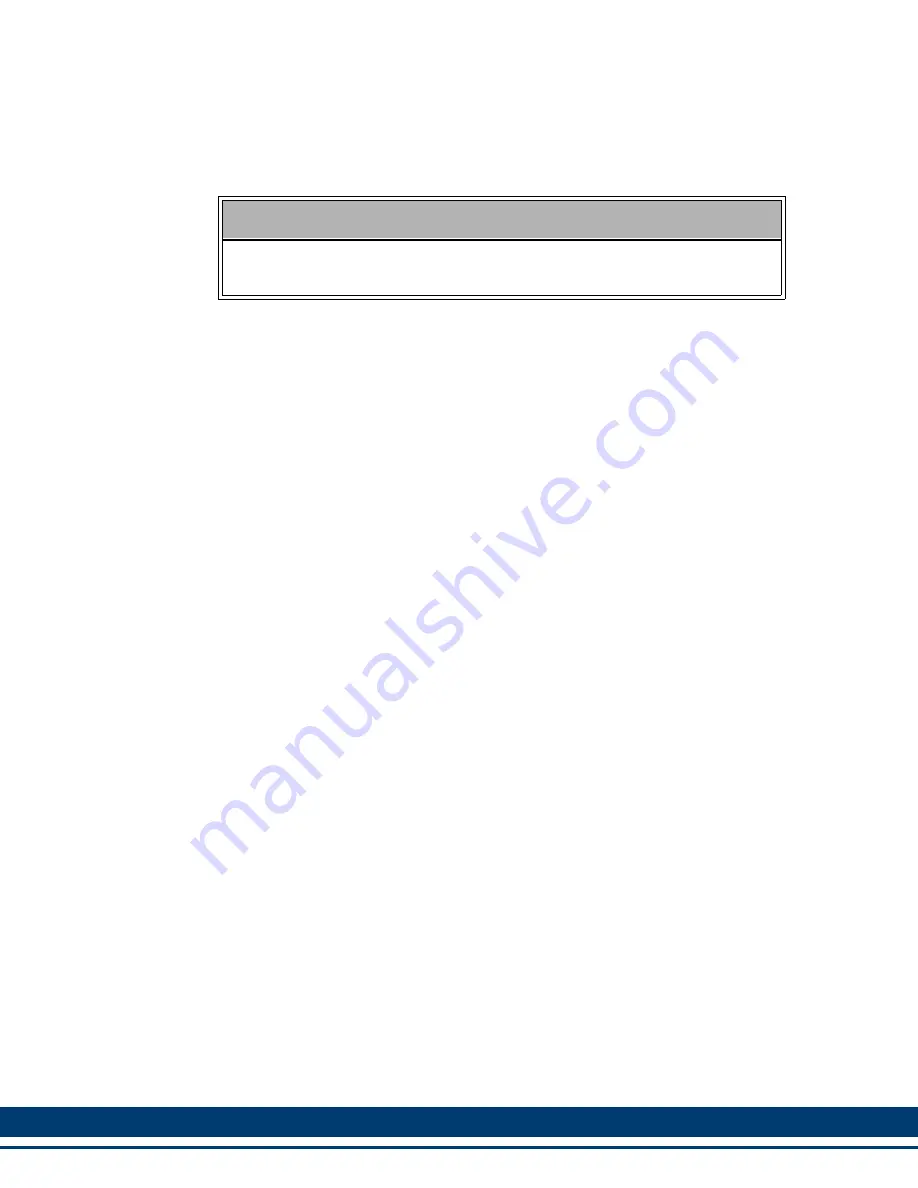
22
Kollmorgen - December 2011
MMC Smart Drive Hardware Manual
-
INSTALLING THE MMC SMART DRIVE
•
the logic power supply
•
external shunt resistors
•
line reactors
3.9
Bonding
Connecting metal chassis, assemblies, frames, shields and enclosures to reduce the
effects of electromagnetic interference (EMI) is the process of bonding.
Most paints act as insulators. To achieve a good bond between system components,
surfaces need to be paint-free or metal plated. Bonding metal surfaces creates a low-
impedance exit path for high-frequency energy. Improper bonding blocks this direct
exit path and allows high-frequency energy to travel elsewhere in the cabinet.
Excessive high-frequency energy can negatively affect the operation of the drive.
3.9.1
Bonding a Subpanel Using a Stud
1.
Weld threaded mounting studs to the back of the enclosure.
2.
Brush off any non-conductive materials (e.g. paint) from the studs.
3.
Remove any non-conductive materials from the front of the subpanel.
4.
Position the mounting holes on the subpanel over the mounting studs on the back
of the enclosure and slide the subpanel onto the studs.
5.
Attach the subpanel to the mounting stud by sliding a star washer over the stud
and then turn and tighten a nut onto the stud.
3.9.2
Bonding a Ground Bus Using a Stud
1.
Weld threaded mounting studs to the back of the subpanel.
2.
Brush off any non-conductive materials (e.g. paint) from the studs.
3.
Slide a flat washer over the studs.
4.
Remove any non-conductive materials from around the mounting hole on the
chassis mounting bracket or ground bus.
5.
Position the mounting hole of the chassis or ground bus over the studs on the
back of the subpanel and slide the mounting bracket or ground bus onto the stud.
6.
Attach the subpanel to the subpanel stud by sliding a star washer and then a flat
washer over the stud. Turn and tighten a nut onto the stud.
3.9.3
Bonding a Ground Bus or Chassis Using a Bolt
1.
Brush off any non-conductive materials (e.g. paint) from the threaded bolt (s).
2.
Slide a star washer over the threaded bolt (s).
3.
Use a subpanel having tapped mounting holes. Remove any non-conductive
materials from around the mounting holes on both sides of the subpanel.
CAUTION
If the MMC Smart Drive is operated outside the recommended environmen-
tal limits, it may be damaged. This will void the warranty.
Summary of Contents for Digital MMC Control
Page 2: ......
Page 10: ...8 Kollmorgen Decamber 2011 MMC Smart Drive Hardware Manual TABLE OF CONTENTS...
Page 128: ...126 Kollmorgen December 2011 MMC Smart Drive Hardware Manual 230V 1 3 PHASE MMC SMART DRIVE...
Page 214: ...212 Kollmorgen December 2011 MMC Smart Drive Hardware Manual 460V 3 PHASE MMC SMART DRIVE...
Page 246: ...244 Kollmorgen December 2011 MMC Smart Drive Hardware Manual MOTOR CABLES CONNECTORS...
Page 298: ...296 Kollmorgen December 2011 MMC Smart Drive Hardware Manual DECLARATIONS OF CONFORMITY...
Page 299: ...Kollmorgen December 2011 297 MMC Smart Drive Hardware Manual DECLARATIONS OF CONFORMITY...
Page 300: ...298 Kollmorgen December 2011 MMC Smart Drive Hardware Manual DECLARATIONS OF CONFORMITY...
Page 301: ...Kollmorgen December 2011 299 MMC Smart Drive Hardware Manual DECLARATIONS OF CONFORMITY...
Page 302: ...300 Kollmorgen December 2011 MMC Smart Drive Hardware Manual DECLARATIONS OF CONFORMITY...
Page 320: ...MMC Smart Drive Hardware Manual INDEX 318 Kollmorgen March 2011...
Page 322: ...320 Kollmorgen December 2011 MMC Smart Drive Hardware Manual SALES AND SERVICE...