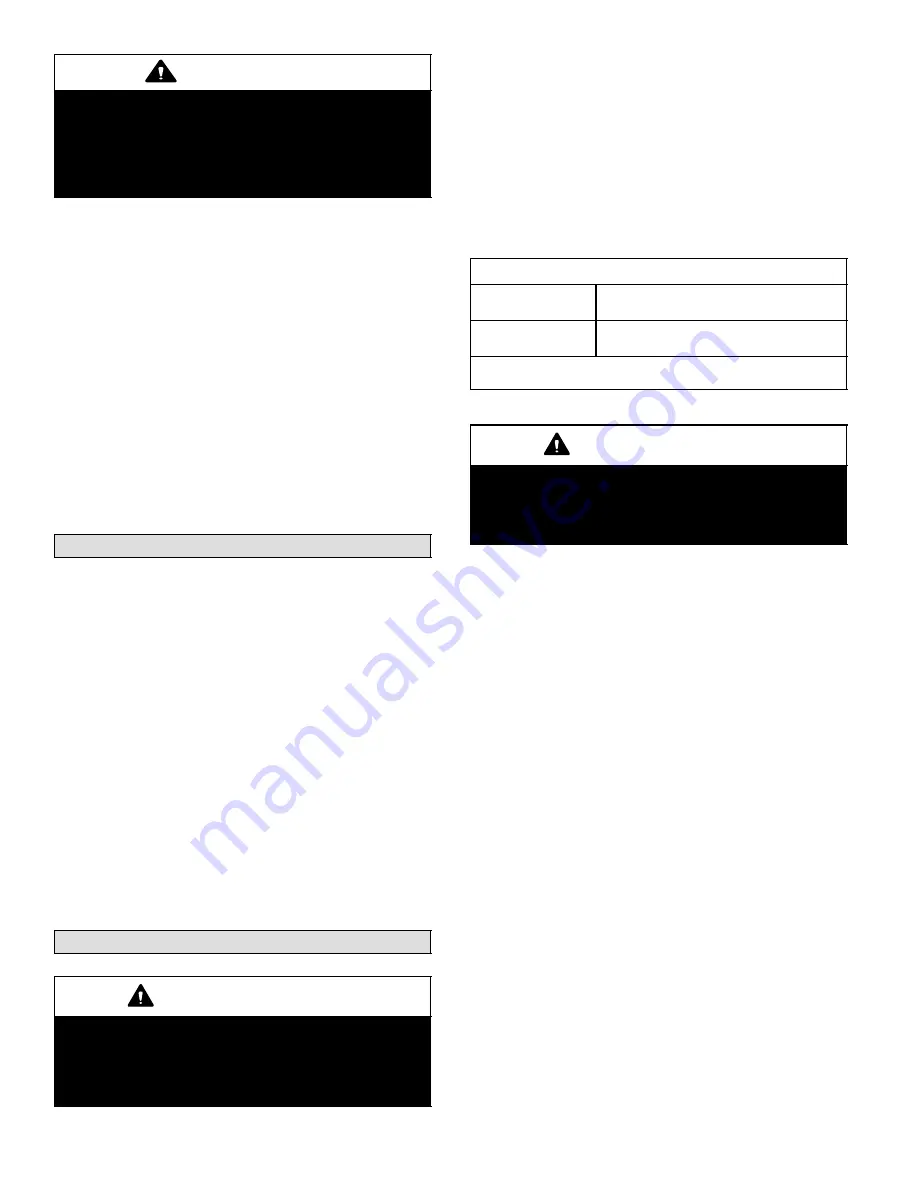
Page 12
504953M 03/06
WARNING
Danger of Equipment Damage. Avoid deep vacu-
um operation. Do not use compressors to evacu-
ate a system. Extremely low vacuums can cause
internal arcing and compressor failure. Damage
caused by deep vacuum operation will void war-
ranty.
8. Shut off the dry nitrogen cylinder and remove the man-
ifold gauge hose from the cylinder. Open the manifold
gauge valves to release the dry nitrogen from the line
set and indoor unit.
9. Reconnect the manifold gauge to the vacuum pump,
turn the pump on, and continue to evacuate the line set
and indoor unit until the absolute pressure does not
rise above 500 microns (29.9 inches of mercury) within
a 20−minute period after shutting off the vacuum pump
and closing the manifold gauge valves.
10. When the absolute pressure requirement above has
been met, disconnect the manifold hose from the vac-
uum pump and connect it to an upright cylinder of
HFC−410A refrigerant. Open the manifold gauge
valves to break the vacuum from 1 to 2 psig positive
pressure in the line set and indoor unit. Close manifold
gauge valves and shut off the HFC−410A cylinder and
remove the manifold gauge set.
Start−Up
1. Rotate fan to check for frozen bearings or binding.
2. Inspect all factory− and field−installed wiring for loose
connections.
3. After evacuation is complete, open the liquid line and
vapor line service valves to release the refrigerant
charge (contained in outdoor unit) into the system.
4. Replace the stem caps and secure finger tight, then
tighten an additional one-sixth (1/6) of a turn.
5. Check voltage supply at the disconnect switch. The
voltage must be within the range listed on the unit’s
nameplate. If not, do not start the equipment until you
have consulted the power company and the voltage
condition has been corrected.
6. Set the thermostat for a high stage cooling demand
(Y1 and Y2 demand). Turn on power to the indoor
blower and close the outdoor unit disconnect switch to
start the unit.
7. Recheck voltage while the unit is running. Power must
be within range shown on the nameplate.
Refrigerant Charging
IMPORTANT
Some HFC−410A cylinders are equipped with a dip
tube which allows you to draw liquid refrigerant
from the bottom of the cylinder without turning the
cylinder upside−down. The cylinder will be marked
if it is equipped with a dip tube.
This system is charged with HFC−410A refrigerant which
operates at much higher pressures than HCFC−22. This
unit is NOT approved for use with coils which include me-
tering orifices or capillary tubes.
Factory Charge
Units are factory charged with the amount of HFC−410A re-
frigerant indicated on the unit rating plate. This charge is
based on a matching indoor coil and outdoor coil with 15
feet (4.6 m) line set. For varying lengths of line set, refer to
table 3 for refrigerant charge adjustment.
Table 3
Refrigerant Charge per Line Set Lengths
Liquid Line
Set Diameter
Ounces per 5 feet (grams per 1.52 meter)
adjust from 15 ft. (4.57m) line set*
3/8 in. (9.5mm)
3 ounces per 5 feet (85 grams per 1.52 me-
ter)
*Add the amount shown if line length is greater than 15’ (4.57m), sub-
tract the amount shown if less than 15’.
Units Delivered Void of Charge
IMPORTANT
Mineral oils are not compatible with HFC−410A. If
oil must be added, it must be a polyol ester oil.
The compressor is charged with sufficient polyol
ester oil for approved line set lengths.
If the system is void of refrigerant,
clean the system us-
ing the following procedure:
1. Use dry nitrogen to pressurize the system and check
for leaks. Repair leaks, if possible.
2. Evacuate the system to remove as much of the mois-
ture as possible (triple evacuation).
3. Evacuate the system again. Then, weigh the appropri-
ate amount of HFC−410A refrigerant (listed on unit
nameplate) into the system.
4. Start the unit and monitor the system to determine the
amount of moisture remaining in the oil. Use test kit
10N46 to verify that the moisture content is within the
kit’s dry color range.
5. If the moisture content is not within the dry color range,
add a new filter drier between the liquid valve and the
TXV.
You may have to add a new filter drier several
times to achieve the required level of dryness.
If system dryness is not verified, the compressor
will fail in the future.
Checking Charge
The outdoor unit should be charged during warm weather.
However, applications arise in which charging must occur
in the colder months.
The method of charging is deter-
mined by the outdoor ambient temperature.
Measure the liquid line temperature and the outdoor ambi-
ent temperature as outlined below:
1. Connect the manifold gauge set to the service valves:
low pressure gauge to
vapor
valve service port
high pressure gauge to
liquid
valve service port
2. Connect the center manifold hose to an upright cylin-
der of HFC−410A. Close manifold gauge set valves.