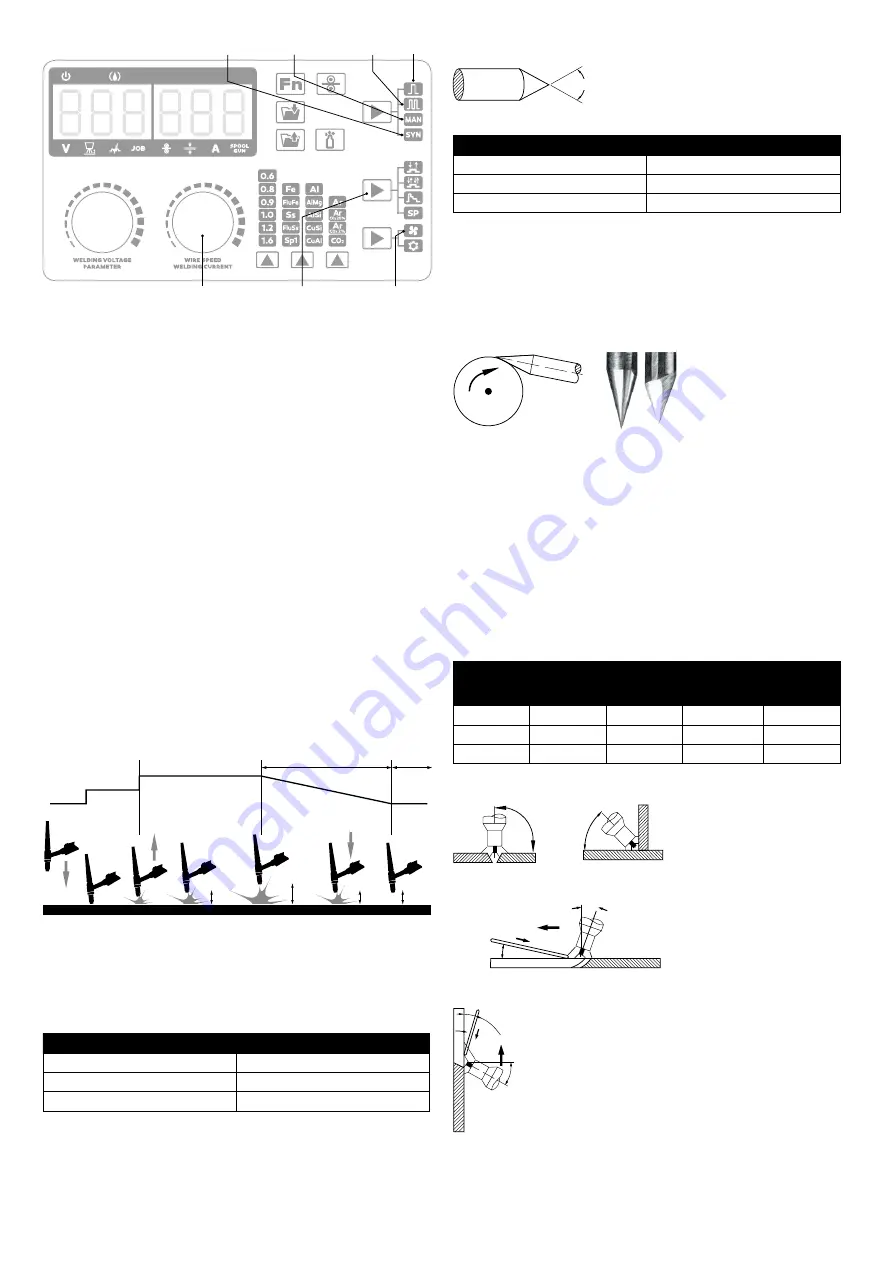
26
|
pulse
double pulse
manual
N-coder ii
control button
deactivation
synergic
Welding in method Tig
Welding inverters allow tiG welding with touch-triggering. the tiG method
is very effective for welding stainless steel.
Switch the machine to TIG mode.
1. connect the welding accessories. Welding torch on the pole (-), grounding
cable on the pole (+), connect the shielding gas.
2. turn the inverter on by the main switch. set the welding method tiG and
set the welding parameters according to the above procedure.
3. press the button on the burner.
4. release the button on the burner to end the welding process.
Welding process at TIG LA
(picture 1)
starting the gas with a valve on the welding torch.
1. approaching the tungsten electrode to the welded material.
2. light touch of tungsten electrode of welded material (no need to cut).
3. removal of tungsten electrode and arcing of welding arc with la - very low
wear tungsten electrodes by touch.
4. Welding process.
5. Finishing the welding process and activating the doWN slope (crater fi
-
lling) is performed by removing tungsten-electrodes to about 8 - 10 mm
from the welded material.
6. re-approach - Welding current decreases after the set time to the end va
-
lue set current (eg 10 a) - filling the crater.
7. end of the welding process. the digital control automatically switches off
the welding process.
switch off the gas with a valve on the welding torch.
Selection and preparation of tungsten electrodes:
table 1 shows the welding current and diameter values for tungsten
electrodes with 2 % thoria - red electrode markings.
table 1
Diameter of the Electrode (mm)
Welding Current (A)
1.0
15 - 75
1.6
60 - 150
2.4
130 - 240
prepare the tungsten electrode according to the values in table 2 and
picture 2.
picture 2
α
table 2
α (°)
Welding current (A)
30
0 - 30
60 - 90
30 - 120
90 - 120
120 - 250
Grinding of tungsten electrodes:
By proper choice of the tungsten electrode and its preparation will affect
the properties of the welding arc, weld geometry and electrode life. the
electrode must be gently grinded in the longitudinal direction as shown in
picture 3. picture 4 shows the effect of grinding the electrode on its service
life.
picture 3
picture 4
Picture 4A -
Fine and even grinding of the electrode in the longitudinal
direction - lifetime up to 17 hours
Picture 4B -
coarse and uneven grinding in the transverse direction - lifetime
5 hours
parameters to compare the influence of the electrode grinding method are
given using:
hF ignition el. arc, electrodes Ø 3.2 mm, welding current 150 a and welded
materiál - pipe.
Protective gas:
For tiG welding, it is necessary to use argon with a purity of 99.99 %. deter
-
mine the amount of flow according to table 3.
table
3
Welding current
(A)
Diameter of
electrode
(mm)
Welding nozzle
Flow of gas
(l/min)
n (°)
Ø (mm)
6 - 70
1.0
4/5
6/8,0
5 - 6
60 - 140
1.6
4/5/6
6.5/8.0/9.5
6 - 7
120 - 240
2.4
6/7
9.5/11.0
7 - 8
Holding the welding torch during welding:
90°
45°
position W (pa)
position h (pB)
10 – 30°
15 – 40°
position s (pF)
10
- 30°
20 - 30°
position s (pF)
a b
en
1
2
3
4
5
6
7
1-3 mm
1-3 mm
1-3 mm
8-10 mm
0 - 5 s
POST GAS
I
0
ON
IW
I
START
I
END
picture 1 - welding process at tiG la