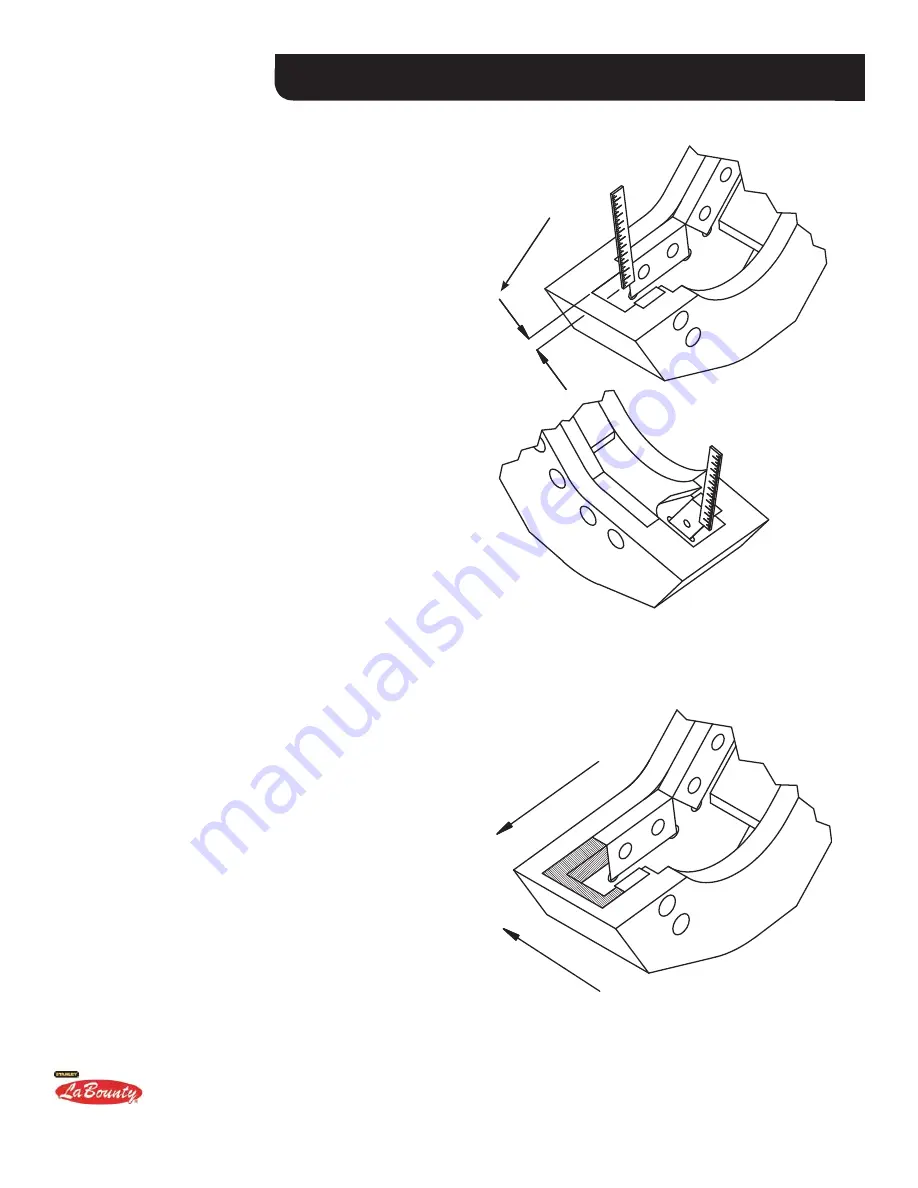
MSD 7R SHEARS
Maintenance
Section 5 Page 21
LOWER PIERCING AREA
BUILD-UP AND
HARDSURFACING
continued
IMPORTANT
Check temperature during this procedure. (Main-
tain 300-400°F/ 150-200°C.)
6.
To hardsurface the build-up just completed, we
recommend using Amalloy 814 or equivalent. Apply
single passes side by side with the grain. Start ap-
proximately 2 - 3" (50 - 75 mm) down the inside of the
piercing tip seat, running the length of the shear and
across the inside of the nose plate (see fi gure 4-12).
Peen each pass. No more than two layers of this rod
should be used.
IMPORTANT
It is important to use an air operated slag peener
on each pass of weld to relieve stress. Grind off
in line with cutting edges.
7.
Hardsurface the top side of lower 1½ - 2" (38 - 50
mm) wide (fi gure 5-12) using the same preheating,
welding and peening procedure. Be sure to weld
with the grain of the steel (see fi gure 5-13).
8.
Grind lower to a sharp edge on each side. After
welding and grinding has been completed, peen
the welded area until it is shiny or until the peener
cannot dent the weld anymore (5 to 10 minutes each
side). This will work harden the welded area.
9.
Be sure to cover the lower with a heat blanket
when build-up is complete to allow it to cool slowly.
The hardsurfaced area acts like an extension of the
blades. Following these procedures will make cutting
easier and prolong the life of the blades and guide
blade.
FIGURE 5-12
FIGURE 5-13
GRAIN
GRAIN
APPROXIMATELY
2 - 3"