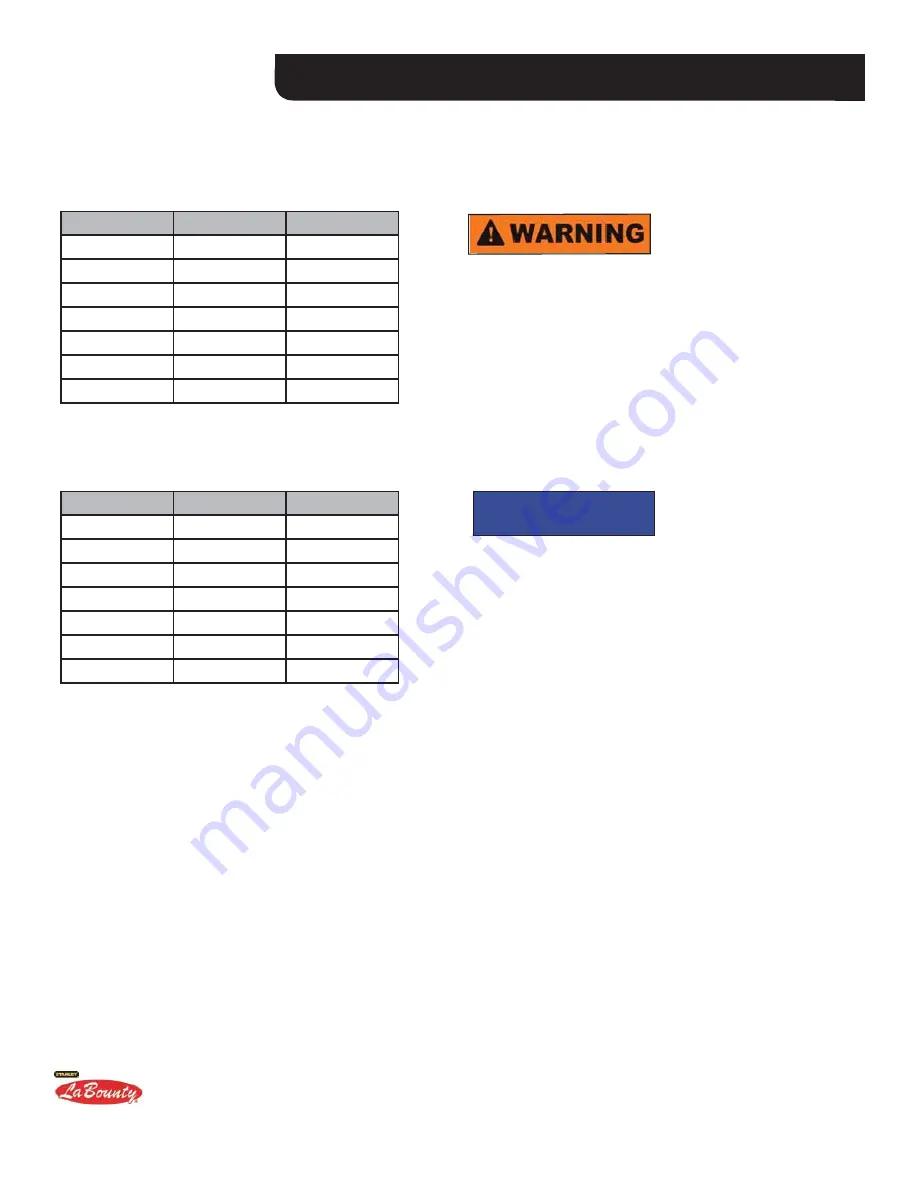
MSD 7R SHEARS
Maintenance
Section 5 Page 13
Always replace bolts and nuts with the same size
and class of fastener. Inferior fasteners can fail and
cause injury or death and damage to the equip-
ment.
SIZE
FT-LBS
N-M
M10 x 1.5
53
72
M12 x 1.75
92
125
M14 x 2
146
198
M16 x 2
224
305
M20 x 2.5
435
590
M24 x 3
752
1020
M30 x 3.5
1511
2050
METRIC CLASS 10.9
DRY BOLT TORQUE CHARTS
It is preferred to apply torque to the nut rather than
the bolt head wherever possible.
METRIC CLASS 12.9
SIZE
FT-LBS
N-M
M10 x 1.5
64
87
M12 x 1.75
110
150
M14 x 2
177
240
M16 x 2
269
365
M20 x 2.5
523
710
M24 x 3
899
1220
M30 x 3.5
1806
2450
NOTICE