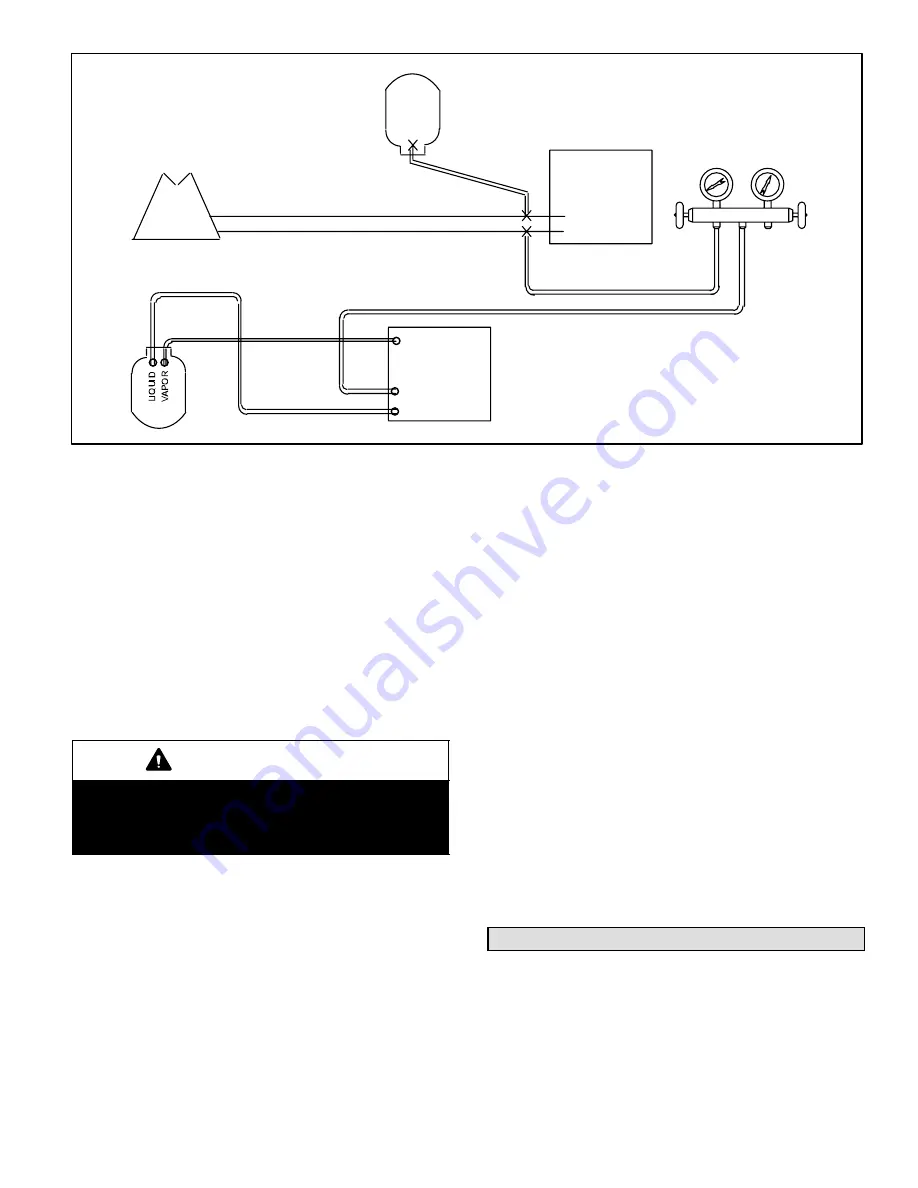
Page 9
HSXA16 SERIES
Flushing Connections
Low
Pressure
High
Pressure
Vapor Line
Service Valve
EXISTING
INDOOR COIL
HSXA16
UNIT
GAUGE MANIFOLD
Inverted HCFC−22 Cylin-
der
(Contains clean
HCFC−22 to be used for
flushing)
Liquid Line
Service Valve
Inlet
Discharge
Tank Return
Closed
Opened
EXISTING LIQUID LINE
RECOVERY CYLINDER
NOTE − The inverted HCFC−22 cyl-
inder must contain at least the
same amount of refrigerant as was
recovered from the existing sys-
tem.
Figure 10
EXISTING VAPOR LINE
RECOVERY MACHINE
2. Remove the existing outdoor unit. Set the new
HFC−410A unit and follow the brazing connection pro-
cedure which begins on the previous page to make line
set connections.
DO NOT install metering device at
this time.
Make low voltage and line voltage connections to the
new outdoor unit.
DO NOT turn on power to the unit
or open the outdoor unit service valves at this
time.
3. Remove the existing refrigerant flow control orifice or
thermostatic expansion valve before continuing with
flushing procedures. The existing devices are not ap-
proved for use with HFC−410A refrigerant and may
prevent proper flushing. Use a field−provided fitting to
reconnect the lines.
IMPORTANT
The line set and indoor coil must be flushed with
at least the same amount of clean refrigerant that
previously charged the system. Check the charge
in the flushing cylinder before proceeding.
4. Remove the pressure tap valve cores from the HSX-
A16 unit’s service valves. Connect an HCFC−22 cylin-
der with clean refrigerant to the vapor service valve.
Connect the HCFC−22 gauge set to the liquid line valve
and connect a recovery machine with an empty recov-
ery tank to the gauge set.
5. Set the recovery machine for liquid recovery and start
the recovery machine. Open the gauge set valves to
allow the recovery machine to pull a vacuum on the ex-
isting system line set and indoor coil.
6. Invert the cylinder of clean HCFC−22 and open its
valve to allow liquid refrigerant to flow into the system
through the vapor line valve. Allow the refrigerant to
pass from the cylinder and through the line set and the
indoor coil before it enters the recovery machine.
7. After all of the liquid refrigerant has been recovered,
switch the recovery machine to vapor recovery so that
all of the HCFC−22 vapor is recovered. Allow the re-
covery machine to pull a vacuum on the system.
NOTE − A single system flush should remove all of the
mineral oil from the existing refrigerant lines and in-
door coil. A second flushing may be done (using clean
refrigerant) if insufficient amounts of mineral oil were
removed during the first flush.
Each time the system
is flushed, you must allow the recovery machine
to pull a vacuum on the system at the end of the
procedure.
8. Close the valve on the inverted HCFC−22 drum and
the gauge set valves. Pump the remaining refrigerant
out of the recovery machine and turn the machine off.
9. Use dry nitrogen to break the vacuum on the refriger-
ant lines and indoor coil before removing the recovery
machine, gauges and HCFC−22 refrigerant drum. Re-
install pressure tap valve cores into HSXA16 service
valves.
10. Install the field−provided expansion valve (approved
for use with HFC−410A refrigerant) in the liquid line at
the indoor coil.
Manifold Gauge Set
Manifold gauge sets used with systems charged with
HFC−410A refrigerant must be capable of handling the
higher system operating pressures. The gauges should be
rated for use with pressures of 0 − 800 on the high side and
a low side of 30" vacuum to 250 psi with dampened speed
to 500 psi. Gauge hoses must be rated for use at up to 800
psi of pressure with a 4000 psi burst rating.