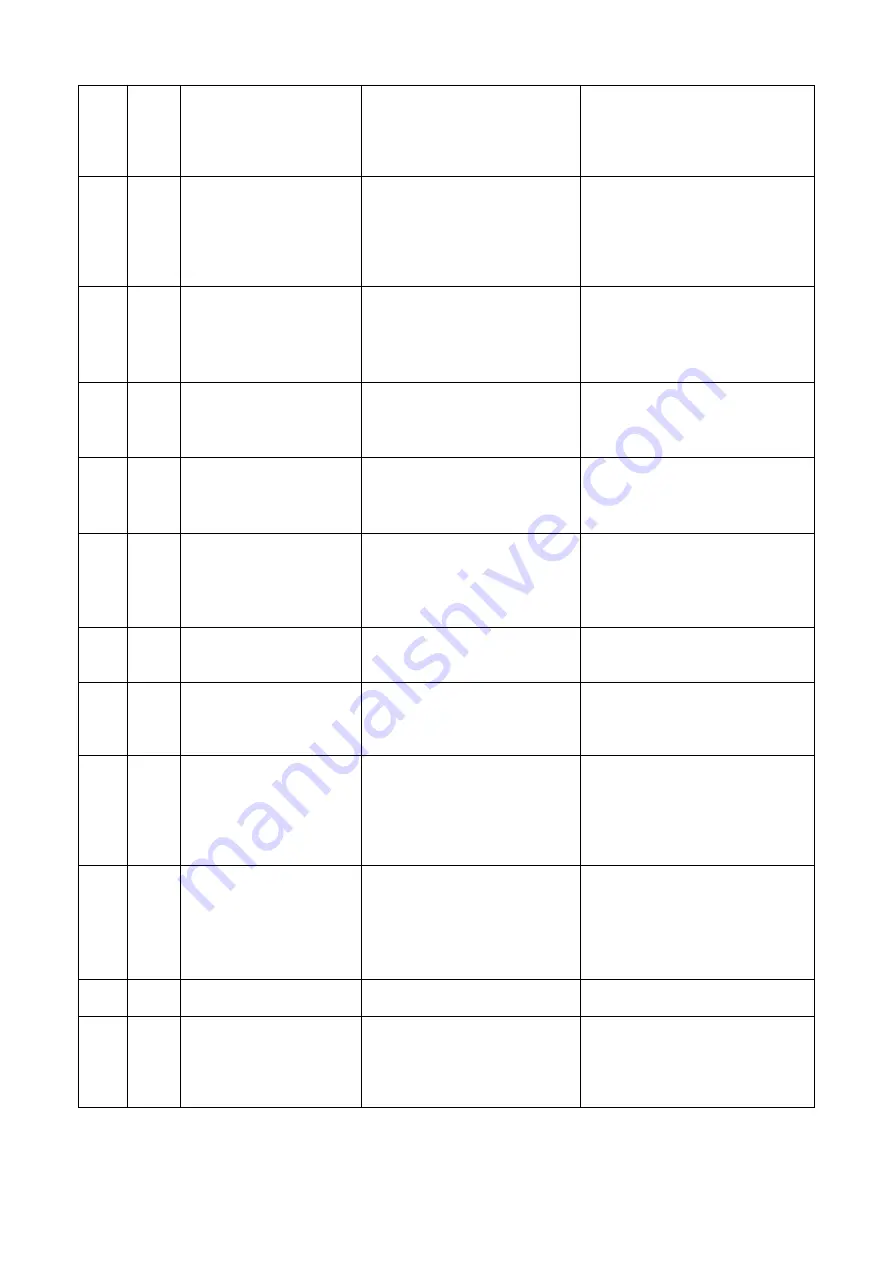
No.:GC-JS-21 Version: 01/00
Effective date
:
2020-07-22
30
8
E62
220
≥
heating jacket
temperature> 190
℃
1. The connector of the
temperature sensor of the
heating ring is not in good
contact
2. The circuit board is damaged
Re-made the connector of the
temperature sensor of the heating
jacket
Replace the circuit board
9
E63
230
≥
heating jacket
temperature> 160
℃
1. The connector of the
temperature sensor of the
heating jacket is not in good
contact,
2. The circuit board is damaged
3. The pump is damaged
Re-made the connector of the
temperature sensor of the heating
jacket
Replace the circuit board
Replace the water pump
10
E2
Overpressure in
sterilization chamber:
134
℃
pressure exceeds
235kpa, 121
℃
program
pressure exceeds 135kpa
No vacuum can be drawn, and
more cold air remains
Test vacuum pump, vacuum
selection valve
11
E41
After 8 minutes in the
preheating phase, the
temperature of the
heating jacket <100
℃
heating jacket failed
Check the thermostat of heating
jacket and the related thermostat
12
E42
The steam generator
temperature <110
℃
after 8 minutes in the
preheating stage
Heating bar in steam generator
failed
Check the thermostat of heating
bar and the related thermostat
13
E5
After 10 minutes of
sterilization phase, the
exhaust failed to reach
20kpa
Drain piping blocked
Clean and sterilize indoor filters
Check the drain solenoid valve,
vacuum selection valve
14
E6
The door switch is
disconnected when the
program is running
The door switch sensor is
displaced, the micro switch
cannot be closed
Reassemble the door switch
15
E7
Local atmospheric
pressure is less than
<70KPa;
1. The stored pressure value is
wrong,
2. The ambient air pressure is
too low
Corrected atmospheric pressure
Check if ground elevation is
detected above 2500 meters
16
E8
During the rising process,
the pressure is added less
than 3kpa in 1 minute
1. unable to inject water;
2. The heating bar of the steam
generator is damaged
3. The door seal is damaged
Observe whether the water
storage tank has enough water and
check the water level sensor;
Check the pump and inlet
solenoid valve;
Check the door seal
17
E9
Low pressure during
sterilization: 134
℃
pressure is lower than
100kpa, 121
℃
program
pressure is lower than
200kpa
1. too much loading loaded;
2. unable to enter the water
1. Reduce the number of loads;
2. Observe whether the water
storage tank has enough water and
check the level switch;
3. Check the water pump and inlet
solenoid valve
18
E10
Door can not be locked at
the beginning of cycle
Door lock failure
Check electromagnet and circuit
board
19
E11
The door lock cannot be
opened at the end of the
program
Door lock is open during
operation
1.
The electronic lock is stuck
and damaged
2. The circuit board is
damaged
Check the electronic lock and
circuit board