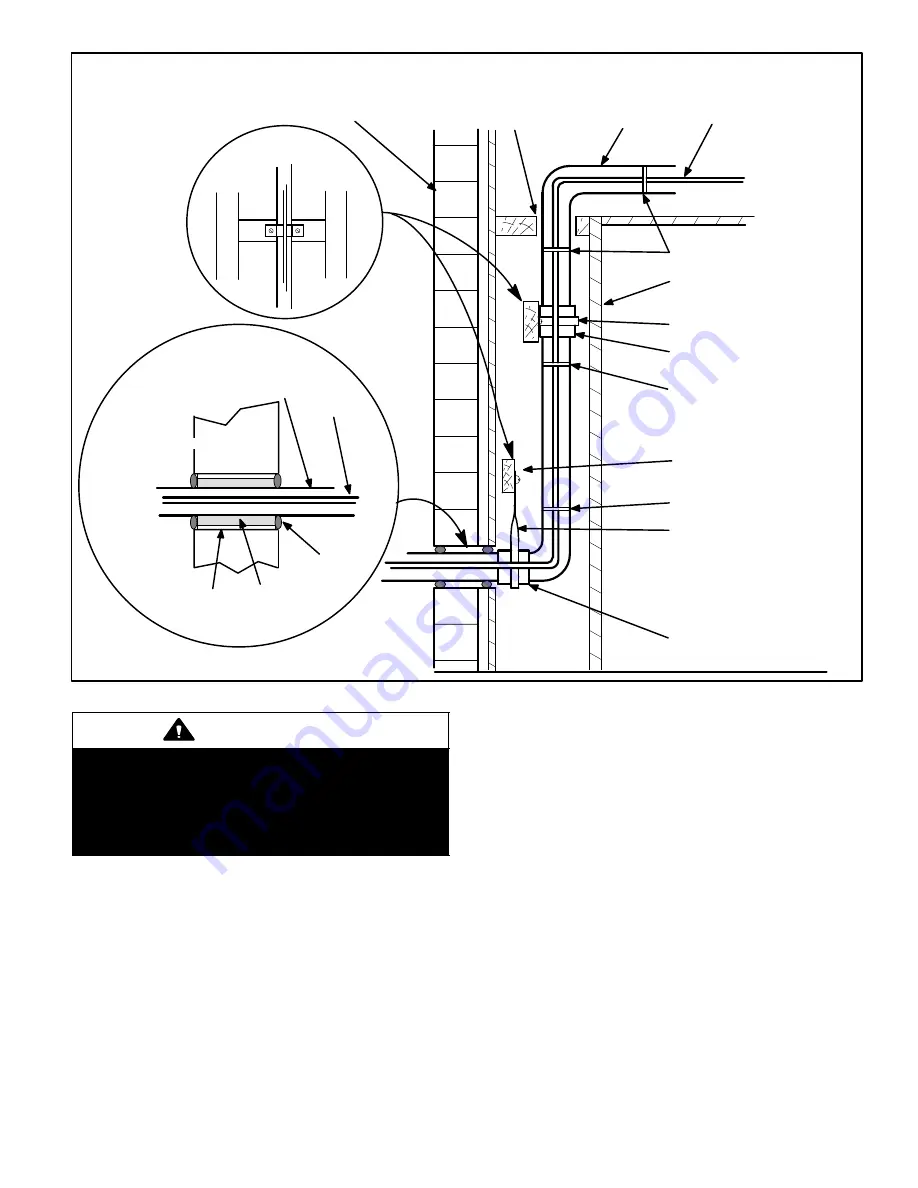
Page 7
HSXA16 SERIES
Refrigerant Line Sets: Installing Vertical Runs (new construction shown)
NOTE − Similar installation practices should be used if line set is to be installed on exterior of outside wall.
PVC PIPE
FIBERGLASS
INSULATION
CAULK
OUTSIDE WALL
VAPOR LINE WRAPPED
WITH ARMAFLEX LIQUID
LINE
IMPORTANT!
Refrigerant
lines must
not contact
structure.
OUTSIDE WALL
LIQUID LINE
VAPOR LINE
IMPORTANT - Refrigerant
lines must not contact wall.
WOOD BLOCK
BETWEEN STUDS
STRAP
SLEEVE
WOOD BLOCK
STRAP
SLEEVE
WIRE TIE
WIRE TIE
WIRE TIE
Figure 8
INSIDE WALL
WARNING
Polyol ester (POE) oils used with HFC−410A refrig-
erant absorb moisture very quickly. It is very im-
portant that the refrigerant system be kept closed
as much as possible. DO NOT remove line set caps
or service valve stub caps until you are ready to
make connections.
Brazing Connection Procedure
1. Cut ends of the refrigerant lines square (free from
nicks or dents). Debur the ends. The pipe must remain
round, do not pinch end of the line.
2. Before making line set connections, use dry nitrogen
to purge the refrigerant piping. This will help to prevent
oxidation and the introduction of moisture into the sys-
tem.
3. Use silver alloy brazing rods (5 or 6 percent
minimum
silver alloy for copper−to−copper brazing or 45 percent
silver alloy for copper−to−brass or copper−to−steel
brazing) which are rated for use with HFC−410A refrig-
erant. Wrap a wet cloth around the valve body and the
copper tube stub. Remove light maroon washers from
service valves and shield light maroon stickers in order
to protect them during brazing. Braze the line set to the
service valve.
4. Wrap a wet cloth around the valve body and copper
tube stub to protect it from heat damage during braz-
ing. Wrap another wet cloth underneath the valve body
to protect the base paint.
NOTE − The tube end must stay bottomed in the fitting
during final assembly to ensure proper seating, seal-
ing and rigidity.
5. Install the field−provided thermostatic expansion valve
(approved for use with HFC−410A refrigerant) in the
liquid line at the indoor coil.