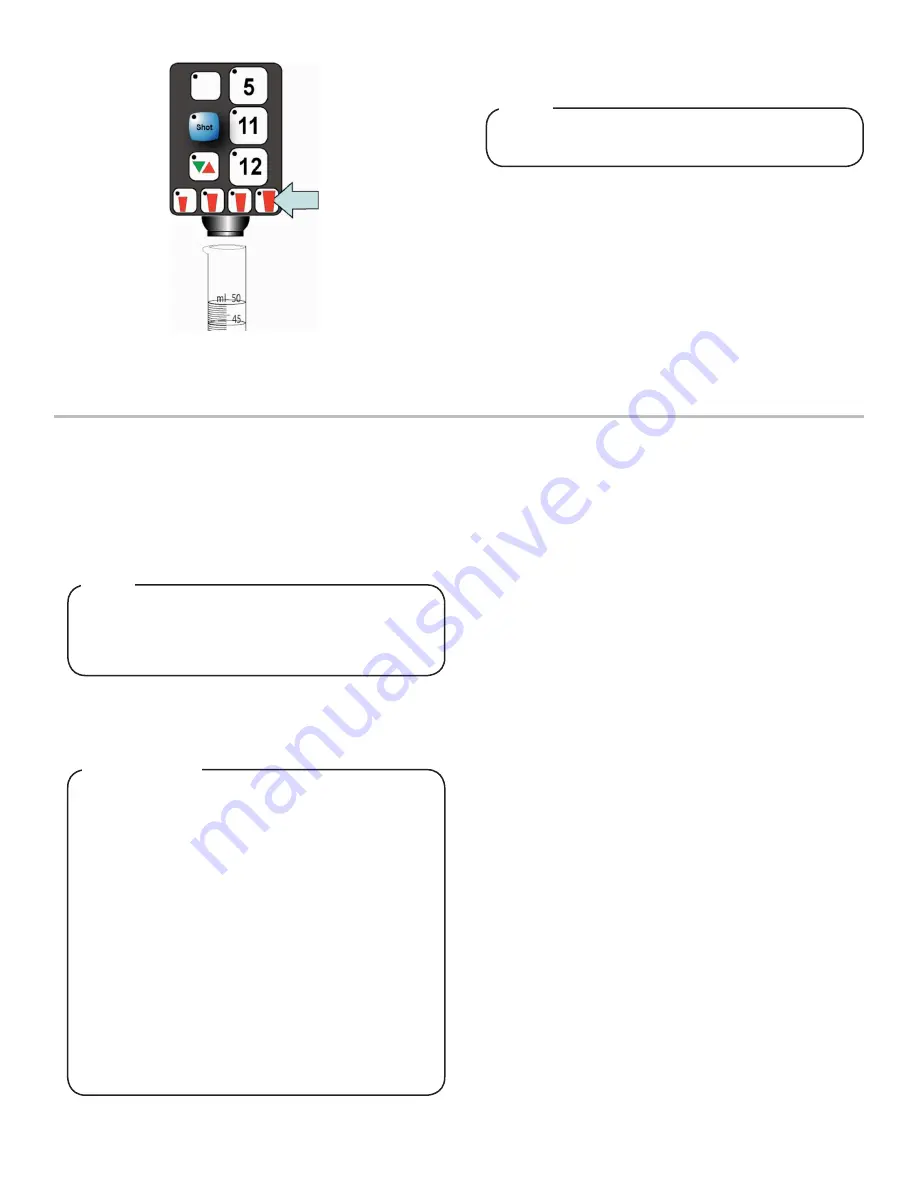
11
The cleaning procedures provided herein pertain to the
Lancer equipment identified by this manual. If other
equipment is being cleaned, follow the guidelines
established by the manufacturer for that equipment.
NOTE
CLEANING AND SANITIZING
General Information
•
Lancer equipment (new or reconditioned) is shipped from
the factory cleaned and sanitized in accordance with NSF
guidelines. The operator of the equipment must provide
continuous maintenance as required by this manual and/
or state and local health department guidelines to ensure
proper operation and sanitation requirements are
maintained.
•
Cleaning should be accomplished only by trained personnel.
Sanitary gloves are to be used during cleaning operations.
Applicable safety precautions must be observed. Instruction
warnings on the product being used must be followed.
• Use sanitary gloves when cleaning the unit and
observe all applicable safety precautions.
• DO NOT
use a water jet to clean or sanitize the
unit.
• DO NOT
disconnect water lines when cleaning
and sanitizing syrup lines, to avoid contamination.
• DO NOT
use strong bleaches or detergents; These
can discolor and corrode various materials.
• DO NOT
use metal scrapers, sharp objects, steel
wool, scouring pads, abrasives, or solvents on the
dispenser.
• DO NOT
use hot water above 140° F (60° C). This
can damage the dispenser.
• DO NOT
spill sanitizing solution on any circuit
boards. Insure all sanitizing solution is removed
from the system.
!
ATTENTION
The Flavor Shot programming will automatically save
60 seconds after all changes have been made.
NOTE
5. Repeat Steps 2-4 for each of the desired brands.
6. Press the Pour/Cancel button to save.
Cleaning Solution
Mix a mild, non-abrasive detergent (e.g. Sodium Laureth
Sulfate, dish soap) with clean, potable water at a temperature
of 90°F to 110°F (32°C to 43°C). The mixture ratio is one
ounce of cleaner to two gallons of water. Prepare a minimum of
five gallons of cleaning solution. Do not use abrasive cleaners or
solvents because they can cause permanent damage to the unit.
Ensure rinsing is thorough, using clean, potable water at a
temperature of 90°F to 110°F (32°C to 43°C). Extended lengths
of product lines may require additional cleaning solution.
Sanitizing Solution
Prepare sanitizing solutions in accordance with the
manufacturer’s written recommendations and safety guidelines.
The solution must provide 200 parts per million (PPM) chlorine
(e.g. Sodium Hypochlorite or bleach). A minimum of five gallons
of sanitizing solution should be prepared. Any sanitizing solution
may be used as long as it is prepared in accordance with the
manufacturer’s written recommendations and safety guidelines,
and provides 200 parts per million (PPM) chlorine.
Other Supplies Needed
Daily Cleaning
1. Using the cleaning solution, clean top cover and all exterior
stainless steel surfaces.
2. Clean exterior of dispensing valves and ice chute.
3. Remove cup rest then clean the drip tray and cup rest.
Replace cup rest and drip tray when finished.
4. Wipe clean all splash areas using a damp cloth soaked in
cleaning solution.
5. Clean beverage valves as specified by the valve
manufacturer.
1. Clean cloth towels
2. Bucket
3. Extra nozzle
4. Sanitary gloves
5. Small brush (PN 22-0017)
Summary of Contents for Bevariety ACIB Series
Page 14: ...14 WIRING DIAGRAMS ACIB 22 30...