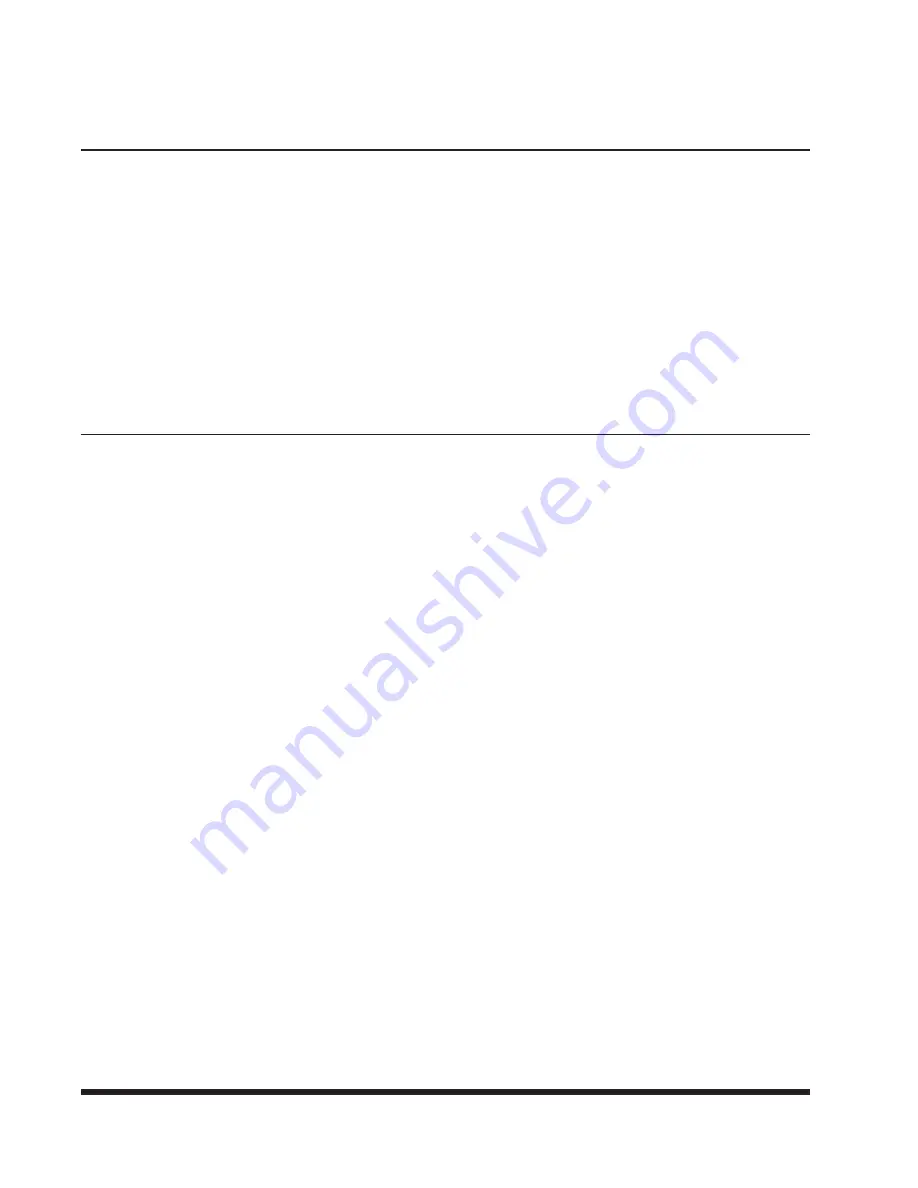
4-8
4-5
WHEEL BEARING MAINTENANCE
Wheel bearing maintenance should be per-
formed at the beginning of every season of use.
Check the wheel bearings periodically for exces-
sive end play. If needed, adjust or replace them
using the following procedure:
4-5.1
Place the frame on blocks or stands suf-
ficient to lift the tire clear of the ground.
4-5.2
Remove the hub cap, cotter pin, slotted
nut and washer.
4-5.3
Remove the hub. Clean and inspect the
bearings and hub cavity. Replace any worn
or defective parts.
4-5.4
Repack the bearings using a high-
quality wheel bearing grease.
4-5.5
Replace the hub with a new seal and
the inner bearing in place.
4-5.6
Install the outer bearing cone, washer
and slotted nut.
4-5.7
Tighten the slotted nut while rotating the
hub until there is a slight resistance to wheel
rotation. Then, back the slotted nut off one
notch, until the wheel rotates freely without
end play.
4-5.8
Install a new cotter pin and replace the
hub cap.
4-6
HYDRAULIC MAINTENANCE
4-6.1
Check the tractor hydraulic fluid level
per tractor owners manual and after any
leakage. Check fluid level with the cylinders
in the retracted position.
4-6.2
If a cylinder or valve leaks, disassemble
the parts to determine the cause of the leak.
Any time a cylinder is opened up, or when-
ever any seal replacement is necessary, it is
advisable to clean all parts and replace all
seals. Seal kits are available from your Lan-
doll dealer.
4-6.3
Check all hydraulic hoses weekly. Look
for binding or cracking. Replace all worn or
defective parts immediately.
Summary of Contents for 850 FINISHOLL Series
Page 4: ......
Page 8: ......
Page 12: ...2 4 Figure 2 1 11 Shank Placement Assembly...
Page 13: ...2 5 Figure 2 2 14 Shank Placement Assembly...
Page 14: ...2 6 Figure 2 3 16 8 Shank Placement Assembly...
Page 15: ...2 7 Figure 2 4 16 8 Shank Placement Assembly...
Page 16: ...2 8 Figure 2 5 19 4 Shank Placement Assembly...
Page 17: ...2 9 Figure 2 6 19 4 Shank Placement Assembly...
Page 18: ...2 10 Figure 2 7 22 Shank Placement Assembly...
Page 19: ...2 11 Figure 2 8 22 Shank Placement Assembly...
Page 20: ...2 12 Figure 2 9 24 8 Shank Placement Assembly...
Page 21: ...2 13 Figure 2 10 24 8 Shank Placement Assembly...
Page 22: ...2 14 Figure 2 11 27 4 Shank Placement Assembly...
Page 23: ...2 15 Figure 2 12 27 4 Shank Placement Assembly...
Page 24: ...2 16 Figure 2 13 30 Shank Placement Assembly...
Page 25: ...2 17 Figure 2 14 30 Shank Placement Assembly...
Page 26: ...2 18 Figure 2 15 33 N Shank Placement Assembly...
Page 27: ...2 19 Figure 2 16 33 N Shank Placement Assembly...
Page 28: ...2 20 Figure 2 17 33 Shank Placement Assembly...
Page 29: ...2 21 Figure 2 18 33 Shank Placement Assembly...
Page 30: ...2 22 Figure 2 19 35 Shank Placement Assembly...
Page 31: ...2 23 Figure 2 20 35 Shank Placement Assembly...
Page 32: ...2 24 A A 850 41 p1 Figure 2 21 41 Shank Placement Assembly Left Outer Wing...
Page 35: ...2 27 C C 850 41 p4 Figure 2 24 41 Shank Placement Assembly Right Outer Wing...
Page 36: ......
Page 38: ...3 2 Figure 3 1 Frame Assembly 30 to 41...
Page 43: ...3 7 Figure 3 5 Wing and Wing Extensions 17 35 Models...
Page 58: ...3 22 Figure 3 18 Installation of Shanks and Clamps...
Page 62: ...3 26 Figure 3 21 Disc Gang Assembly 850 Series Figure 3 22 Adjustment Cylinder Installation...
Page 63: ...3 27 Figure 3 23 Disc Gang Hydraulic Assembly...
Page 68: ...3 32 Figure 3 26 Leveling Assembly Installation...
Page 70: ...3 34 Figure 3 27 Hydraulic Radius Rod...
Page 72: ...3 36 Figure 3 28 Warning Light Installation...
Page 74: ...3 38 Figure 3 29 Rear Hitch Assembly Option...
Page 76: ...NOTES 3 40...
Page 82: ...4 6 Figure 4 5 Coil Tine Harrow Figure 4 6 Spike Harrow 3 and 5 Bar...
Page 83: ...4 7 Figure 4 7 Spike Harrow Tilloll Style Figure 4 8 Chain Spike Harrow...
Page 87: ...4 11 NOTES...
Page 88: ......
Page 91: ...NOTES 5 3...
Page 92: ......