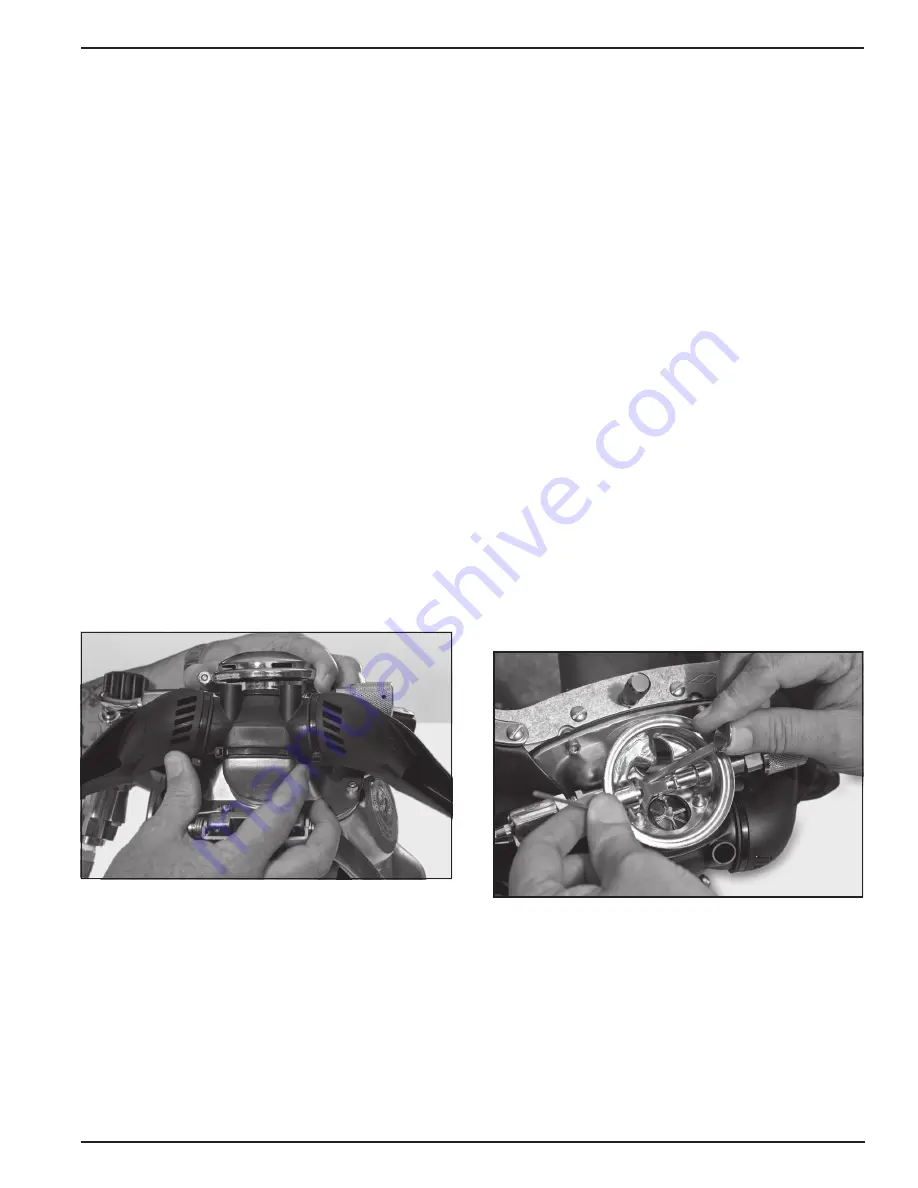
© ⅯⅯⅩⅢ Kirby Morgan Dive Systems, Inc. All rights reserved. Document # 130318002
107
Kirby Morgan
®
37SS
Chapter 7 - Reassembly of the SuperFlow® 350 Demand Regulator
Ensure that the Teflon
®
ring is in place and engage
the bent tube nut to the side block fully until it is hand
tight. You may need to gently rock the regulator body
and/or the bent tube to fully engage side block nut.
Next, fully engage (clockwise) the large nut on the
bent tube into the regulator inlet until hand tight. This
will ensure the nut is bottomed on the shoulder on
the bent tube. Do not tighten further.
Loosen the jam nut on the regulator inlet (counter
-
clockwise), and engage the jam nut fully to the large
nut on the bent tube. Using a torque wrench and an
7/8"
open end wrench hold the large nut on the regu
-
lator end of the bent tube and tighten the jam nut to
40 inch pounds.
22) Ensuring the O-ring is in place, use a torque
wrench with a 1
3/8
" socket and an extension to tighten
the regulator mount nut to 100 inch pounds. Next us
-
ing a torque wrench with an
11/16
adapter, torque the
bent tube nut to the side block to 100 inch pounds.
23) Attach the whisker to each side of the face port
retainer using the screws, plates and spacers, use
Loctite
®
222. Using a torque wrench with a flat blade
screwdriver adapter, carefully torque these screws to
12 inch pounds.
The Quad Valve must be properly connected to the regulator
and the quad exhaust extension on the pod.
24) Adjust the regulator following instructions in
this chapter.
Make sure diaphragm & mating surfaces are clean
and free of lube.
25) Install the diaphragm, cover, t and screw. Tighten
the screw to 12 inch pounds using a torque screw
-
driver, after all adj. and fine tuning are complete.
7.13.1 Tuning the SuperFlow
®
350 Regulator
1) If not already done, remove the clamp, cover and
diaphragm.
2) Screw the adjustment knob (clockwise) all the way
in, towards the regulator body.
3) Pressurize the regulator to between 120-150 p.s.i.g.
of supply pressure.
4) Screw the adjustment knob out (counterclockwise)
until the regulator starts to free flow, then screw the
adjustment knob in (clockwise) until the free-flow
just stops. Depress the lever several times to ensure
the free-flow has stopped.
If the free flow does not stop, the adjustment nut
is too tight. If the roller lever is sloppy (loose) the
adjustment nut is too loose.
5) Insert the inlet valve holding tool into the balance
hole on the inlet tube. Push forward on the tool only
hard enough to stop the inlet valve stem from turn
-
ing. Adjust the nut until there is
1/16
inch (1.5 mm) to
1/8
inch (3.0 mm) of free play at the end of the lever.
Insert the inlet valve holding tool into the balance hole on the
inlet tube.
6) Remove the inlet valve holder tool.
7) Put the diaphragm and cover in place, depressing
the cover tightly to simulate a properly tightened
clamp.
8) Depress the purge button in the center of the cover.