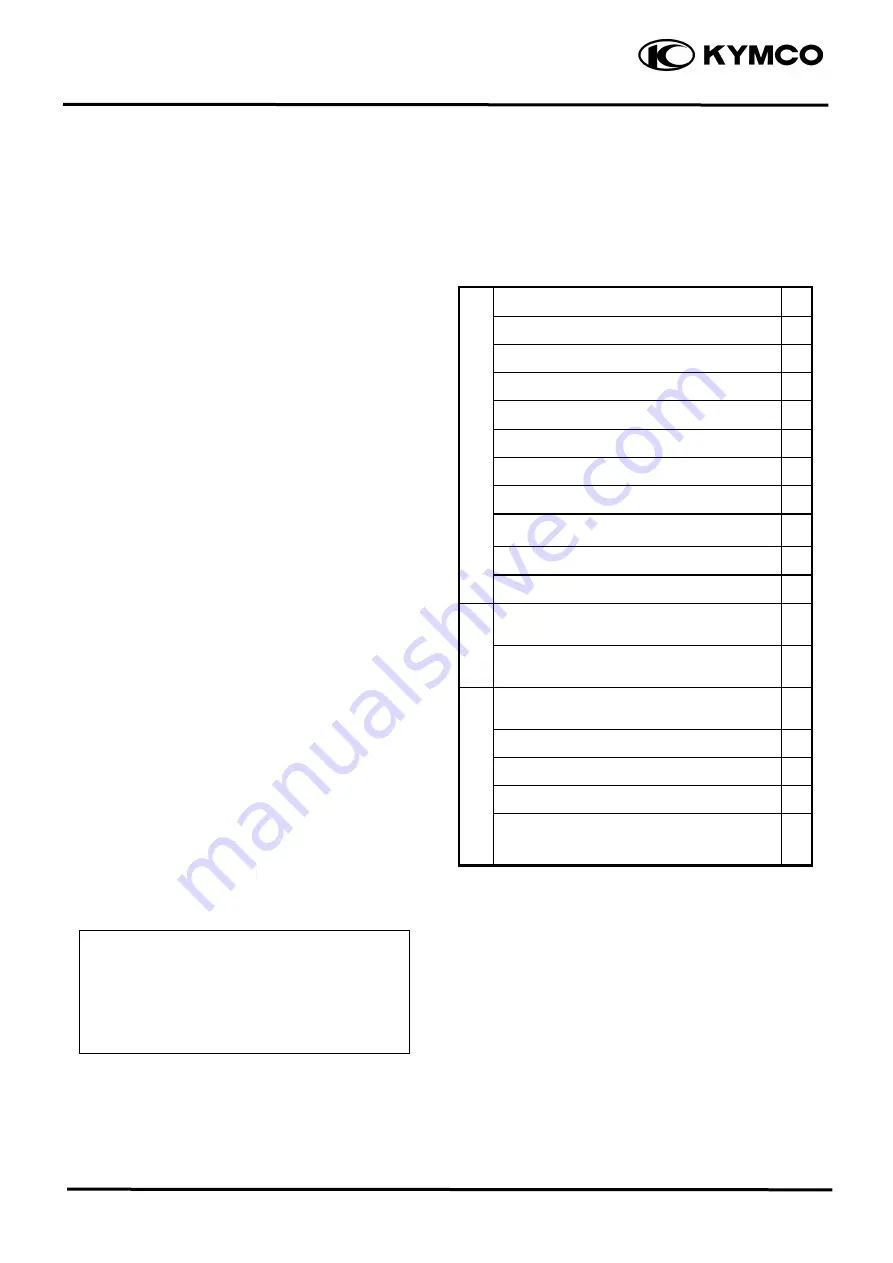
Super 8 50
PREFACE
This Service Manual describes the
technical features and servicing
procedures for the KYMCO
SUPER 8 50
Section 1 contains the precautions for all
operations stated in this manual. Read
them carefully before starting any
operation.
Section 2 is the removal/installation
procedures for the frame covers which
are subject to higher removal/installation
frequency during maintenance and
servicing operations.
Section 3 describes the inspection/
adjustment procedures, safety rules and
service information for each part, starting
from periodic maintenance.
Sections 6 through 17 give instructions
for disassembly, assembly and inspection
of engine, chassis frame and electrical
equipment.
Most sections start with an assembly or
system illustration and troubleshooting
for the section. The subsequent pages
give detailed procedures for the section.
KWANG YANG MOTOR CO., LTD.
OVERSEAS SALES DEPARTMENT
OVERSEAS SERVICE SECTION
TABLE OF CONTENTS
GENERAL INFORMATION
1
FRAME COVERS/EXHAUST MUFFLER
2
INSPECTION/ADJUSTMENT
3
LUBRICATION SYSTEM
4
ENG
IN
E
FUEL SYSTEM
5
ENGINE REMOVAL/INSTALLATION
6
CYLINDER HEAD/VALVES
7
CYLINDER/PISTON
8
DRIVE AND DRIVEN PULLEYS
9
FINAL REDUCTION
10
CRANKCASE/CRANKSHAFT
11
C
HA
S
S
IS
FRONT WHEEL/FRONT BRAKE/
FRONT SUSPENSION
12
REAR WHEEL /REAR BRAKE /REAR
SUSPENSION
13
EL
EC
TR
IC
A
L
EQ
U
IPMEN
T
BATTERY/CHARGING SYSTEM/A.C.
GENERATOR
14
IGNITION SYSTEM
15
STARTING SYSTEM
16
LIGHTS/INSTRUMENTS/SWITCHES
17
EXHAUST EMISSION CONTROL
SYSTEM
Our company reserves the right to make
any alteration in the design
.
The
information and contents included in
this manual may be different from the
motorcycle in case specifications are
changed.
18
Summary of Contents for Super 8 50
Page 19: ...1 GENERAL INFORMATION 1 18 SUPER 8 50 WIRING DIAGRAM...
Page 25: ...2 FRAME COVERS EXHAUST MUFFLER 2 0 NEW SUPER8 50 2 SCHEMATIC DRAWING 2...
Page 26: ...2 FRAME COVERS EXHAUST MUFFLER 2 1 NEW SUPER8 50...
Page 27: ...2 FRAME COVERS EXHAUST MUFFLER 2 2 NEW SUPER8 50...
Page 78: ...6 ENGINE REMOVAL INSTALLATION 6 0 SUPER 8 50 6 6...
Page 83: ...7 CYLINDER HEAD VALVES 7 0 Super 8 50 7 7...
Page 95: ...8 CYLINDER PISTON 8 0 Super 8 50 8 8 Do not bend...
Page 103: ...9 DRIVE AND DRIVEN PULLEYS 9 0 Super 8 50 9 9...
Page 117: ...10 FINAL REDUCTION 10 0 Super 8 50 10...
Page 123: ...11 CRANKCASE CRANKSHAFT 11 0 Super 8 50 11 11...
Page 129: ...12 FRONT WHEEL FRONT BRAKE FRONT SUSPENSION 12 0 Super 8 50 12 12...
Page 150: ...13 REAR WHEEL REAR BRAKE REAR SHOCK ABSORBER 1 Super 8 50...
Page 172: ...16 STARTING SYSTEM 16 0 Super 8 50 16 16 Starter Relay Starter Motor...