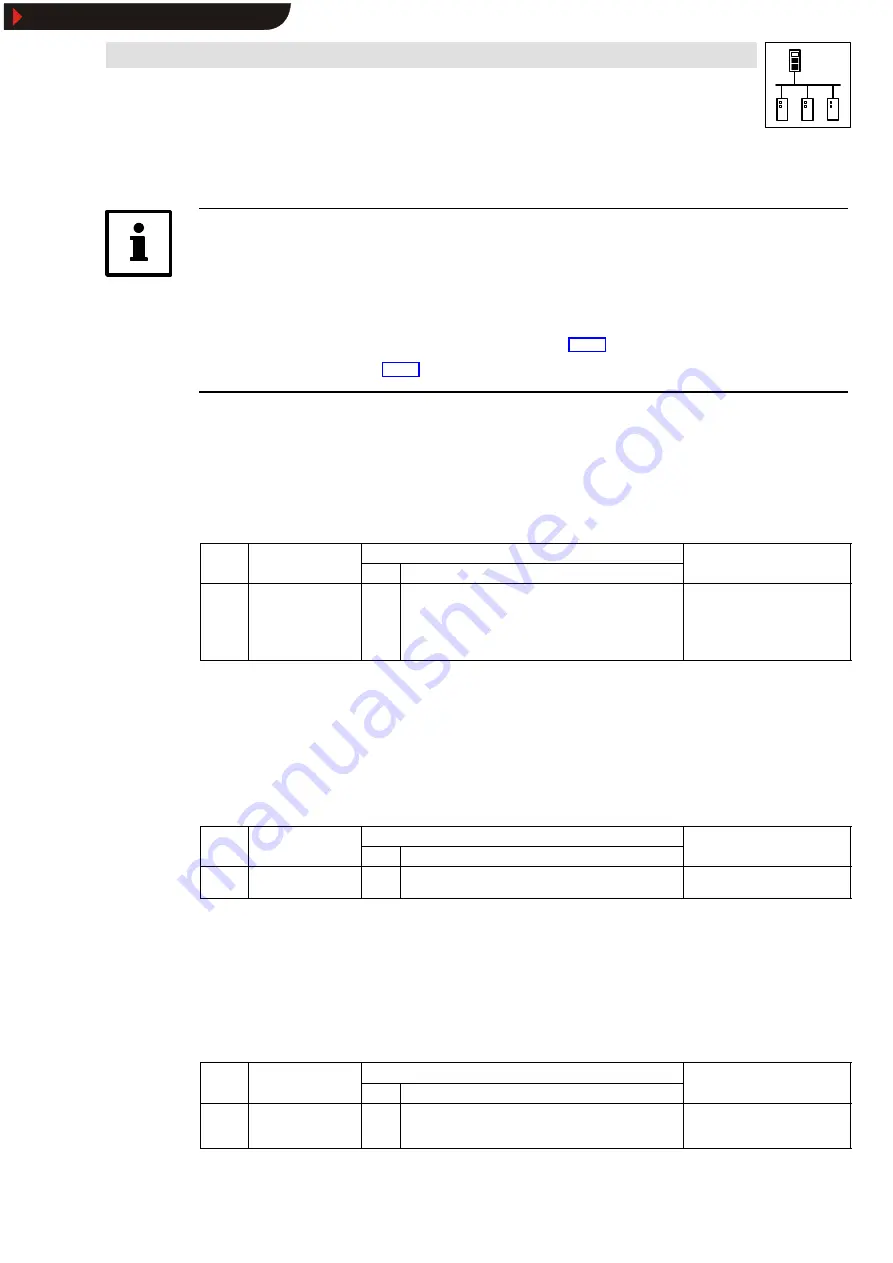
System bus (CAN) with Servo PLC & Drive PLC
Configuration
3-1
l
PLC-Systembus EN 1.1
3
Configuration (integrated system bus interface)
Tip!
Changes in the CAN baud rate, the CAN addresses and the PDO identifiers are only accepted after
a reset node.
A reset node can be initiated by
•
a fresh power-on
•
a reset node command through an NMT command
•
a reset node via C0358
3.1
CAN baud rate
All participants must use the same baud rate for data transmission to enable communication via the
system bus.
•
The baud rate is configured via code C0351:
Code
LCD
Possible settings
Info
Lenze Choice
C0351 CAN baud rate
0
0
500 kbit/s
1
250 kbit/s
2
125 kbit/s
3
50 kbit/s
4
1000 kbit/s
System bus baud rate
•
Save changes with C0003 = 1
•
Changes will only become
effective after a reset node!
3.2
CAN boot-up
Unless a higher-level host system controls the system bus initialisation and the status change from
pre-operational to operational, you can select a PLC or a drive controller as a “ quasi” master to fulfil
this task.
•
Configuration is made via code C0352:
Code
LCD
Possible settings
Info
Lenze Choice
C0352 CAN mst
0
0
Boot-up not active
1
Boot-up active
Delay time for system bus initialisation (boot-up)
Some bus participants (e.g. HMIs) need a certain start-up time after power-on before they can
accept NMT commands from the master to switch to
operational.
You can set a delay time to be observed after power-on before NMT commands are transmitted to
ensure that all bus participants, even the one with the longest start-up time, are really ready to
receive the NMT commands.
•
The delay time is configured via code C0356/1:
Code
LCD
Possible settings
Info
Lenze Choice
C0356/1 CAN boot-up
3000
0
{1 msec}
65000 Delay time after power-on for
initialisation through the “quasi”
master
Show/Hide Bookmarks