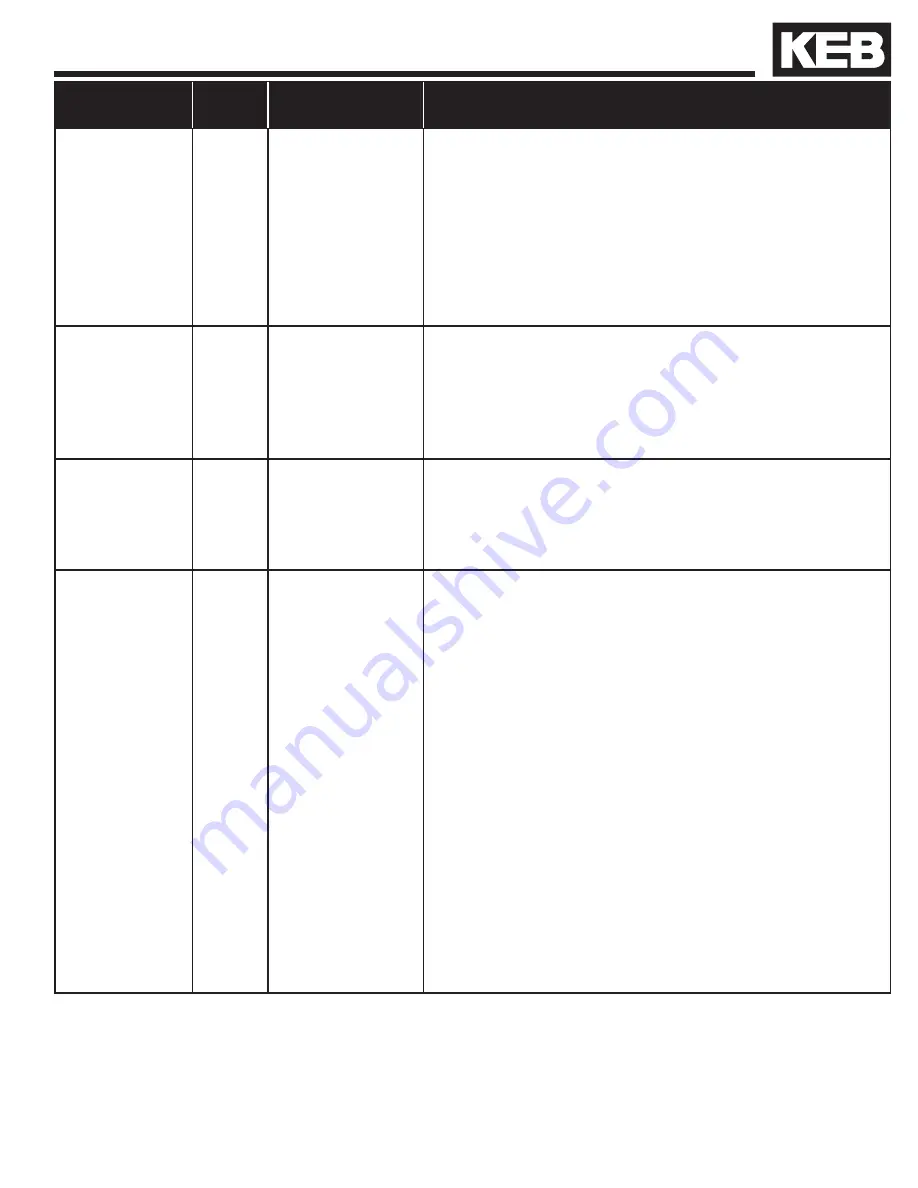
89
Drive Faults
Error/Message Alt. /
(NUM)
Description
Cause/Solution/Troubleshoot
Data Unspeci-
fied
-
When LE12 =
Data Unspeci-
fied, the encoder
memory is not
formatted.
Encoder memory has not been formatted. To fix, enter
2503 into Password to access drive parameters. Next,
from the Program menu, hit F4 for File. Select Inverter
parameter and then scroll down to user definition param-
eters. Set ud.1 to 2206 for supervisor access. Hit ESC
twice to get back to the inverter parameter menu. Scroll
to encoder parameter and set ec.38 = 2. Power cycle
drive and LE12 should read “Position Transfer.”
Direction Se-
lection Failure*
-
(161)
Both directions
signaled at begin-
ning of run.
For LI15 = Up (I5) and Down (I6) inputs, the up/down
directions must independently be selected. If both are
selected simultaneously, the ‘Direction Selection Failure’
fault will occur, but not during UPS Operation Mode (refer
to LI04 UPS Operation for further details).
Drive Enable
Switched Off*
-
(162)
Drive Enable (I7)
input dropped
while current
output.
Will occur whenever the Drive Enable (I7) is dropped
while current is being output. Check input signal con-
nections, sequence, or reason for abrupt stop. (eg. emer-
gency stop, clip door lock, etc.)
Error Calculate
Motor Data
ECdd
(60)
The inverter is
unable to learn
a value during
the Motor Learn
procedure, SPI,
or during auto-
matic learn of the
encoder position
during each run.
Verify correct motor data is entered in LM01-07 and re-try.
Make sure motor contactor is closing.
Make sure motor is wired correctly.
Change LM27 to 1, Ld = Lq and test again.
If the problem occurs during an SPI, the following proce-
dure can be done instead...
Verify LM27 Motor Inductance Mode is set to Ld = Lq.
Set LE07 Rotor Detection Mode to NOP.
Prevent brake from releasing, set inspection speed = 0.
Give inspection command to allow sample to be taken.
Check the value in LE06 Encoder Pole Position.
Repeat several times to ensure consistency in LE06.
Samples should not vary by more than 2,000 counts.
Set LE07 to OFF and proceed as normal.
Summary of Contents for COMBIVERT F5
Page 1: ...COMBIVERT F5 ELEVATOR DRIVE Operation Manual Version 3 33 00F5LUM K333...
Page 4: ......
Page 136: ...136 Notes...
Page 137: ...137...