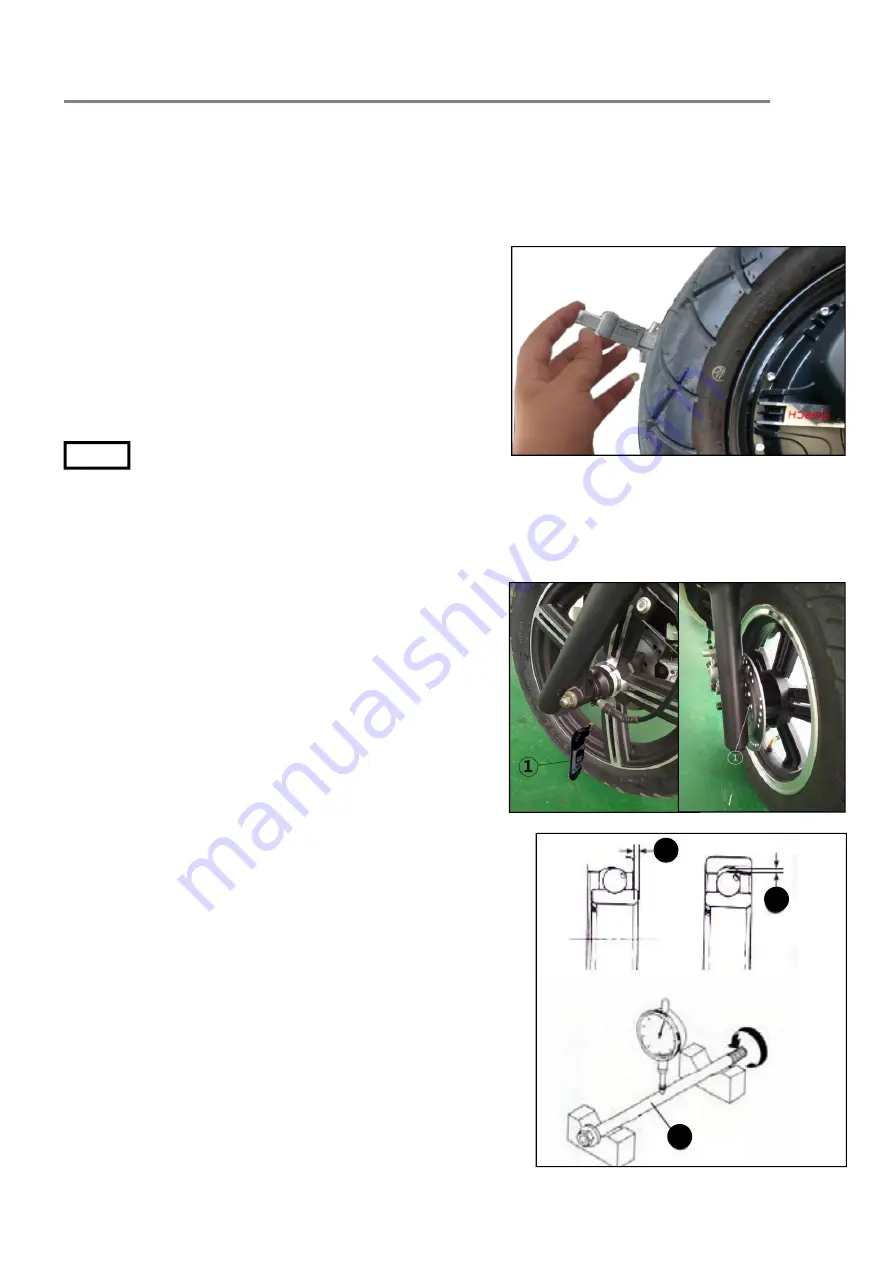
WHEELS AND TIRES
40
B
WHEELS (RIMS)
The wheel rims should be checked for cracks, bends. If any damage is found replace the rim. Do
not attempt even the smallest repair of the wheel. The wheel should be balanced whenever
either the tire or the rim has been changed or replaced. An unbalanced wheel can result in poor
performance, adverse handling characters, and a shortened tire life.
TIRES
The tires must be checked during each workshop visit.
If a tire tread shows crosswise lines (minimum tread
depth), the tire has a fragments in it, the sidewall is
cracked then replace the tire immediately.Operating the
Motorcycle with excessively worn tires will decrease the
riding stability and can lead to loss of control.Please
replace the excessive worn tires immediately.
Allowable tread limit X : Technically - 1,6 mm
Legal value may be different!
WHEEL BEARING WHEEL AXLE DAMAGE INSPECTION
The wheels rotate with difficulties .The wheel-axle
Bearing or the gear seats are in failure.To find the error,
the wheel must be removed.
1. Loose the mounting bolt (1) of the braking cylinder.
Remove components (2) of the braking cylinder.
2. Place an appropriate supporting stand under the
engine in order to raise the front wheel up.
3. Loose the mounting bolt (3) which fixing the axle
of the front wheel in order to remove the front wheel
and its axle.
4. Remove the speedometer gear seat.
5. Remove axle sheath,oil seal,axle (6200-2RS), alxe
insulating sheath axle (6200-2RS).
6. Reassemble in reverse order.
FRONT WHEEL BEARING INSPECTION
1. Examine the rolling condition of the bearing.
2. If it doesn’t roll, or the bearing is damaged or loosened,
It should be replaced.
Allowable limit (A): 2 mm
Allowable limit (B): 2 mm
INSPECT BENDING OF THE WHEEL SPINDLE
1. Put to wheel axle on a V-shape seat and use dial
Indicator to measure its eccentricity.
Allowable limit (A): 2 mm
NOTE
A
A
Summary of Contents for Ride Speedy
Page 1: ...REPAIR MANUAL Speedy Vers 2017_01...
Page 11: ...1 TIPS FOR USING THE FOUR MAJOR ELECTRICAL PARTS...
Page 13: ...2 FAILURE DIAGNOSIS...
Page 21: ...3 FAULTS AND TROUBLE SHOOTING...
Page 22: ...FAULTS AND TROUBLESHOOTING 22...
Page 23: ...FAULTS AND TROUBLESHOOTING 23...
Page 24: ...FAULTS AND TROUBLESHOOTING 24...
Page 25: ...4 PERIODIC MAINTENANCE...
Page 36: ...5 REPAIR AND DIAGNOSTICS...