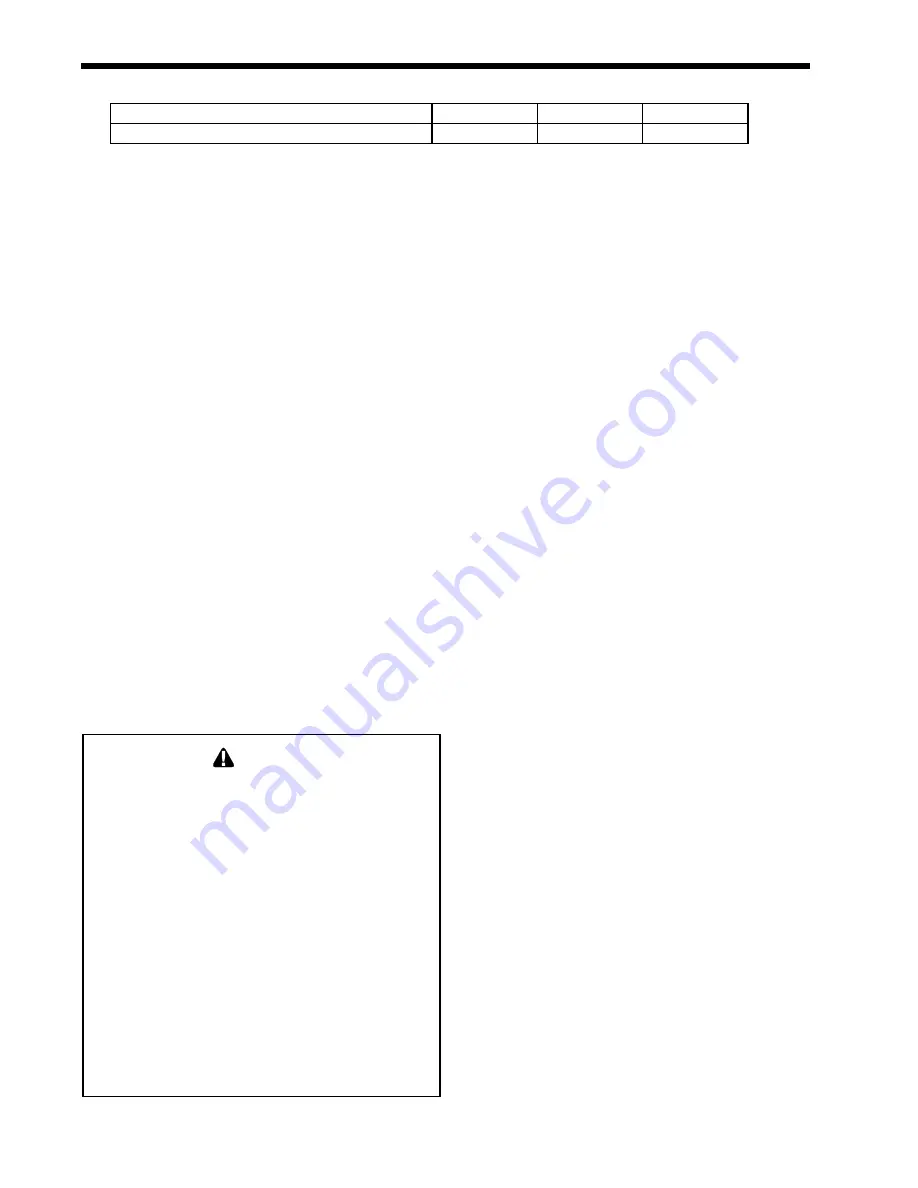
LAARS Heating Systems
Page 16
WarnInG
Do not use open flame to check for leaks. An
open flame could lead to explosion, which
could result in property damage, serious injury
or death.
note -
The MagnaTherm appliance and all
other gas appliances sharing the gas supply line
must be firing at maximum capacity to properly
measure the inlet supply pressure. The pressure
can be measured at the supply pressure port
on the gas valve. Low gas pressure could be an
indication of an undersized gas meter, undersized
gas supply lines and/or an obstructed gas supply
line. MagnaTherm units may be equipped with
low and high gas pressure switches that are
integrally vent limited. These types of devices do
not require venting to atmosphere.
Section 4
GaS SUPPly anD PIPInG
4.0
Gas Supply and Piping
Gas piping should be supported by suitable hangers
or floor stands, not the appliance. Installers should
refer to local building and safety codes or, in the
absence of such requirements, follow the national
Fuel Gas code, AnSi Z223.1 nFPA and/or cSA
B149.1 installation codes.
Review the following instructions before proceeding
with the installation.
1. Verify that the appliance is fitted for the
proper type of gas by checking the rating
plate. MagnaTherm appliances are normally
equipped to operate at elevations up to 2000
feet (610m).
However, the appliance will function properly
without the use of high altitude modification at
elevations up to 10,000 feet (3050 m).
2. The maximum inlet gas pressure must not
exceed 13” w.c. (3.2kPa). The minimum inlet
gas pressure is 4” w.c. (1.0kPa).
3. Table 8 and Table 9 offer some gas pipe sizing
information. Refer to the applicable gas code
for more detailed sizing information.
4. Run gas supply line in accordance with all
applicable codes.
5. Locate and install manual shutoff valves in
accordance with state and local requirements.
6. A sediment trap must be provided upstream of
the gas controls.
7. All threaded joints should be coated with
piping compound resistant to action of
liquefied petroleum gas.
8. The appliance and its individual shutoff valve
must be disconnected from the gas supply
piping during any pressure testing of that
system at test pressures in excess of 1/2 PSiG
(3.45kpa).
9. The unit must be isolated from the gas supply
system by closing its individual manual shutoff
valve during any pressure testing of the gas
supply piping system at test pressures equal to
or less than 1/2 PSiG (3.45kpa).
10. The appliance and its gas connection must be
leak tested before placing it in operation.
11. Purge all air from gas lines
et les fenêtres, les vientilateurs, les registre de
cheminées et les appareils au gaz àleur position
originale.
7, Tout mauvais fonctionnement du système
d’évacuation commun devrait être corrigé de
facon que l’installation soit conforme au national
Fuel Gas code, AnSi Z223.1/nFPA 54 et (ou)
aux codes d’installation cAn/cSA-B149.1. Si la
grosseur d’une section du système d’évacuation
doit être modifié pour respecter les valeurs
minimales des tableaux pertinents de l’appendice
F du national Fuel Gas code, AnSi Z223.1/
nFPA 54 et (ou) aux codes d’installation cAn/
cSA-B149.1.
3.5
outdoor Installation
if installing outdoors in a location that may experience
freezing temperatures, precautions must be taken to
prevent water in the heat exchanger and condensate
inside and outside of the boiler from freezing. Damage
due to freezing water or condensate is not covered by the
warranty.
For proper operation in outdoor installations,
the boiler must be equipped with the inlet air and
exhaust terminal kits listed in Table 7. Additional
instructions are supplied with the terminal kits.
table 7. air & Vent accessories for Units Placed outdoors
(Place in section 3.1)
Model 2000
Model 3000
Model 4000
Screen for horizontal galvanized air pipe
D2012101
D2012102
D2012103
Screen for horizontal PVC air pipe
CA012001
CA012002
CA012003
Screen for horizontal polypropylene air pipe
CA012201
CA012202
CA012203
Screen for vertical galvanized air pipe
D2012201
D2012202
D2012203
Screen for vertical PVC air pipe
CA012401
CA012402
CA012403
Screen for vertical polypropylene air pipe
CA012601
CA012602
CA012603
Table 3a - Ducted Air Accessories
(Place in section 3.2)
Model 2000
Model 3000
Model 4000
Horizontal vent terminal for stainless steel
D2012001
D2012002
D2012003
Screen for horizontal CPVC vent
CA012101
CA012102
CA012103
Screen for vertical stainless steel vent
D2012301
D2012302
D2012303
Screen for vertical CPVC vent
CA012501
CA012502
CA012503
Table 3* - Vent Accessories
(Place in section 3.5)
Model 2000
Model 3000
Model 4000
Air intake screen for unit placed outdoors
CA011901
CA011902
CA0011903
Vent terminal for unit placed outdoors
CA011801
CA011802
CA011803
Table 3** - Air & Vent Accessories for Units Placed Outdoors