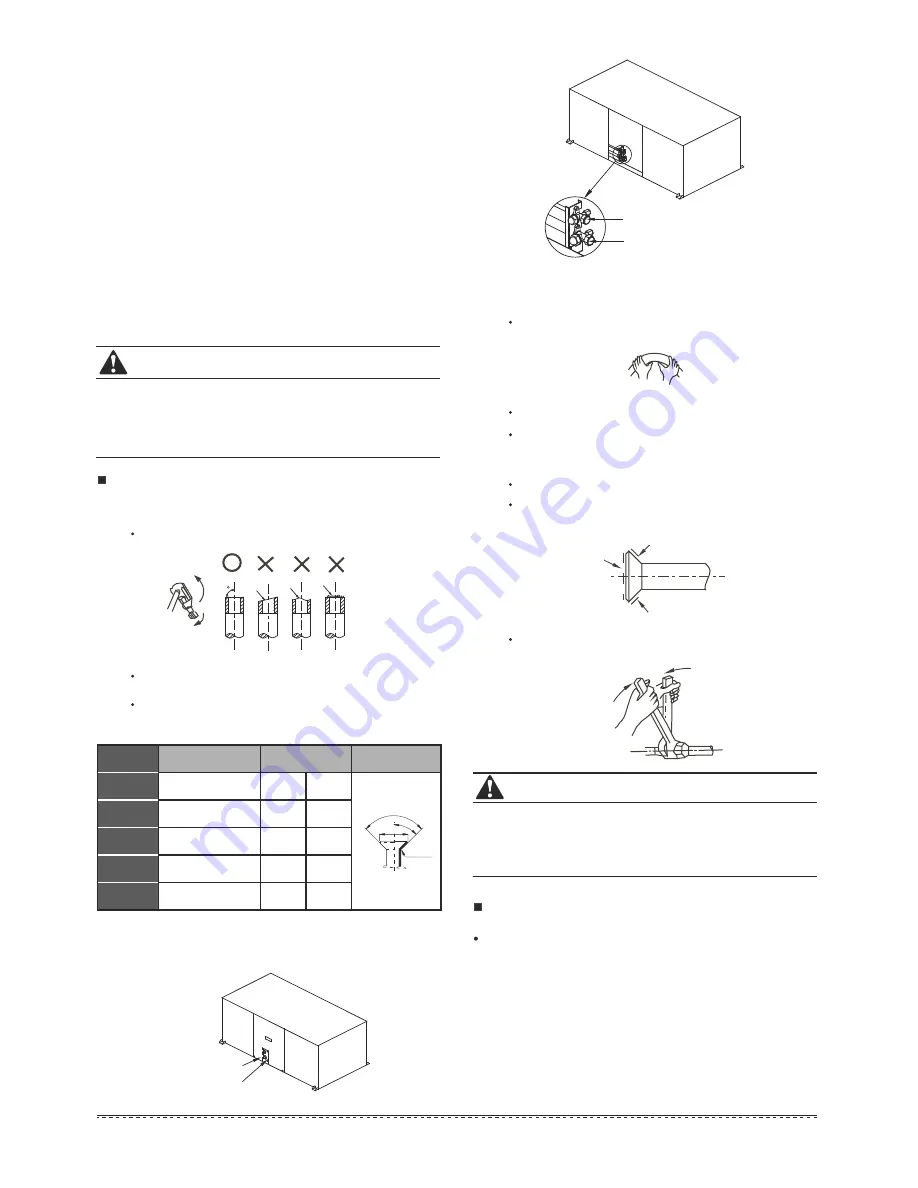
installation manual
10
Bind the connecting pipe and the cables together tightly with
binding tapes.Pass the bound connecting pipe through the
wall conduct from outside. Be careful of the pipe allocation to
do on damage to the tubing.
Connect the pipes. Refer to "How to Connect the pipes" for
details.
Expel the air with a vacuum pump. Refer to "How to expel the
air with a vacuum pump" for details.
Open the stop values of the outdoor unit to make the
refrigerant pipe connecting the indoor unit with the outdoor
unit in fluent flow.
Check the leakage. Check all the joints with the leak detector
or soap water.
Cover the joints of the connecting pipe with the soundproof /
insulating sheath (fittings), and bind it well with the tapes to
prevent leakage.
2
3
5
6
7
4
Be sure to with insulating materials cover all the exposed
parts of the flare pipe joints and refrigerant pipe on the
liquid-side and the gas-side. Ensure that there is no gap
between them.
Incomplete insulation may cause water condensation.
CAUTION
How to Connect the pipes
Flaring
1
Cut a pipe with a pipe cutter.
(Refer to Fig.7-1)
Insert a flare nut into a pipe and flare the pipe.
Refer to Table 7-2 for the dimension of flare nut spaces.
Fig.7-1
90
Lean crude burr
4
Bend the tubing in proper way. Do not harm to them.
Connect the indoor unit at first, then the outdoor
unit.
Too large torque will harm the bellmouthing and too small
will cause leakage. Please determine the torque
according to Table 7-2.
After the connecting work is finished, be sure to check
that there is no gas leak.
When connecting the flare nut, coat the flare both inside
and outside with either oil or ester oil and initially tighten
by hand 3 or 4 turns before tighting firmly.
Be sure to use both a spanner and torque wrench
together when connecting or disconnecting pipes to /from
the unit.
Bend the pipe with thumb
min-radius 100mm
Fig.7-4
Fig.7-5
Fig.7-6
How to expel the air with a vacuum pump
Stop valve operation introduction
1. Opening stop valve
1.
2.
3.
Remove the cap and turn the valve counter
clock-wise with the hexagon wrench.
Turn it until the shaft stops.Do not apply excessive force
to the stop valve. Doing so may break the valve body,
as the valve is not a backseat type. Always use the
special tool.
Make sure to tighten the cap securely.
CAUTION
Table 7-2
Ø6.4
8.3
8.7
Ø9.5
12.0
Ø12.7
15.4
Ø15.9
Ø19.1
18.6
22.9
R0.4~0.8
45 °
± 2
90 °
± 4
A
65
~
67N.m
(663
~
684 kgf.cm)
45
~
47 N.m
(459
~
480 kgf.cm)
35
~
36 N.m
(357
~
367 kgf.cm)
25
~
26N.m
(255
~
265 kgf.cm)
15
~
16 N.m
(153
~
163 kgf.cm)
(mm)
min
max
Pipe gauge
Tightening torque
Flare dimensin A
Flare shape
12.4
15.8
19.0
23.3
2
Remove the Cycle Service Panel and the Cover
Board, unscrewing the screws which secure it to
the structure
3
Remove the protection cover of stop valve
Fig.7-3
Liquid Valve
Gas Valve
The bending angle should not exceed 90.
Bending position is preferably in the middle of the
bendable pipe. The larger the bending radius the better it
is.
Do not bend the pipe more than three times.
Fig.7-2
Cycle Service Panel
Cover Board