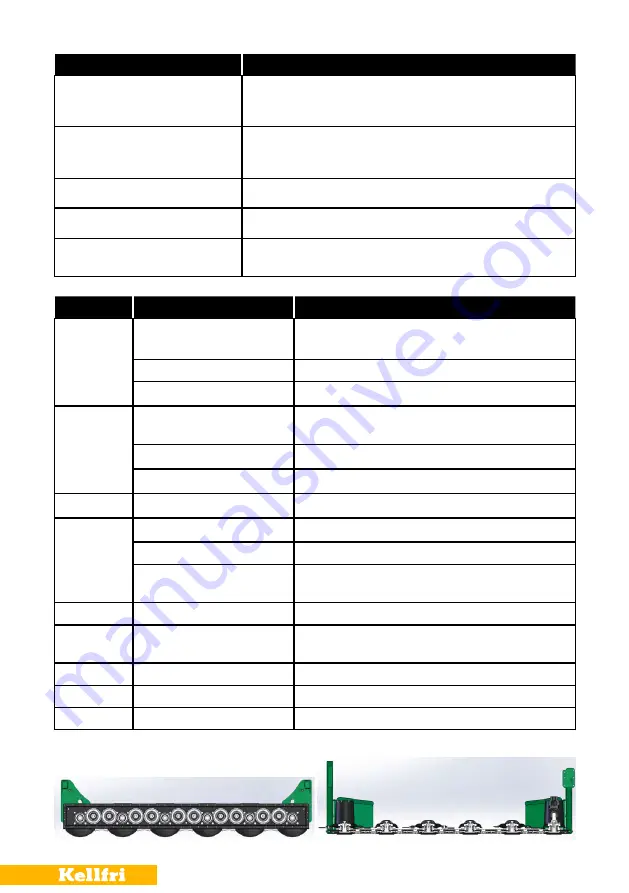
32
SERVICE
INTERVAL
MEASURE
Blades
Before each use
Replace all defective blades. Sharp blades give better results.
When replacing blades, tighten bolts fully.
While operating
Listen out for noises
After each use
Check
Discs
Before each use
Replace all defective discs.
When replacing blades, tighten bolts fully.
While operating
Listen out for noises
After each use
Check
Bolts/nuts
After one hour of operation
Re-tighten all bolts and nuts.
Gearbox/cut-
terbar
Before each use
Check oil level.
Before first operation
First oil change.
300 operating hours or a minimum
of once a year
Oil change
Rotor
After 20 hours of operation
Lubrication
Belts
After one hour of operation
Check and tighten the belt.
The belt should move 20 mm under pressure.
Hydraulics
Before each use
Check that all hoses are intact, connected and leak-proof.
The equipment After each use
Wash off earth and grass with water.
Piston rods
For extended storage, piston rods should be lubricated.
FAULT
MEASURE
Rotary disc mower cuts unevenly or badly
Check that the blades are intact and firmly in position.
Check the drive belts and tighten if necessary.
The cutting sound changes
Check the tension of the drive belts.
Check that the blades are properly tightened.
Vibrations
Check that the blades are properly tightened.
Hydraulics do not work
Check hoses and connections
Accumulation of material on the rotary
disc mower
Operating speed is too slow - increase speed.
Summary of Contents for 35-FDM240
Page 14: ...14 Table of Contents PARTS...
Page 18: ...18 Table of Contents M16x45 M16 M16 38 x 25 x 24 mm M24 M24 M24...
Page 20: ...20 Table of Contents Secure with the chain Banjo bolt Sealing washer...
Page 23: ...23 Table of Contents GREASE POINTS...
Page 34: ...34 Table of Contents Version 1 1...
Page 38: ...38 Table of Contents Version 1 1...
Page 40: ...40 Table of Contents Version 1 1...
Page 43: ...43 Table of Contents ROTATION PATTERN 35 FDM240 Turning the blades is not recommended...
Page 44: ...44 Table of Contents NOTES...
Page 45: ...45 Table of Contents NOTES...
Page 46: ...46 Table of Contents NOTES...