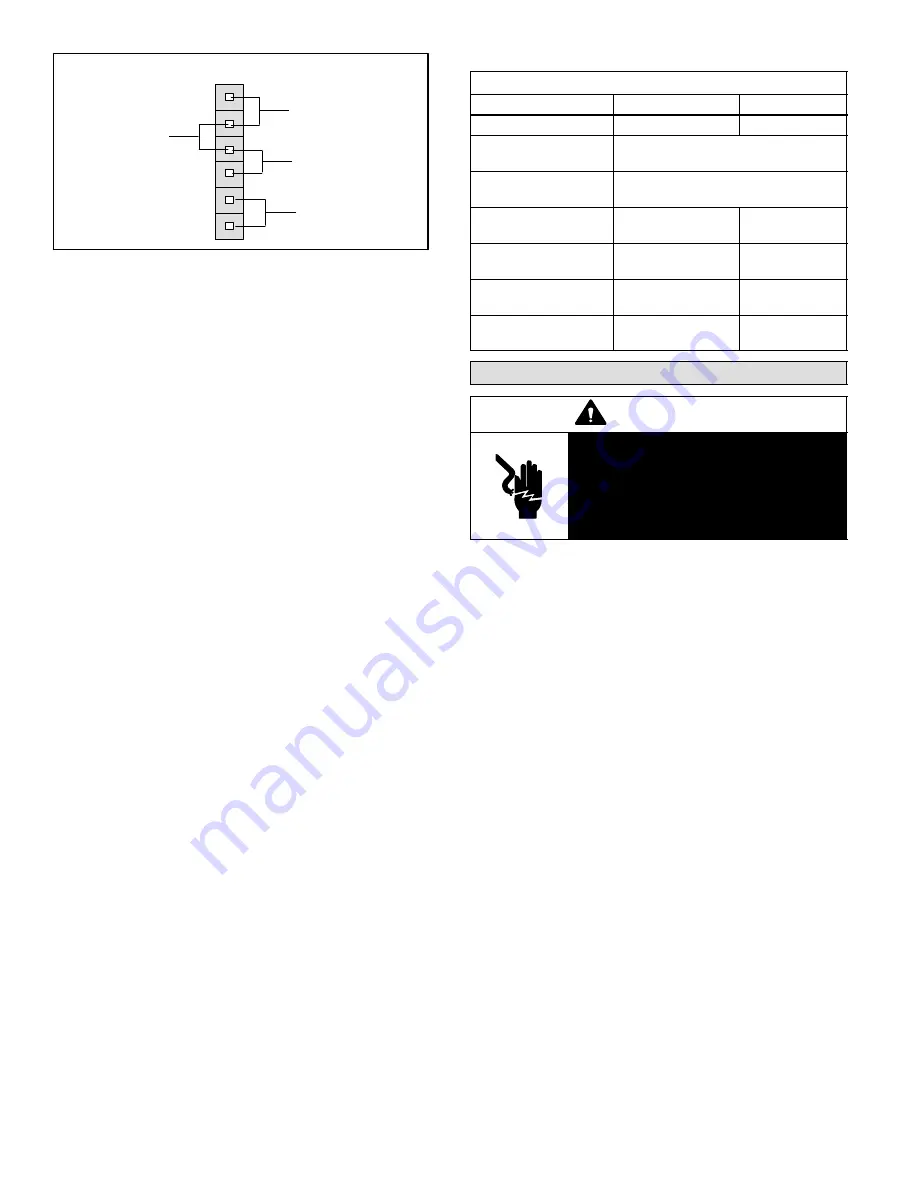
Page 18
505361M 09/07
P1
TEST
90
DEFAULT
30
60
Figure 29. P1 Jumper Configurations
A TEST option is provided for troubleshooting.
The TEST
mode may be started any time the unit is in the heating
mode and the defrost thermostat is closed or
jumpered.
If the jumper is in the TEST position at power-up, the
control will ignore the test pins.
When the jumper is placed across the TEST pins for
two seconds, the control will enter the defrost mode.
If the jumper is removed before an additional 5−second
period has elapsed (7 seconds total), the unit will
remain in defrost mode until the defrost thermostat
opens or 14 minutes have passed.
If the jumper is not removed until after the additional
5−second period has elapsed, the defrost will
terminate and the test option will not function again
until the jumper is removed and re−applied.
P5 Compressor 30−Second Delay
The DCB has a field−selectable function to reduce
occasional sounds that may occur while the unit is cycling
in and out of the defrost mode. The compressor will be
cycled off for 30 seconds going in and out of the defrost
mode when the compressor delay jumper is removed.
NOTE − The 30-second OFF cycle is not functional when
jumpering the TEST pins.
Time Delay ByPass
The timed-off delay is five minutes long. The delay helps to
protect the compressor from short-cycling in case the
power to the unit is interrupted or a pressure switch opens.
The delay is bypassed by placing the timer select jumper
across the P1 TEST pins for 0.5 seconds as illustrated in
figure 29.
DS1 and DS2 Diagnostic LEDs
The DCB uses two LEDs (DS1 and DS2) for diagnostics.
The LEDs flash a specific sequence according to the
condition.
Table 10.
DS1 and DS2 LED Codes
Defrost Control Board Diagnostic LED
Mode
Green LED (DS2)
Red LED (DS1)
No power to control
OFF
OFF
Normal operation /
power to control
Simultaneous Slow FLASH
Anti-short cycle lock-
out
Alternating Slow FLASH
Low pressure switch
fault (Optional)
OFF
Slow FLASH
Low pressure switch
lockout (Optional)
OFF
ON
High pressure switch
fault (Optional)
Slow FLASH
OFF
High pressure switch
lockout (Optional)
ON
OFF
Maintenance
WARNING
Electric shock hazard. Can cause
injury or death. Before attempting to
perform any service or maintenance,
turn the electrical power to unit OFF at
disconnect switch(es). Unit may have
multiple power supplies.
Before the start of each heating and cooling season, the
following service checks should be performed by a
qualified service technician. First, turn off electrical power
to the unit prior to performing unit maintenance.
Inspect and clean the outdoor and indoor coils. The
outdoor coil may be flushed with a water hose.
NOTE − It may be necessary to flush the outdoor coil more
frequently if it is exposed to substances which are
corrosive or which block airflow across the coil (e.g., pet
urine, cottonwood seeds, etc.)
Visually inspect the refrigerant lines and coils for leaks.
Check wiring for loose connections.
Check voltage at the indoor and outdoor units (with
units operating).
Check the amperage draw at the outdoor fan motor,
compressor, and indoor blower motor. Values should
be compared with those given on unit nameplate.
Check, clean (or replace) indoor unit filters.
Check the refrigerant charge and gauge the system
pressures.