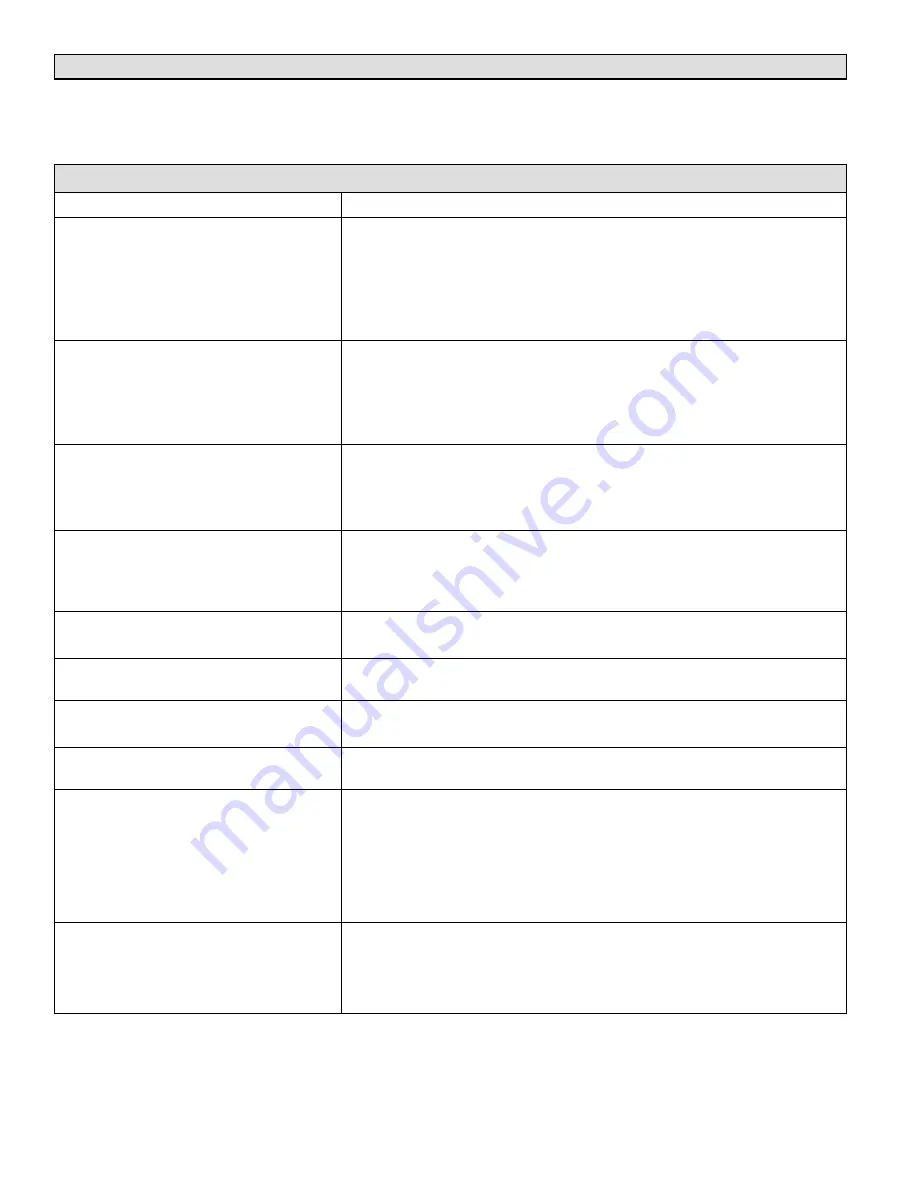
Page 18
Troubleshooting
Burner failure or improper operation can result from a num-
ber of different causes. Often the cause can be pinpointed
by observing the different types of failure or by the process
of elimination.
The following troubleshooting charts list some failures,
causes and a sequence of steps to isolate the point of fail-
ure. Check the simplest and most obvious items before
progressing to other items.
Troubleshooting: Fan board operating sequence
Action
System Response
Thermostat calls for heat.
(W terminal is energized.)
ST9103A closes oil primary control T−T connections.
Ignition system and oil primary control start the furnace. Oil flows as long
as oil primary control senses flame.
Burner motor is energized and heat fan on delay timing begins. When tim-
ing is complete, the circulating fan is energized at heat speed and warm
air is delivered to the controlled space.
Thermostat ends call for heat.
(W terminal is de−energized.)
Oil primary control is de−energized, terminating the burner cycle.
Heat fan off delay timing begins. When timing is complete, the circulating
fan is de−energized.
ST9103A returns to standby mode (oil primary control and circulating fan
are off).
Burner fails to light.
Oil primary control locks out within lockout timing (timing depends on oil
primary control).
Burner motor is de−energized.
If heat fan has started, it continues through the selected delay off period.
Established flame fails.
Burner motor is de−energized and oil primary control goes into recycle
mode.
If selected heat fan off delay is longer than the recycle delay timing, the
heat fan continues to run through the next trial for ignition.
Thermostat begins call for cool.
(G and Y terminals are energized.)
Circulating fan is energized at the cool speed.
Cooling compressor turns on immediately.
Thermostat ends call for cool.
(G and Y terminals are de−energized.)
Circulating fan and cooling compressor turn off immediately.
Thermostat begins call for fan.
(G terminal is energized.)
Circulating fan is energized immediately at cool speed.
ST9103A may be factory−configured to operate heat speed in this mode.
Thermostat ends call for fan.
(G terminal is de−energized.)
Circulating fan is de−energized.
Limit switch string opens.
Oil primary control shut off the burner.
Circulating fan is energized immediately at heat speed.
ST9103A opens oil primary control T−T connections.
Circulating fan runs as long as limit string stays open.
If there is a call for cooling or fan, the circulating fan switches from heat
speed to cool speed.
Limit switch string closes.
ST9103A begins heat fan off delay sequence.
Circulating fan turns off after the selected heat fan off delay timing.
ST9103A closes oil primary control T−T connections.
Oil primary control is energized, initiating burner light off.
table continued on next page