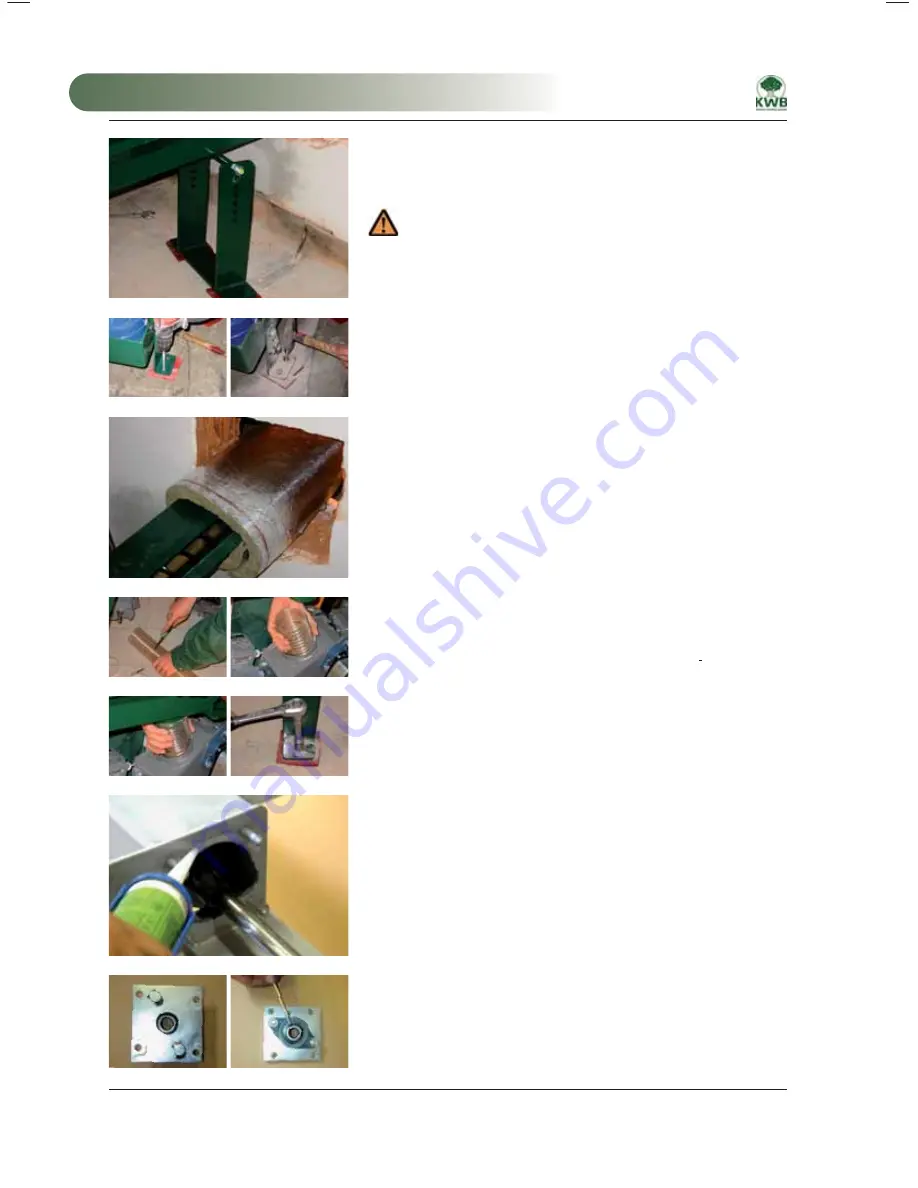
Page
140
IM Easyfire 10/2008
© KWB – Kraft und Wärme aus Biomasse GmbH
17 Pellet stirrer
17 Pellet stirrer
6.) Set up the trough supports
Fasten the screws on the trough supports and the feet of the gear unit
box in accordance with the optimal height of the worm trough.
If acoustic insulation plates are placed underneath the
supports this must be done before adjusting the height.
Acoustic insulation plates are not in the KWB scope of delivery.
Height of the trough support
Fasten the feet of the gear unit with anchor bolts.
Fasten the feet of the gear unit box
Slightly lift the worm trough, wrap the penetration sleeve around the
worm trough, bond it together and attach the sleeve cladding on the
boiler room side of the penetration.
Penetration sleeve
7.) Install the connecting hose
Measure the length of the connecting hose and cut it to size.
Lift the worm trough and connect the connecting hose including the
hose clamps to the nozzles on the drop shaft and burner
.
Connecting hose
Use hose clamps to fasten the two ends of the connecting hose to the
nozzles.
Place anchor bolts on the floor of the storage room to fasten the trough
supports and tighten the anchor bolts.
Burner & floor connection
8.) Support the conveyor worm
Apply silicon on the trough flange on the motor side all around the
recess.
Apply sealing compound
Place the flange bearing on the face side cover and fix it in place hand
tight with spring-lock washers and nuts. Align the bearing so that it is
centred and tighten the nuts. Unscrew both worm bolts on the bearing
slightly so that they are not an obstruction when sliding the bearing
onto the shaft.
MA-Easyfire 10.2008_EN.indd 140
MA-Easyfire 10.2008_EN.indd 140
30.03.2009 13:31:38 Uhr
30.03.2009 13:31:38 Uhr