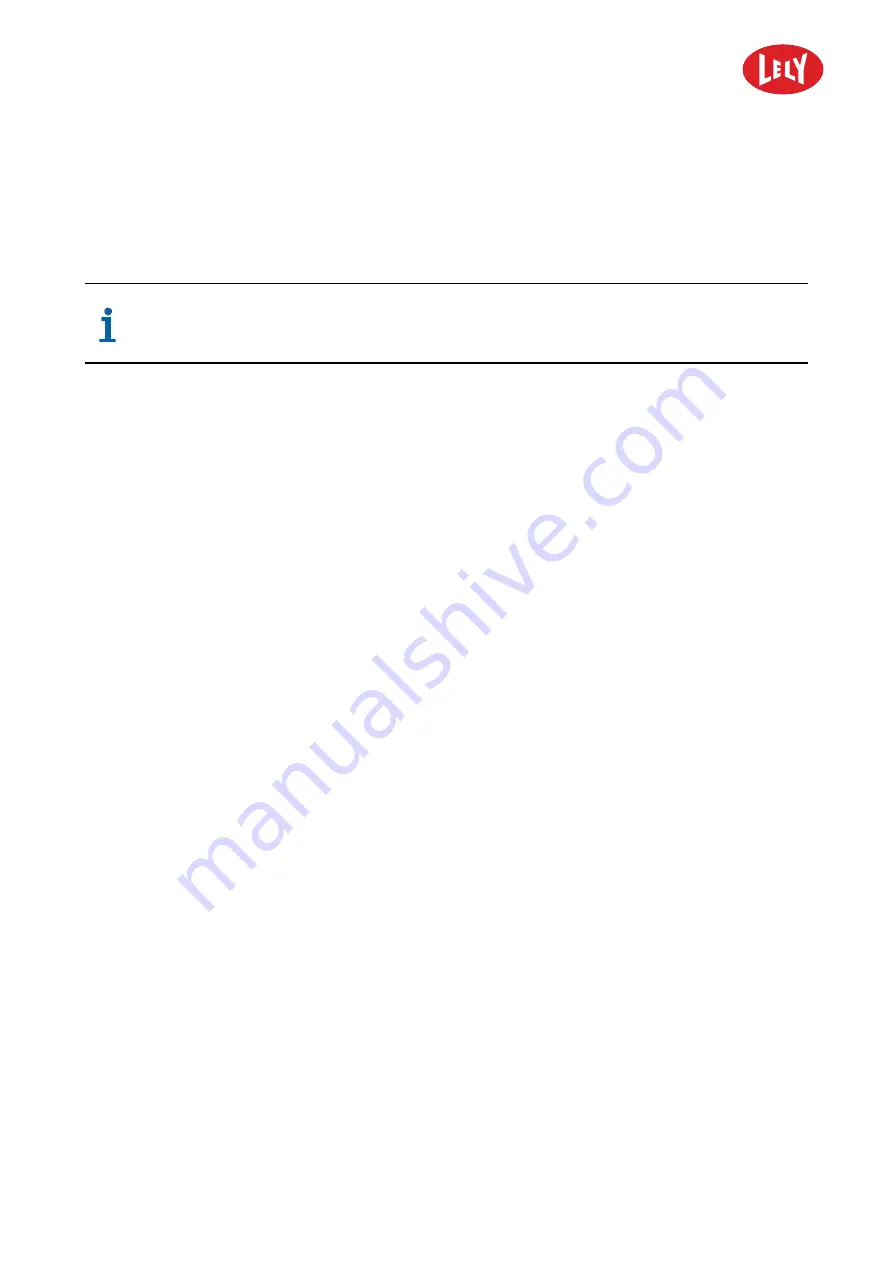
5.4002.8501.0
B
5-9
5.10
Prepare for Route Programming
5.10.1
Requirements for a good Route
Be aware of the intended use before programming the Discovery (See chapter Intended
Use).
Make it possible for the machine to correct itself
•
Include as many bump points as possible in all directions. If, due to slipping, the bump point is not
reached in time, the machine continues until the bump point is reached. This improves the reliability of
the route.
•
Be aware that actions like
Turn
and
Straight
may cause inaccurate results. Make sure the vehicle
cannot get stuck after making a turn or driving straight. Program a 'long action' (wall contact:
Wall follow
or
Ultrasound
) after a 'short action' (no wall contact:
Turn
or
Straight
•
If the vehicle follows the wall or cubicle row (
Wall follow
or
Ultrasound
) and if there is a bend, stop
the vehicle, program a turn and go on to follow the wall (see To follow a Bend in a Wall on page 5-19).
Make it easy for yourself
•
Program routes from different positions in the barn back to the charging station. This will enable you
to easily return the vehicle back to the charging station in case it gets lost.
•
Make a backup after programming a route.
Adapt the route or settings to the herd
•
The beep can be modified separate for each route. If the beep length is set to 0, the beep is switched
Off
. If a warning signal is given, the cows have time to move out of the way. However, the sound may
equally well disturb other cows (see which settings suit your herd best).
•
Set the speed to a lower level for parts of the route or the whole route if the cows are disturbed (see
Set the Speed for a Particular Action on page 5-35).
5.10.2
Example Routes, Barn with Milking Robot
In the example situation, the barn is divided into 3 areas. The time path has different routes to clean each
area:
Route 1
The area behind the cubicles is most extensively polluted (see figure 24 on page 5-10). It should be
cleaned each hour at least.
Route 2
The walking alley should be cleaned 4 to 6 times a day (see figure 25 on page 5-11). Because the area
behind the cubicles should be cleaned often, the route combines cleaning the walking area and the area
behind the cubicles. It is useful to clean the walking area just before you enter the stall, for instance at
7:00, 12:00, 17:00 and 22:00 hour.
in n o vato rs in ag ric u ltu re
Summary of Contents for DISCOVERY 90 S
Page 2: ...INTENTIONALLY BLANK 5 4002 8501 0 B innovators in agriculture...
Page 6: ...INTENTIONALLY BLANK 5 4002 8501 0 B 6 List of Included Amendments innovators in agriculture...
Page 16: ...INTENTIONALLY BLANK 5 4002 8501 0 B 1 2 Lely Discovery innovators in agriculture...
Page 56: ...INTENTIONALLY BLANK 5 4002 8501 0 B 4 32 Description and Operation innovators in agriculture...
Page 104: ...INTENTIONALLY BLANK 5 4002 8501 0 B 6 12 Maintenance innovators in agriculture...
Page 112: ...INTENTIONALLY BLANK 5 4002 8501 0 B 7 8 Test and Adjustment innovators in agriculture...
Page 134: ...INTENTIONALLY BLANK 5 4002 8501 0 B 9 2 Disposal innovators in agriculture...
Page 137: ......