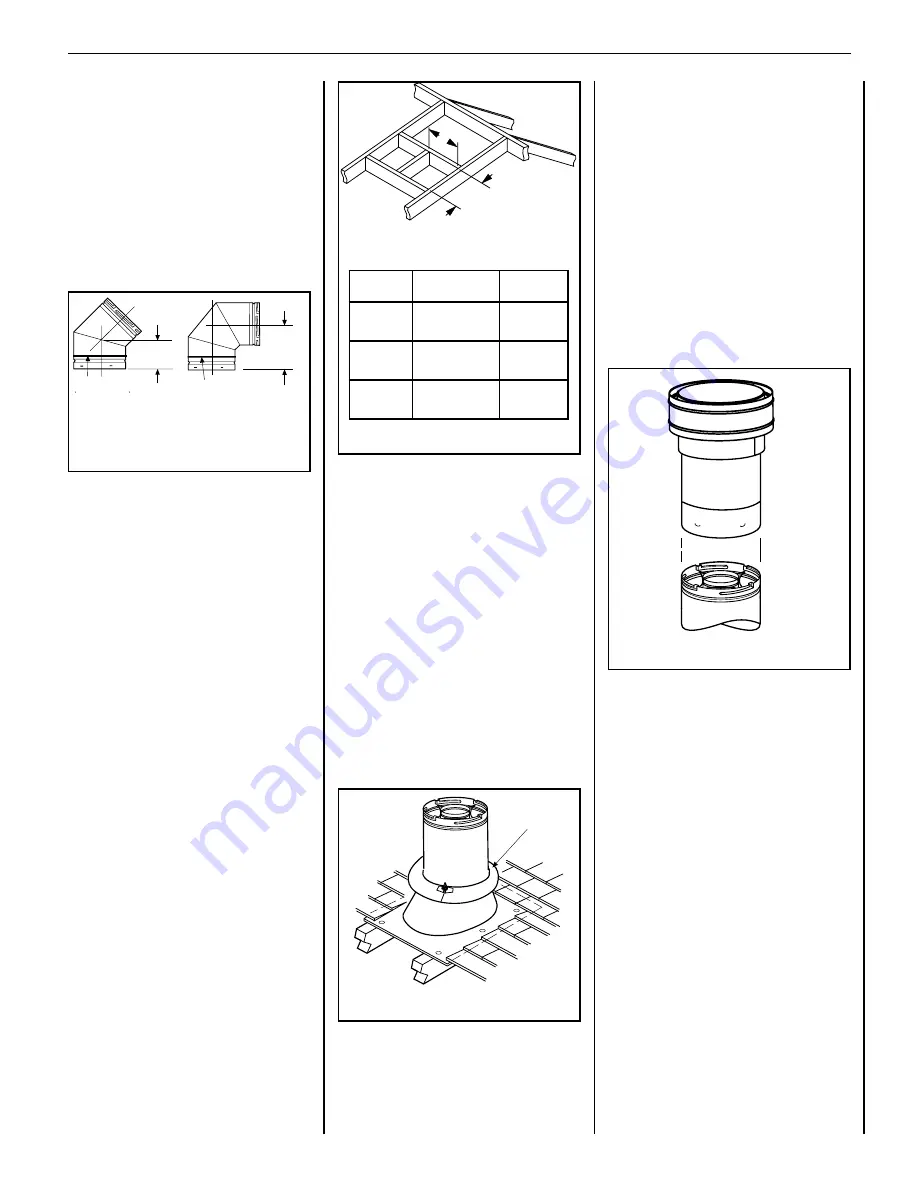
15
NOTE: DIAGRAMS & ILLUSTRATIONS ARE NOT TO SCALE.
LENNOX HEARTH PRODUCTS • MERIT PLUS
®
DIRECT VENT GAS FIREPLACES (MPD33/35/40/45) • INSTALLATION INSTRUCTIONS
Figure 24
Figure 26
Figure 25
If the vent system extends more than 5' (1.5
m) above the roof flashing, stabilizers may be
necessary. Additional screws may be used at
section joints for added stability. Guide wires
may be attached to the joint for additional sup-
port on multiple joint configurations.
G.
Continue installation of horizontal/inclined
sections -
Continue with the installation of the
straight vent sections in horizontal/inclined run
as described in
Step C.
Install support straps
every 5 ft (1.52 m) along horizontal/inclined
vent runs using conventional plumber’s tape.
It is very important that the horizontal/inclined
run be maintained in a straight (no dips),
slightly elevated plane. The recommended
incline is approximately 1/4" per foot (20 mm
per meter) horizontal, in a direction away from
the fireplace.
The rise per foot run ratios that
are smaller are acceptable all the way down
to at or near level.
Use a carpenter’s level to
measure from a constant surface and adjust
the support straps as necessary.
It is important to maintain the required
clearances to combustibles: 1" (25 mm) at all
sides for all vertical runs; and 3" (76 mm) at
the top, 1" (25 mm) at sides, and 1" (25 mm)
at the bottom for all horizontal/inclined runs.
H.
Frame roof opening -
Identify location for
vent at the roof. Cut and/or frame opening per
Roof Framing Chart and
Figure 24
.
F. Change vent direction to horizontal/inclined
run -
At transition from or to a horizontal/
inclined run, install the SV4.5E45 and SV4.5E90
elbows in the same manner as the straight vent
sections. The elbows feature a twist section to
allow them to be routed about the center axis
of their initial collar section to align with the
required direction of the next vent run element.
Twist elbow sections in a clockwise direction
only so as to avoid the possiblity of unlocking
any of the previously connected vent sections.
See
Figure 23
.
Figure 23
SV4.5E90
(90
°
Elbow)
8-1/8"
(206 mm)
Swivel Joint
(360
°
swivel)
4-13/16"
(122 mm)
SV4.5E45
(45
°
Elbow)
Swivel Joint
(360
°
swivel)
C
D
Storm
Collar
K. Install the vertical termination -
The final
step involves installation of the SV4.5CGV-1
Vertical Termination. Extend the vent sections
to the height as shown in the "Vertical vent
termination section" on
Page 6
. The SV4.5CGV-1
Vertical Termination (
Figure 26
) installs in the
exact same fashion as any other
Secure Vent
®
section. Align the termination over the end of
the previously installed section, adjusting the
radial alignment until the four locking dimples
of the termination are aligned with the inlets of
the four incline channels of the last vent section.
Push the termination down until it fully engages,
then twist the termination clockwise running the
dimples down and along the incline channels
until they seat at the end of the channels.
I.
Install the roof flashing -
Extend the vent
sections through the roof structure. Install the
roof flashing over the vent section and posi-
tion such that the vent column rises vertically
(use carpenters level) (
Figure 25
). Nail along
perimeter to secure flashing or adjust roofing to
overlap the flashing edges at top and sides only
and trim where necessary. Seal the top and both
sides of the flashing with waterproof caulking.
J. Install the storm collar -
Install the storm
collar, supplied with the flashing, over the vent/
flashing joint. See
Figure 25
.
Loosen the storm
collar screw. Slide collar down until it meets
the top of the flashing. Tighten the adjusting
screw. Apply non-combustible caulking or
mastic around the circumference of the joint
to provide a water tight seal.
Pitch
C
d
0/12
10-1/2"
(267 mm)
10-1/2"
(267 mm)
6/12
10-1/2"
(267 mm)
12"
(305 mm)
12/12
10-1/2"
(267 mm)
17-3/4"
(451 mm)
Framing dimensions for Roof