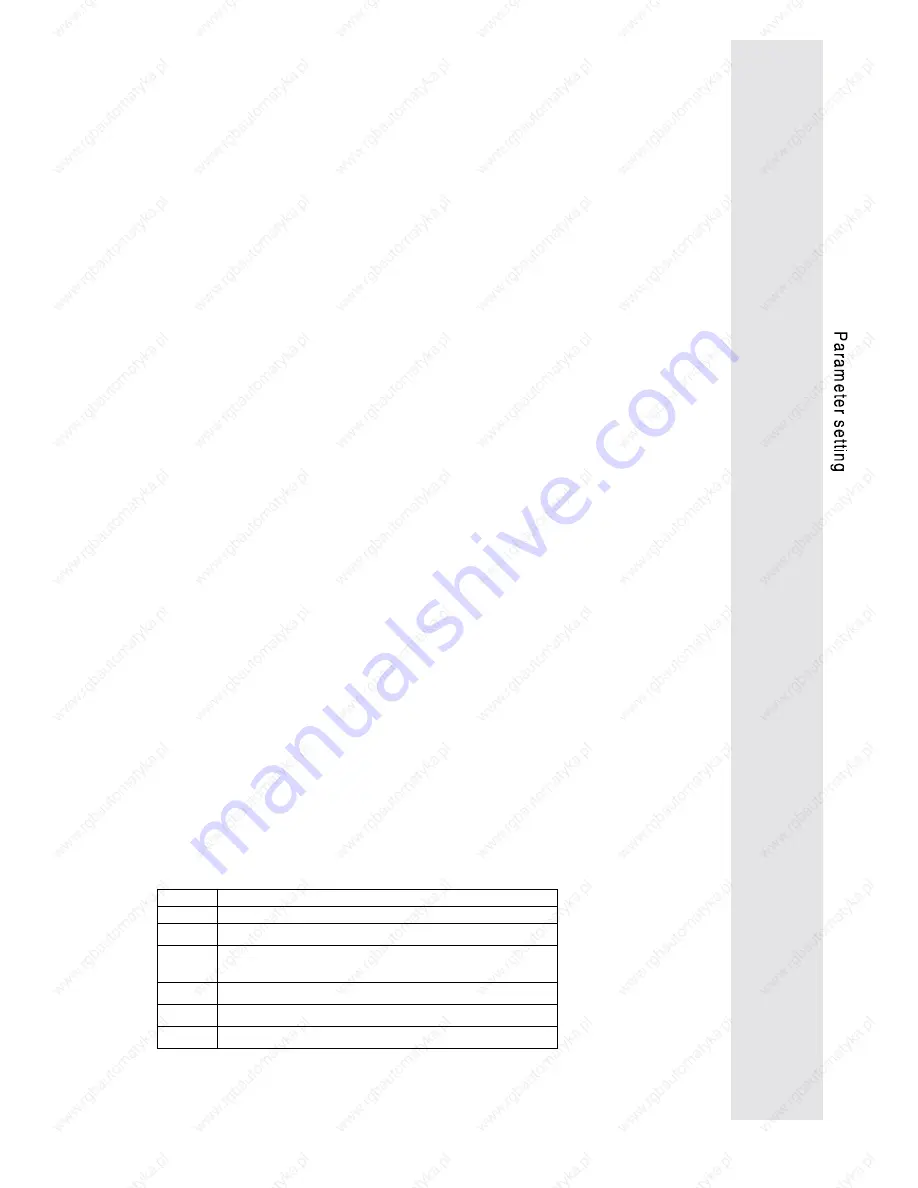
53
4.1.2. Setting
These setting instructions are meant as guideline and must not
always decelerate the machine to standstill before reaching the
undervoltage threshold. The parameter setting of the codes, which
influences the DC-bus control during mains failure detection (C079,
C080, C228, C236, C237), depend on the size of the drive
configurations and the mechanical features of the system.
There are minimum speeds at which the energy of the mechanical
system is not high enough to compensate the losses which occur
during the controlled deceleration (switched-mode power supplies,
inverter, machines).
Aim:
•
The aim is to have a controlled speed deceleration that allows a
DC-bus voltage value which remains higher than the
undervoltage threshold for as long as possible.
As soon as the value falls below this threshold, pulse inhibit will
be set and the drive will coast to standstill.
•
The brake chopper should not be activated during the controlled
deceleration of the speed.
Therefore, the parameter setting of the DC-bus control should
be "softly". It is not very important whether the DC-bus can be
loaded to the voltage set under C236.
Required measuring units:
•
Oscilloscope,
at least 2 channels, if possible with memory.
Test set-up:
•
Connect channel 1 of the oscilloscope with X5,62 of the axis
module (speed monitor).
•
Connect channel 2 of the oscilloscope with X3,2 of the supply
module (DC-bus monitor).
•
If available, connect channel 3 of the oscilloscope with X5,44 of
the axis module (RDY-output).
Presettings:
1. Set the speed controller of the axis module drive configuration
as usual.
2. Activate the mains failure detection of the master drive (C229 =
-1-).
If the function is activated, the RDY-output changes from the
HIGH level to the LOW level. As soon as the speed is
decelerated to 0, the RDY-output re-changes to HIGH.
3. The relevant codes must be set as follows:
Code
Presetting
C079
-1-
C080
150 s
C228
1/10...1/20 of the natural slow-down time of the machine at
maximum operating speed
C229
-1-
C236
680 V
C237
1000 rpm or more
Summary of Contents for 9212
Page 3: ...EDB9200_E GB 00375316 Antriebstechnik Operating Instructions Servo controller 9200 series ...
Page 32: ...28 5 2 Wiring with positioning control SX 1 5 2 1 Diagram 1 Mains supply ...
Page 33: ...29 5 2 2 Diagram 2 Control circuit 230V ...
Page 34: ...30 5 2 3 Diagram 3 Control circuit 24V ...
Page 35: ...31 5 2 4 Diagram 4 Control connections 9200 SX1 Ω ...
Page 36: ...32 5 2 5 Diagram 5 Control connections SX1 ...