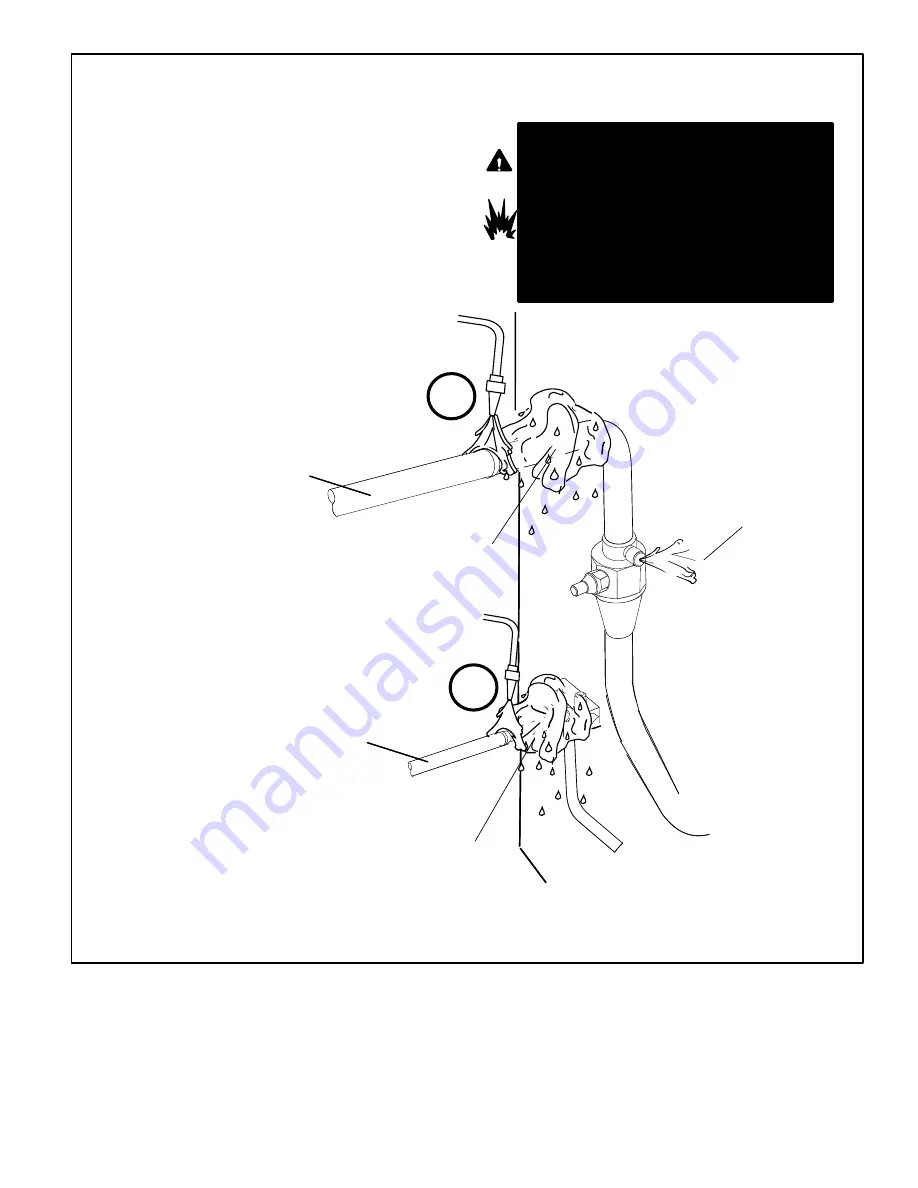
Page 69
XP17
BRAZE LINE SET
Water saturated cloths must remain water saturated
throughout the brazing and cool-down process.
6
After all connections have been brazed, disconnect manifold gauge set from service ports. Apply additional water saturated cloths to both
services valves to cool piping. Once piping is cool, remove all water saturated cloths. Refer to the unit installation instructions for the next step in
preparing the unit.
PREPARATION FOR NEXT STEP
7
WRAP SERVICE VALVES
To help protect service valve seals during brazing, wrap water saturated cloths around service valve bodies and copper tube stubs. Use
additional water saturated cloths underneath the valve body to protect the base paint.
4
FLOW NITROGEN
Flow regulated nitrogen (at 1 to 2 psig) through the refrigeration
gauge set into the valve stem port connection on the liquid service
valve and out of the suction / vapor valve stem port. See steps
3A,
3B
and
3C
on previous page and below for manifold gauge setup.
5
SUCTION / VAPOR LINE
WHEN BRAZING LINE SET TO
SERVICE VALVES, POINT FLAME
AWAY FROM SERVICE VALVE.
WARNING
1.
FIRE, PERSONAL INJURY, OR PROPERTY
DAMAGE
will result if you do not wrap a water
saturated cloth around both liquid and suction line
service valve bodies and copper tube stub while
brazing in the line set! The braze, when complete,
must be quenched with water to absorb any
residual heat.
2. Do not open service valves until refrigerant lines
and indoor coil have been leak-tested and
evacuated. Refer to procedures provided in this
supplement.
LIQUID LINE
WATER SATURATED
CLOTHS
WATER SATURATED CLOTHS
A
Braze liquid line to liquid line service valve.
B
Braze suction / vapor line to suction / vapor service
valve.
6A
6B
SUCTION / VAPOR SERVICE PORT
MUST BE OPEN AND SERVICE PORT
CORE REMOVED TO ALLOW EXIT
POINT FOR NITROGEN FLOW
IMPORTANT —
Allow braze joint to cool. Apply
additional water saturated cloths to help cool
brazed joints. Do not remove water saturated
cloths until piping has cooled. Temperatures
above 250ºF will damage valve seals.
Figure 42. Brazing Procedures (Continued)
Summary of Contents for iComfort SL18XC1 Series
Page 44: ...Page 44 XP17 Figure 21 Typical XP17 Wiring XP17 XX 230 06...
Page 45: ...Page 45 XP17 Factory Wiring Diagrams Figure 22 Typical Factory Wiring XP17 XX 230 01...
Page 46: ...Page 46 XP17 Figure 23 Typical Factory Wiring XP17 XX 230 02...
Page 47: ...Page 47 XP17 Figure 24 Typical Factory Wiring XP17 XX 230 03 and 05...
Page 48: ...Page 48 XP17 Figure 25 Typical Factory Wiring XP17 XX 230 06...