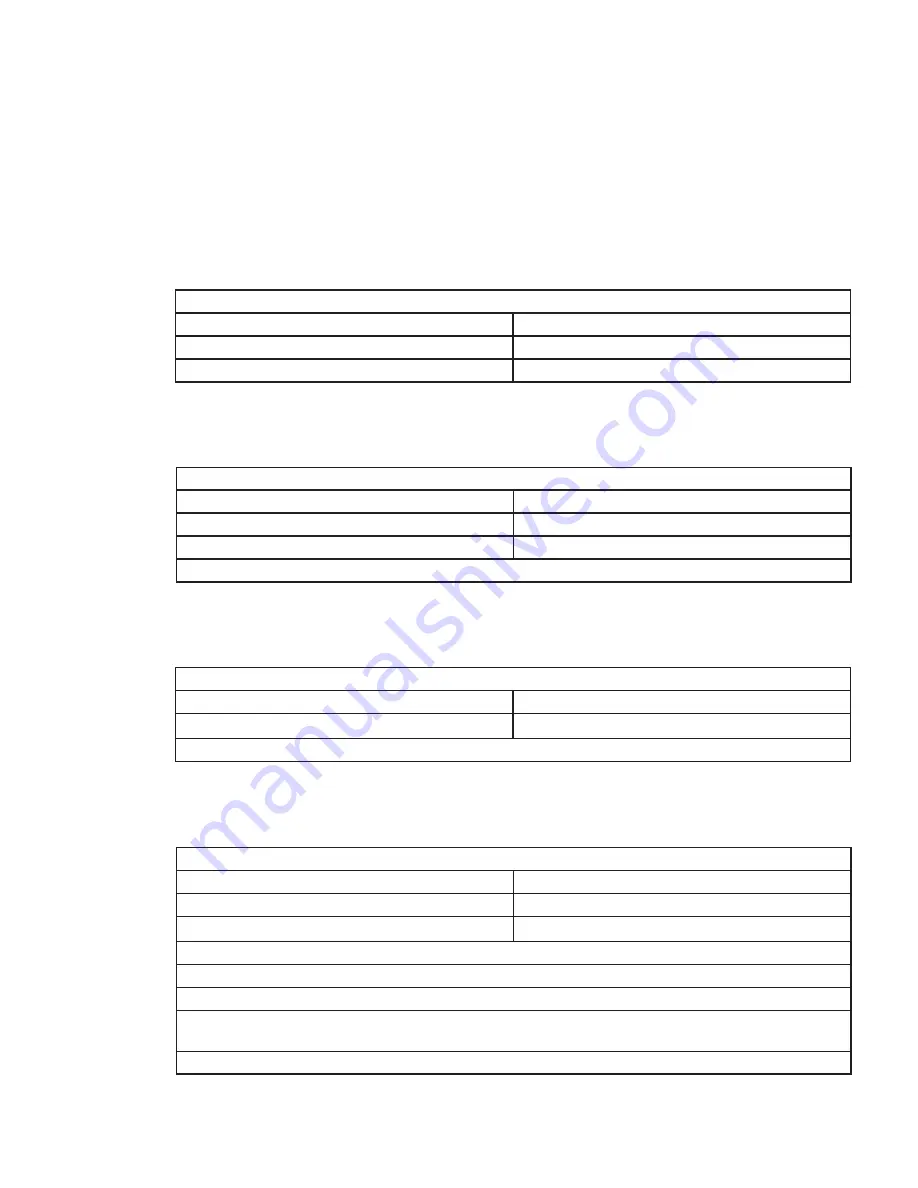
PRE-INSTALLATION CHECKLIST
BEFORE GETTING STARTED
Each unit is tested under operating conditions and is thoroughly inspected before
shipment. At the time of shipment, the carrier accepts responsibility for the unit. Upon
receiving the unit, carefully inspect the carton for visible damage. If damage exists, have
the carrier note the damage on the freight bill and file a claim with carrier. Responsibility for
damage to the dispenser lies with the carrier.
TOOLS REQUIRED
Oetiker Pliers
Slotted Screwdriver
Tubing Cutters
Phillips Screwdriver
Wrench
Cordless Drill
POST MIX ACCESSORIES
CO2 Regulator Set
CO2 Supply
Beverage Tubing
Oetiker Clamps/Fittings
Water Booster
Water Regulator
Precision Cutters (if removing/replacing carbonator tank)
CONSIDER LOCATION OF THE FOLLOWING PRIOR TO INSTALL
Water supply lines
Drain
Is the countertop level?
Heating and air conditioning ducts
Grounded electrical outlet.
Enough space to install the dispenser. Include space for a top-mounted ice machine, if necessary.
Does the top-mounted ice machine have a minimum clearance on all sides?
Located away from direct sunlight or overhead lighting.
Can the countertop support the weight of the dispenser? Be sure to include the weight of an ice
machine (if necessary) plus the weight of the ice.
This unit is not suitable for use in an area where a water jet could be used.
BIB SYSTEM
BIB Rack
BIB Regulator Set
BIB Syrup Boxes
BIB Connectors - ensure you have the correct connectors for syrup lineup.
5