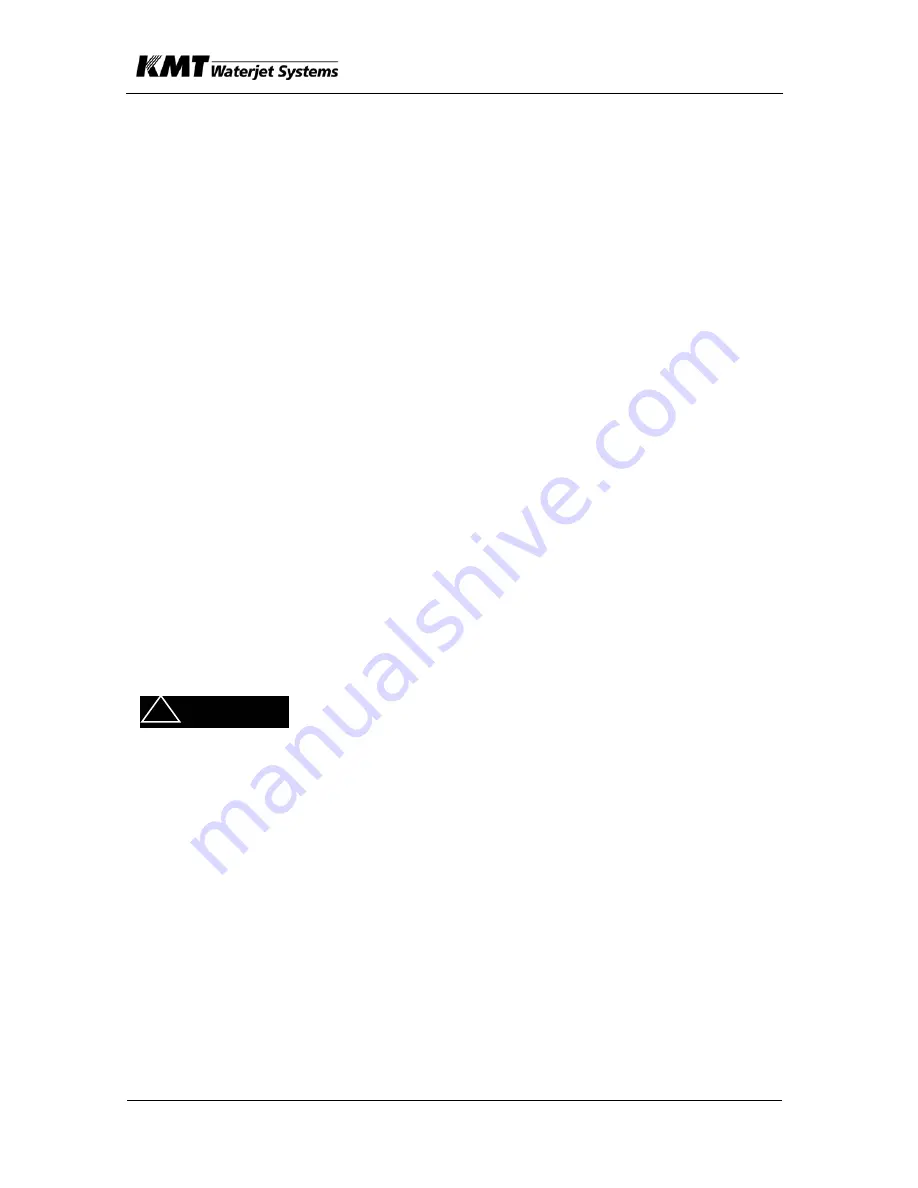
SECTION 7
HIGH PRESSURE WATER
May 2003
p. 7-6
49831951
CAUTION
!
5.
Remove sealing head. Note that a white plastic ring used to position the
sealing head relative to the HP cylinder bore may not have been removed
with the sealing head. This ring should be removed prior to re-installing
a sealing head to avoid pushing the ring further into the HP cylinder
bore. Note that a fully- assembled spare sealing head greatly reduces
pump downtime.
Re-Assemble Sealing Head and End Flange to HP Cylinder
1.
Verify that sealing head cone surface is smooth. Perform any necessary
maintenance on inlet check valve. (Refer to paragraph 7.3.2) Verify that
a white plastic alignment ring is installed on the ‘nose’ of the sealing
head. Verify O-rings (2 ea) properly installed in ID grooves of end flange.
Check HP cylinder bore to verify presence of plastic tubular cylinder liner
and to verify that no white plastic alignment ring remains in end of HP
cylinder bore. Feel sealing edge of HP cylinder bore to verify that no
unusual blemishes are present that might hinder proper cone ring seal.
2.
Install sealing head into end flange. Install sealing head and end flange
over stud bolts and into cylinder bore. Note that end flange should be
oriented with the LP water fitting oriented near the 9 o’clock or 3 o’clock
positions for ease of making the LP water connection.
3.
Thread nuts onto studs to hand-tightness. Apply molygrease to stud
threads (Table 7-2 item 3). Verify end flange and ring flange are parallel
to within 0.070-inch.
4.
Tighten stud nuts (using a torque wrench) in a crossing pattern in
several stages to reach maximum torque. See Table 7.1 for suggested nut
tightening sequence. Verify flange parallelism at completion of tightening
sequence.
5.
Re-connect HP and LP piping / hoses per paragraph 7.2.1 above.
Verify that proximity switches (2 ea) are properly installed
Failure to tighten proximity switch hold down screws will
result in hydraulic oil spraying in general directions.
6.
Restart the pump, first operating in LOW pressure mode to flush out air
in HP components and also to check for obvious leaks. Switch to HIGH
pressure after 5-10 minutes of LOW pressure operation, watching for
obvious leaks. Be ready to shut off the pump if leaks appear. Remedy
leaks then repeat start procedure, moving from LOW pressure to HIGH
pressure soon after intensifier starts pumping water (no further need to
flush air from lines).
Summary of Contents for STREAMLINE SL-IV PLUS
Page 44: ...SECTION 6 LOW PRESSURE WATER May 2003 6 4 05148390 Figure 6 2 LP Cutting Water Supply Circuit ...
Page 78: ...SECTION 7 HIGH PRESSURE WATER May 2003 p 7 30 49831951 ...
Page 82: ...SECTION 8 ELECTRICAL SYSTEM Aug 2002 p 8 4 49836323 ...
Page 111: ...SECTION 12 PARTS LISTS July 2003 page 12 5 49836349 ...
Page 113: ...SECTION 12 PARTS LISTS July 2003 page 12 7 49836349 ...
Page 115: ...SECTION 12 PARTS LISTS July 2003 page 12 9 49836349 ...
Page 117: ...SECTION 12 PARTS LISTS July 2003 page 12 11 49836349 ...
Page 119: ...SECTION 12 PARTS LISTS July 2003 page 12 13 49836349 ...
Page 121: ...SECTION 12 PARTS LISTS July 2003 page 12 15 49836349 ...
Page 123: ...SECTION 12 PARTS LISTS July 2003 page 12 17 49836349 ...
Page 125: ...SECTION 12 PARTS LISTS July 2003 page 12 19 49836349 ...
Page 127: ...SECTION 12 PARTS LISTS July 2003 page 12 21 49836349 ...
Page 129: ...SECTION 12 PARTS LISTS July 2003 page 12 23 49836349 ...
Page 131: ...SECTION 12 PARTS LISTS July 2003 page 12 25 49836349 ...
Page 133: ...SECTION 12 PARTS LISTS July 2003 page 12 27 49836349 ...
Page 135: ...SECTION 12 PARTS LISTS July 2003 page 12 29 49836349 ...
Page 137: ...SECTION 12 PARTS LISTS July 2003 page 12 31 49836349 ...
Page 139: ...SECTION 12 PARTS LISTS July 2003 page 12 33 49836349 ...
Page 141: ...SECTION 12 PARTS LISTS July 2003 page 12 35 49836349 ...
Page 143: ...SECTION 12 PARTS LISTS July 2003 page 12 37 49836349 ...
Page 145: ...SECTION 12 PARTS LISTS July 2003 page 12 39 49836349 ...
Page 146: ......
Page 147: ......