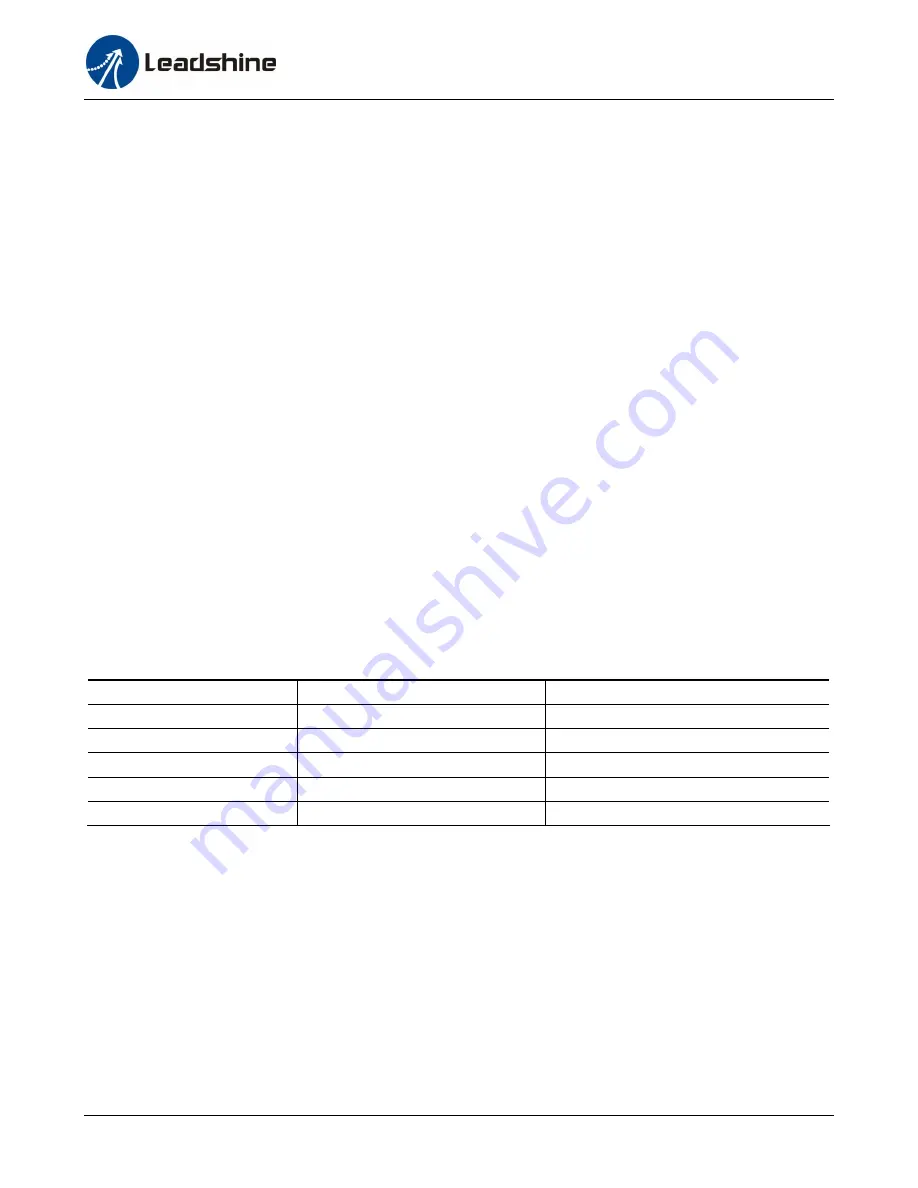
Hardware
manual of the ES-DH series drives
10
Wiring Notes
l
In order to improve anti-interference performance of the drive, it is recommended to use twisted
pair shield cable.
l
To prevent noise incurred in PUL/DIR signal, pulse/direction signal wires and motor wires should
not be tied up together. It is better to separate them by at least 10 cm, otherwise the disturbing
signals generated by motor will easily disturb pulse direction signals, causing motor position
error, system instability and other failures.
l
If a power supply serves several drives, separately connecting the drives is recommended instead
of daisy-chaining.
l
It is prohibited to pull and plug power connector while the drive is powered ON, because there is
high current flowing through motor coils (even when motor is at standstill). Pulling or plugging
power connector with power on will cause extremely high back-EMF voltage surge, which may
damage the drive.
Configuration
When the default settings of the easy servo drives are not suitable for your application, it is necessary
to configure it via the on board HMI or the configuration software ProTuner. Otherwise you may
encounter problems like high motor heating, big motor noise or even motor stall due to weak torque.
For a quick start of the easy servo drive, there are not much parameters need to be configured. The
following table gives the most significant settings of the easy servo drives.
Most significant settings of the easy servo drive
Parameters
ES-DH1208
ES-DH2306
Pulses/Revolution
Default 4000, Software Adjustable
Default 4000, Software Adjustable
Holding Current (%)
Default 40%, Software Adjustable
Default 40%, Software Adjustable
Close-loop Current Limit (%)
Default 60% , Software Adjustable
Default 60% , Software Adjustable
Current Loop Kp
*Auto Tuning at Power-up
*Auto Tuning at Power-up
Current Loop Ki
*Auto Tuning at Power-up
*Auto Tuning at Power-up
*
Auto Tuning at Power-up
: It is possible to disable this feature in the setup software in order to tune
the current loop Kp and current loop Ki manually if the auto tuning result is not good enough. This
happens when the motor
’
s inductance or resistance is too high or too low.