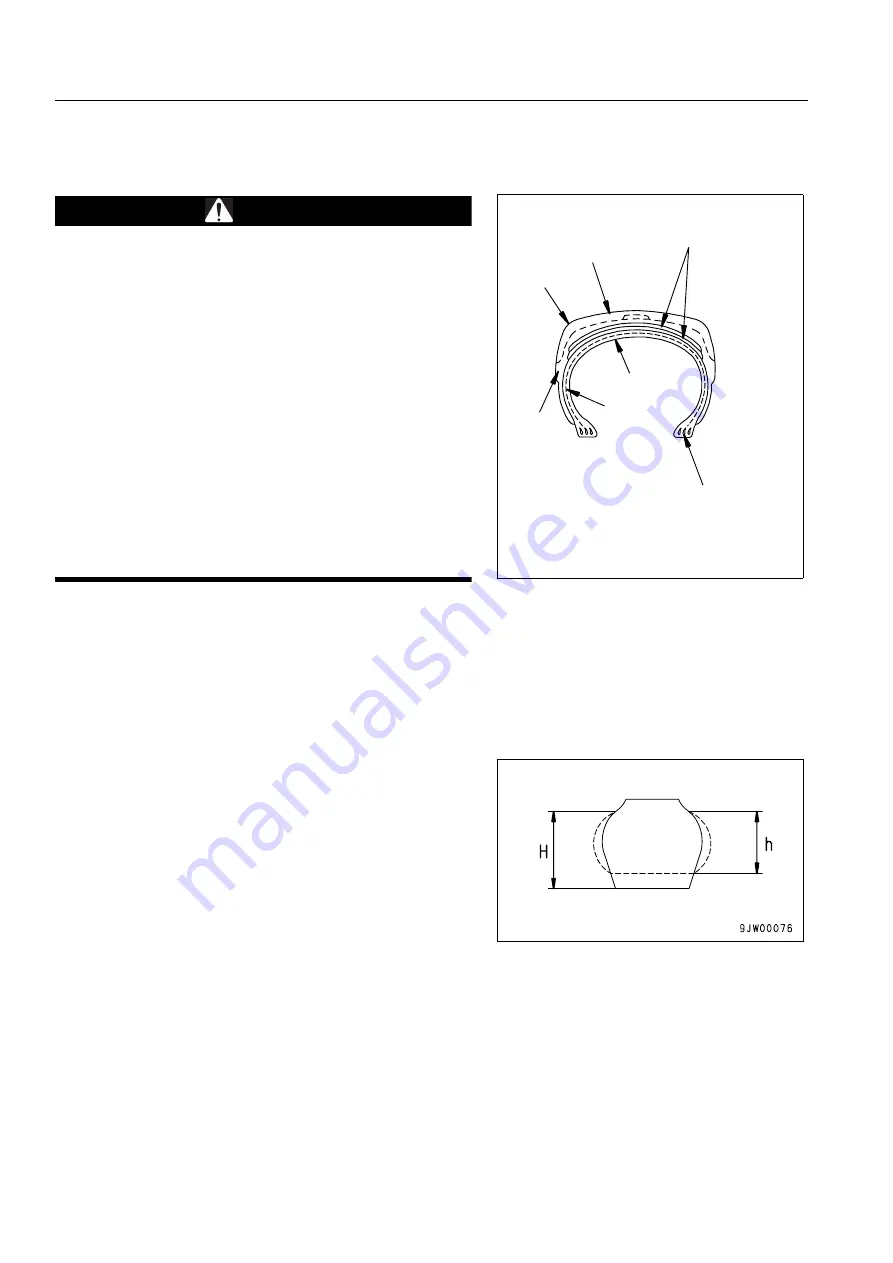
Operation
OPERATION
Handling the tires
3-96
Handling the tires
0.
Precautions when handling tires
0.
CAUTION
If a tire has reached any of the following service limits,
there is danger that the tire may burst or cause an acci-
dent, so to ensure safety, replace it with a new tire.
Service limits for wear
When the remaining depth of the groove on construction
equipment tires (at a point approx. 1/4 of the tread width)
is 15% of the groove depth on a new tire.
When the tire shows marked uneven wear, stepped
wear or other abnormal wear, or when the cord layer is
exposed.
Service limits for damage
When there is external damage extending to the cord or
when the cord is broken
When the cord is cut or there is dragging
When the tire is peeling (there is separation)
When the bead is damaged
For tubeless tires, when there is air leakage or
improper repair
Please contact your Komatsu distributor when replacing the tires. It is dangerous to jack up the machine without
taking due care.
Tire pressure
0.
Measure the tire pressure before starting operations, when the tires are cool.
If the tire inflation pressure is too low, there will be overload; if it is too high, it will cause tire cuts and shock burst.
To prevent these problems, adjust the tire inflation pressure according to the table on the next page.
Deflection ratio = H - h / H x 100
As a guideline that can be checked visibly, the deflection ratio
of the front tire (deflection/free height) is as follows.
When carrying normal load (lift arm horizontal): Approx. 15 to
25 %
When digging (rear wheels off ground): Approx. 25 to 35 %
When checking the tire inflation pressure, check also for small
scratches or peeling of the tire, for nails or pieces of metal
which may cause punctures, and for any abnormal wear.
Clearing fallen stones and rocks from the operating area and
maintaining the surface will extend the tire life and give
improved economy.
For operations on normal road surfaces, rock digging operations: High end of range in air pressure chart
Stockpile operations on soft ground: Average pressure in air pressure chart
Operations on sand (operations not using much digging force): Low end of range in air pressure chart
If the deflection of the tire is excessive, raise the inflation pressure within the limits given in the table to give a suit-
able deflection (see deflection ratio).
AE40786B-A
Breaker or belt
(cord layer)
Tread
Shoulder
Side wall
Inner liner
Carcass
Bead
Summary of Contents for WA250PT-5H
Page 2: ......
Page 3: ...FOREWORD 11...
Page 16: ...Contents FOREWORD 1 14...
Page 24: ...SAFETY 2 2...
Page 58: ...Precautions with tires SAFETY Precautions when storing tires 2 36...
Page 60: ...OPERATION 3 2...
Page 233: ...TECHNICAL DATA 45...
Page 235: ...TECHNICAL DATA Technical data 5 3...
Page 250: ...Central lubrication system ATTACHMENTS OPTIONS 6 14...
Page 251: ...INDEX 67...
Page 252: ...INDEX 7 2...
Page 255: ...Index 7 5...