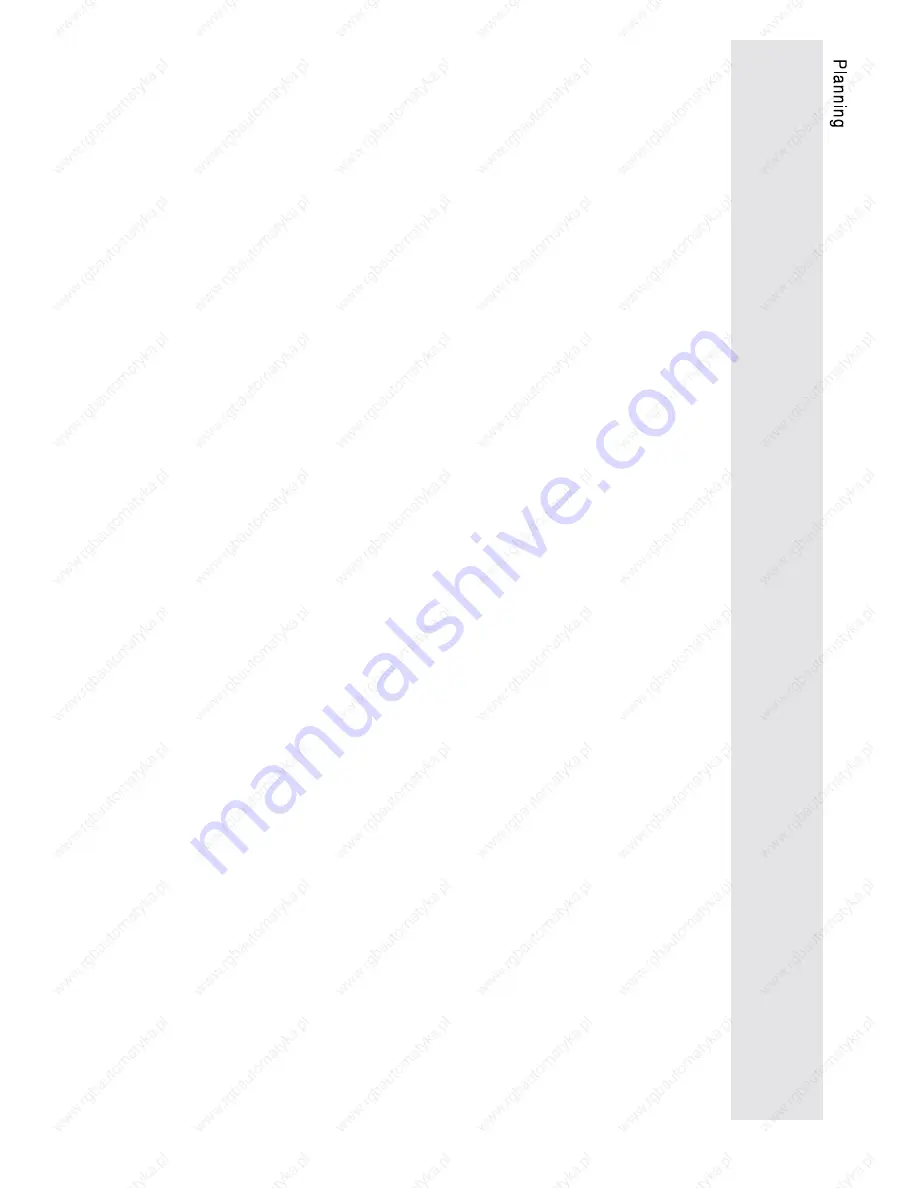
9
2.6.
Manufacturer's certification
We hereby certify that the below listed electronic controllers are
control components for variable speed motors intended for the
assembly into machines or together with other components to form
a machine. According to the "Council directive ... relating to
machinery" 89/392/EWG, our controllers are no machines.
The Operating Instructions supplied together with the controllers
give advice and recommendations for the installation and use of the
electronic equipment.
As long as the conformity with the protection and safety
requirements of the "Council directive ... relating to machinery"
89/392/EWG and its amendment 91/368/EWG is not proved,
operation of the machine is prohibited.
The measures required for typically configurated controllers to
comply with the EMC limit values are indicated in the Operating
Instructions. The electromagnetic compatibility of the machine
depends on the method and accuracy of the installation. The user
is responsible for the compliance of the machine with the "Council
directive ... relating to electromagnetic compatibility" 89/336/EWG
and its amendment 92/31/EWG.
Considered standards and regulations:
•
Electronic equipment for use in electrical power installations and
their assembly into electrical power installations: DIN VDE 0160,
5.88 (pr EN 50178)
•
Standards for the erection of power installations:
DIN VDE 0100
•
IP - enclosures: EN 60529, 10.91
•
Base material for printed circuits:
DIN IEC 249 part 1, 10.90; DIN IEC 249 part 2-15, 12.89
•
Printed circuits, printed boards:
DIN IEC 326 part 1, 10.90; EN 60097, 9.93
•
Creepage distances and clearances:
DIN VDE 0110 part 1-2, 1.89; DIN VDE 0110 part 20, 8.90
•
Electrostatic discharge (ESD):
prEN 50082-2, 8.92, IEC 801-2, 9.87 (VDE 0843, part 2)
•
Electrical fast transient interference (Burst):
prEN 50082-2, 8.92, IEC 801-4, 9.87 (VDE 0843, part 4)
•
Surge immunity requirements: IEC 801-5,10.93
•
Radio interference suppression of electrical equipment and
plants:
EN 50081-2, 3.94; EN 55011 (VDE 0875, part 11,7.92)
•
Radio interference suppression of radio frequency equipment
for industrial purposes: VDE 0871, 6.78
Summary of Contents for 9212
Page 3: ...EDB9200_E GB 00375316 Antriebstechnik Operating Instructions Servo controller 9200 series ...
Page 32: ...28 5 2 Wiring with positioning control SX 1 5 2 1 Diagram 1 Mains supply ...
Page 33: ...29 5 2 2 Diagram 2 Control circuit 230V ...
Page 34: ...30 5 2 3 Diagram 3 Control circuit 24V ...
Page 35: ...31 5 2 4 Diagram 4 Control connections 9200 SX1 Ω ...
Page 36: ...32 5 2 5 Diagram 5 Control connections SX1 ...