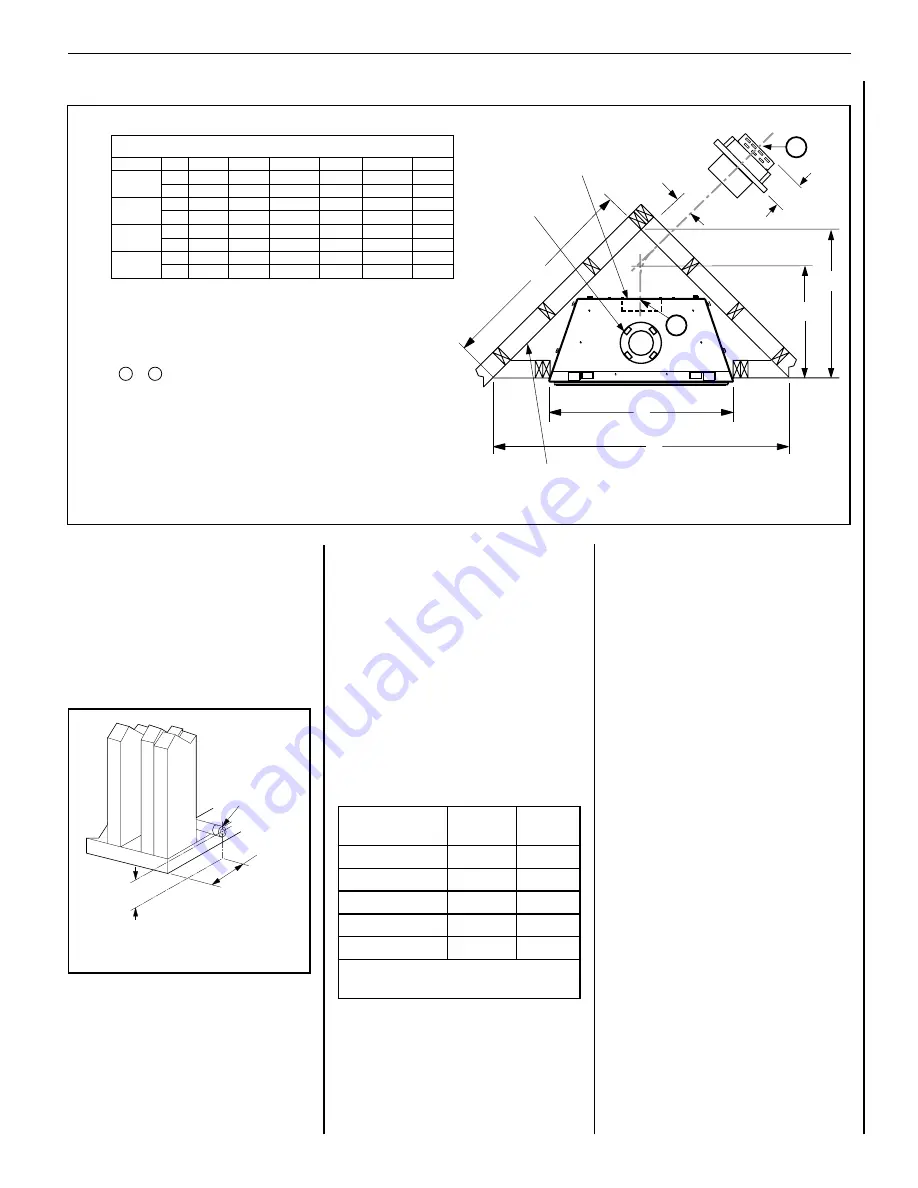
11
NOTE: DIAGRAMS & ILLUSTRATIONS ARE NOT TO SCALE.
LENNOX HEARTH PRODUCTS • MERIT PLUS
®
DIRECT VENT GAS FIREPLACES (MPD33/35/40/45) • INSTALLATION INSTRUCTIONS
FIREPLACE FRAMING SPECIFICATIONS
Schedule 40 Pipe
Length (feet)
Natural
Gas
Propane
Gas
0-10
1/2"
3/8"
10-40
1/2"
1/2"
40-100
1/2"
1/2"
100-150
3/4"
1/2"
150-200
3/4"
1/2"
Table 6 - Schedule 40 Black Iron Pipe -
Inside Diameter
Proper Sizing of Gas Line
Properly size and route the gas supply line
from the supply regulator to the area where the
appliance is to be installed per requirements
outlined in the National Fuel Gas Code, NFPA
54 - latest edition (USA) or CAN/CGA-B149.1
- latest edition (Canada).
Step 2. ROUTING GAS LINE
Route a 1/2" (13 mm) gas line to the left side
of the appliance as shown in
Figure 14
. Gas
lines must be routed, constructed and made
of materials that are in strict accordance with
local codes and regulations. All appliances
are factory-equipped with a flexible gas line
connector and 1/2" shutoff valve.
(See
Step
7
on
Page 26
)
.
Never use galvanized or plastic pipe. Refer to
Table 6
for proper sizing of the gas supply
line, if black iron pipe is being used. Gas lines
must be routed, constructed and made of
materials that are in strict accordance with
local codes and regulations. We recommend
that a qualified individual such as a plumber
or gas fitter be hired to correctly size and route
the gas supply line to the appliance. Installing
a gas supply line from the fuel supply to the
appliance involves numerous considerations
of materials, protection, sizing, locations,
controls, pressure, sediment, and more.
Certainly no one unfamiliar and unqualified
should attempt sizing or installing gas piping.
Figure 13 - Corner Framing with Horizontal Termination
Also see
Figure 12.
Figure 14 - Route Gas Line
3"
(76 mm)
Left Side Front
Corner of Fireplace
Framing
6-1/2"
(152 mm)
Pipe Coupling
(Recommended)
NOTE:
•
Rear Vent Applications in Corner Installations:
The horizontal vent length
(from
a
to
b
) must not exceed 28 inches (711 mm).
•
MPdT33 and MPdR33 Models:
Dimensions
A through F
occur when one
45-degree elbow is connected directly to the appliance collar.
•
MPd35, MPd40, and MPd45 Models:
Dimensions
d through F
occur when
one 45-degree elbow is connected directly to the appliance collar.
Notes:
• All appliances are factory-equipped with
a flexible gas line connector and 1/2 inch
shutoff valve (see
Figure 47
on
Page 27
)
.
• See
Massachusetts Requirements
on
Page
4
for additional requirements for installations
in the state of Massachusetts in the USA.
• The gas supply line should Not be connected
to the appliance until
Step 7
(
Page 26
)
.
• A pipe joint compound rated for gas should be
used on the threaded joints.
Ensure propane
resistant compounds are used in propane
applications
. Be very careful that the pipe
compound does not get inside the pipe.
• It is recommended to install a sediment trap
in the supply line as close as possible to the
appliance.
• Check with local building official for local
code requirements.
IMPORTANT: If propane is used, be aware that
if tank size is too small (i.e. under 100 lbs, if
this is the only gas appliance in the dwelling.
Ref. NPFA 58), there may be loss of pressure,
resulting in insufficient fuel delivery (which
can result in sooting, severe delayed ignition
or other malfunctions). Any damage resulting
from an improper installation, such as this,
is not covered under the limited warranty.
C
Back wall of chase/enclosure (including any finishing materials)
7"
(178 mm)
MPD and MPDR units
D
E
F
A
B
MPD and MPDT units
b
a
Framing
Model
A
B
C
d
E
F
MPdT33
MPdR33
in.
33-1/8 48-1/2
34-5/16 17-3/16
24-1/4
5
mm
841
1232
872
437
616
127
MPd35
in.
35-1/8 57-1/2
40-5/8
19-3/16
28-3/4
6-1/8
mm
892
1461
1032
487
730
156
MPd40
in.
40-1/8 61-3/16 43-11/32 19-3/16 30-11/16
7-7/8
mm 1019
1554
1101
487
779
200
MPd45
in.
45-1/8 66-3/8 46-15/16 19-3/16 33-3/16
9-3/4
mm 1146
1686
1192
487
843
248