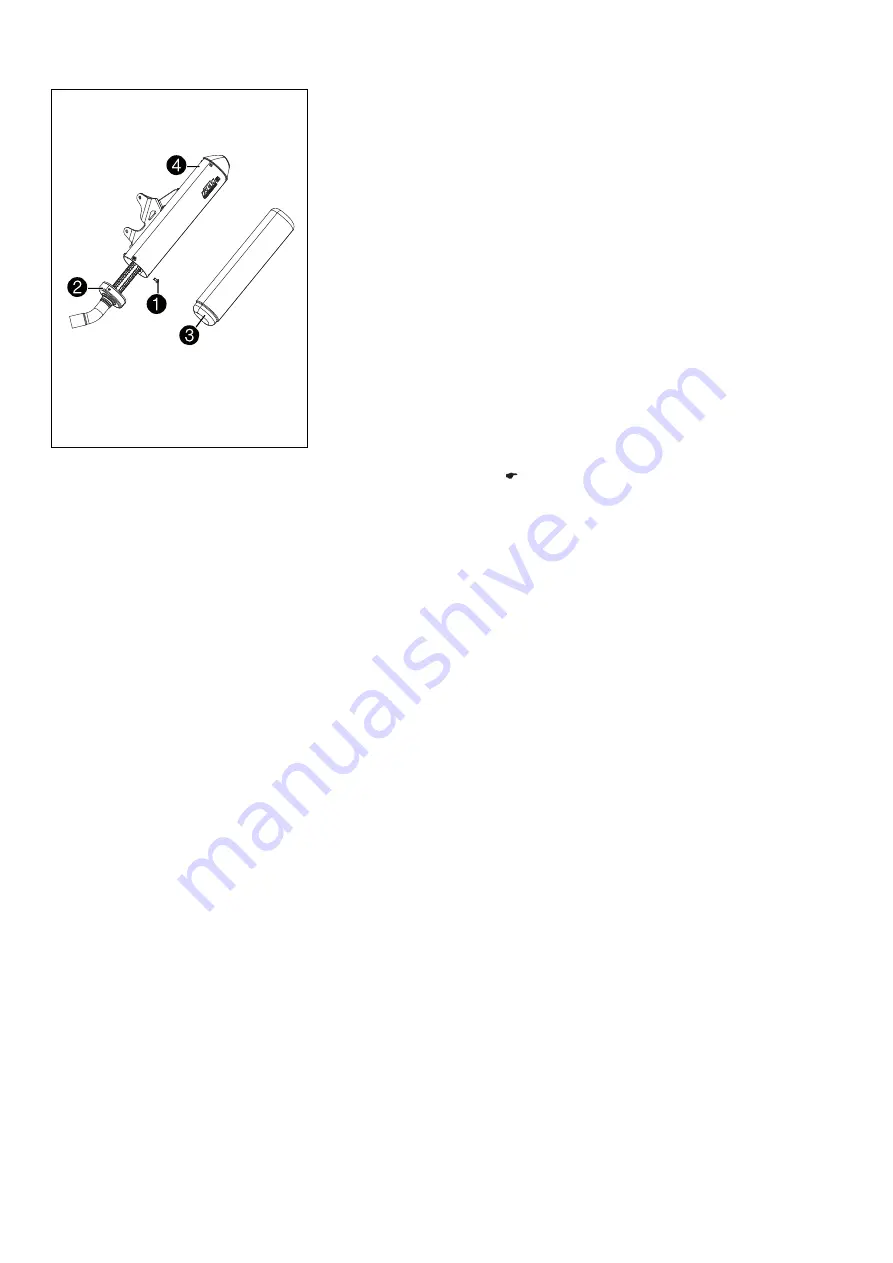
10
EXHAUST
58
B01719-10
Main work
–
Remove screws
1
. Pull out connecting cap
2
.
–
Pull glass fiber yarn filling
3
from the connecting cap.
–
Clean the parts that are to be reinstalled.
–
Mount the new glass fiber yarn filling
3
on the connecting cap.
–
Slide main silencer sleeve
4
over the connecting cap with the new glass fiber yarn
filling.
–
Mount and tighten all screws
1
.
Finishing work
–
Install the main silencer. (