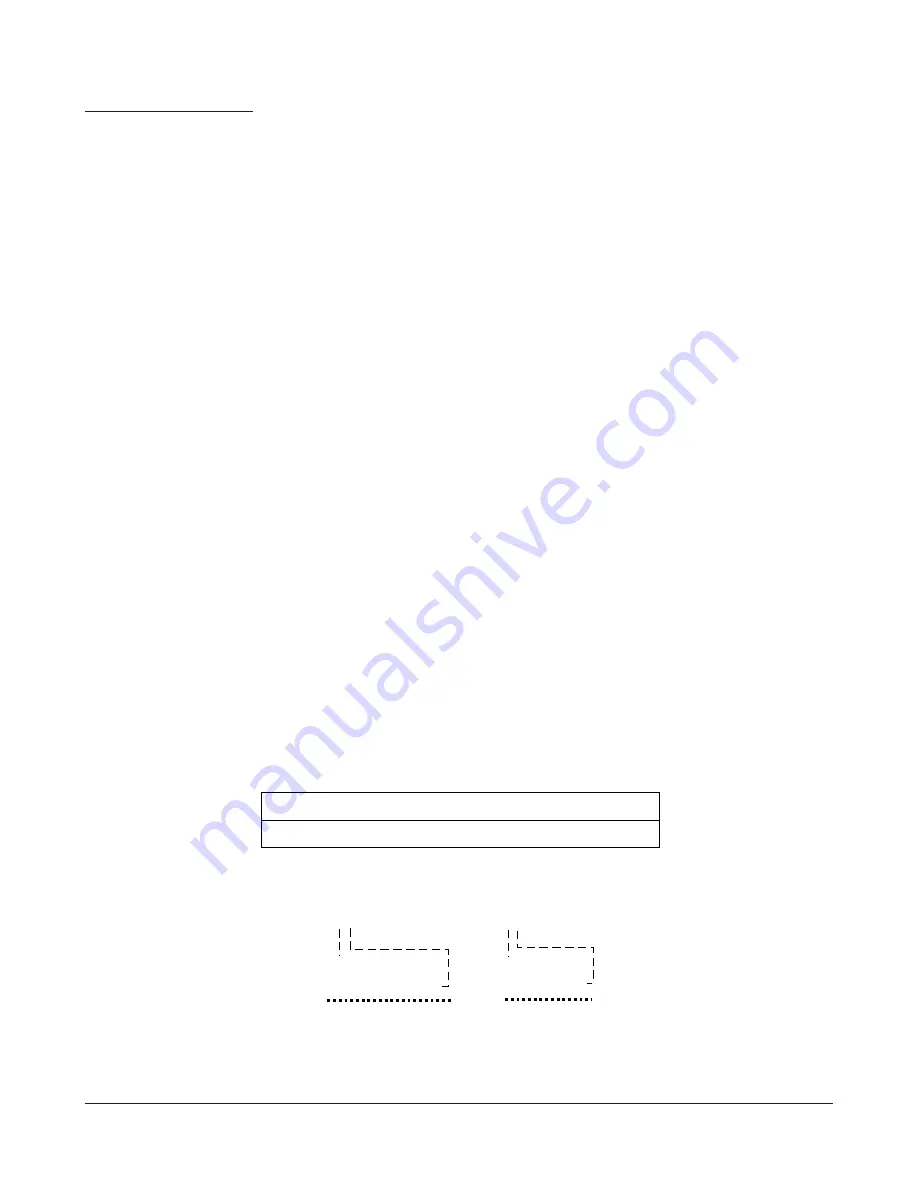
4. PARAMETER
INTRODUCTION
The purpose of the PARAMETERS is to optimise the function of the ML2000 ( ML2000 P).
There are 2 types of PARAMETERS. The value of the first type ends with an H (for example
18H) and the second type ends with a D (for example 15D). The H means this is a
hexa-decimal value. The D means this is a decimal value. Only the PARAMETERS with
hexa-decimal value can be altered by keying in a new value. The PARAMETERS with
decimal values can only be altered by starting a special option.
PARAMETER ..................................................................................................CHANGE WITH OPTION
CASSETTE-OFFSET......................................................................................CASSETTE-LENGTH
MAGAZINE LEVEL .........................................................................................SCAN RUN
HOME POSITION ...........................................................................................SCAN RUN
GEAR BACKLASH..........................................................................................SCAN RUN
NEARLY EMPTY ............................................................................................NEARLY EMPTY
For every hexa-decimal PARAMETER an allowed range exists.
For example LOWER POCKET:
RANGE ............................................................................................................0h....64h
DEFAULT ........................................................................................................40h
This means every value between 0h and 64h can be used. It does not mean that with every
value the ML2000 (ML2000 P) works best. In general the MINILOADER works best with the
DEFAULT (or STANDARD) setting. If a value outside the range is used and ENTER is
pressed, the displayed value will default automatically to the DEFAULT VALUE.
The range is different for every PARAMETER.
If the PARAMETER represents a time, 1 increment is 10 msec.
If the PARAMETER represents a distance, 1 increment is 0.09 mm.
If you need to convert a hexadecimal number to decimal, use the following procedure:
F F
1 5 x 1 6 = 2 4 0
+ 1 5
= 2 5 5
1 A
1 x 1 6 = 1 6
+ 1 0
= 2 6
d e c 0 1 2 3 4 5 6 7 8 9 1 0 1 1 1 2 1 3 1 4 1 5
h e x 0 1 2 3 4 5 6 7 8 9 A B C D E F
SM 3477
PARAMETER
KODAK AG, Stuttgart
4-1
6/1997