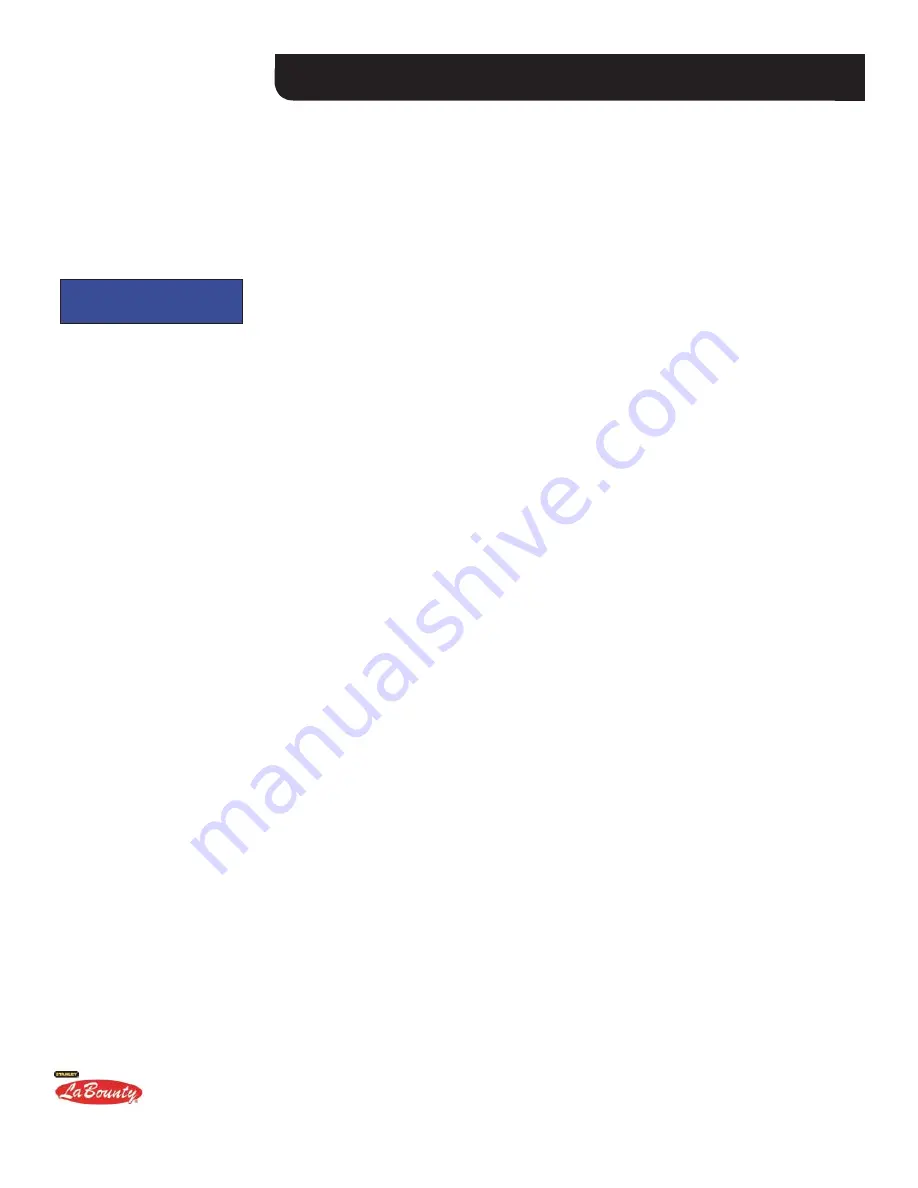
MSD 7R SHEARS
Maintenance
Section 5 Page 17
GENERAL BUILD-UP AND HARDSURFACING
It is recommended that the upper piercing tip and lower piercing tip seat be maintained every 80 hours,
while correct hardsurfacing of the upper and lower shear need only be done periodically. If the shear is in a
severe piercing application, the interval for piercing tip maintenance may need to be shortened. Excessive
hardsurfacing can damage the shear and affect the shears performance. Allow the hardsurfacing to wear
down or away before hardsurfacing again. Never apply more than two layers of hardsurfacing. The quality and
attention to detail in welding can signifi cantly affect the life of the shear. LaBounty strongly recommends that
only certifi ed welders be used.
Strict adherence to the welding rod manufacture’s handling and storage instructions is essential. Electrodes
exposed to the atmosphere for more than four hours must not be used—the moisture absorbed by the elec-
trode covering will change the mechanical properties of the weld, which can cause cracks and porosity in the
weld or adjacent base metal.
LaBounty recommends that you use AWS E7018 rod or equivalent for build-up. After vigorously peening each
pass, the hardsurfacing is placed directly on top of the E7018 beads. The E7018 becomes the bonding or
underlayment for the hardsurfacing. This will help reduce the chances of having the hardsurfacing material
crack.
LaBounty recommends using Amalloy 814 rod or equivalent for hardsurfacing. Do not use stainless hardsur-
face rod; for LaBounty applications it is too brittle and cracks, weakening the base metal.
All blade maintenance must be done before upper piercing tip build-up and hardsurfacing. Upper piercing tip
must be done before lower piercing tip seat. Complete piercing tip maintenance before any upper and lower
shear build-up and hardsurfacing.
GENERAL PROCEDURE
1.
Clean all dirt and grease from the area to be built-up.
2.
Remove the worn hardsurfacing by grinding to the base metal. Do not build-up on top of any hardsurface
material.
3.
Pre-heat the surrounding area to at least 200ºF (100ºC) to remove moisture. Preheat the area to be built
up to 300-400ºF (150-200ºC). Use a temp stick to verify that this temperature is obtained and maintained
throughout the welding process. Temperatures in excess of 450ºF (230ºC) may harm parent metal.
4.
Build up and restore any worn or damaged surfaces with E7018 (or equivalent). Each pass must be stress
relieved by peening vigorously. Grind edges to 90º.
5.
Hardsurface as instructed in this manual. It is not necessary to cover the entire surface with hardsurfacing
to be effective. Vigorously peen the hardsurfacing to stress-relieve and work-harden the material.
6.
Post heat to 300-400ºF (150-200ºC); cover with heat blanket and allow to cool.
It is recommended that build-up and hardsurfacing be performed at the end of the work day to allow adequate
time to cool.
NOTICE