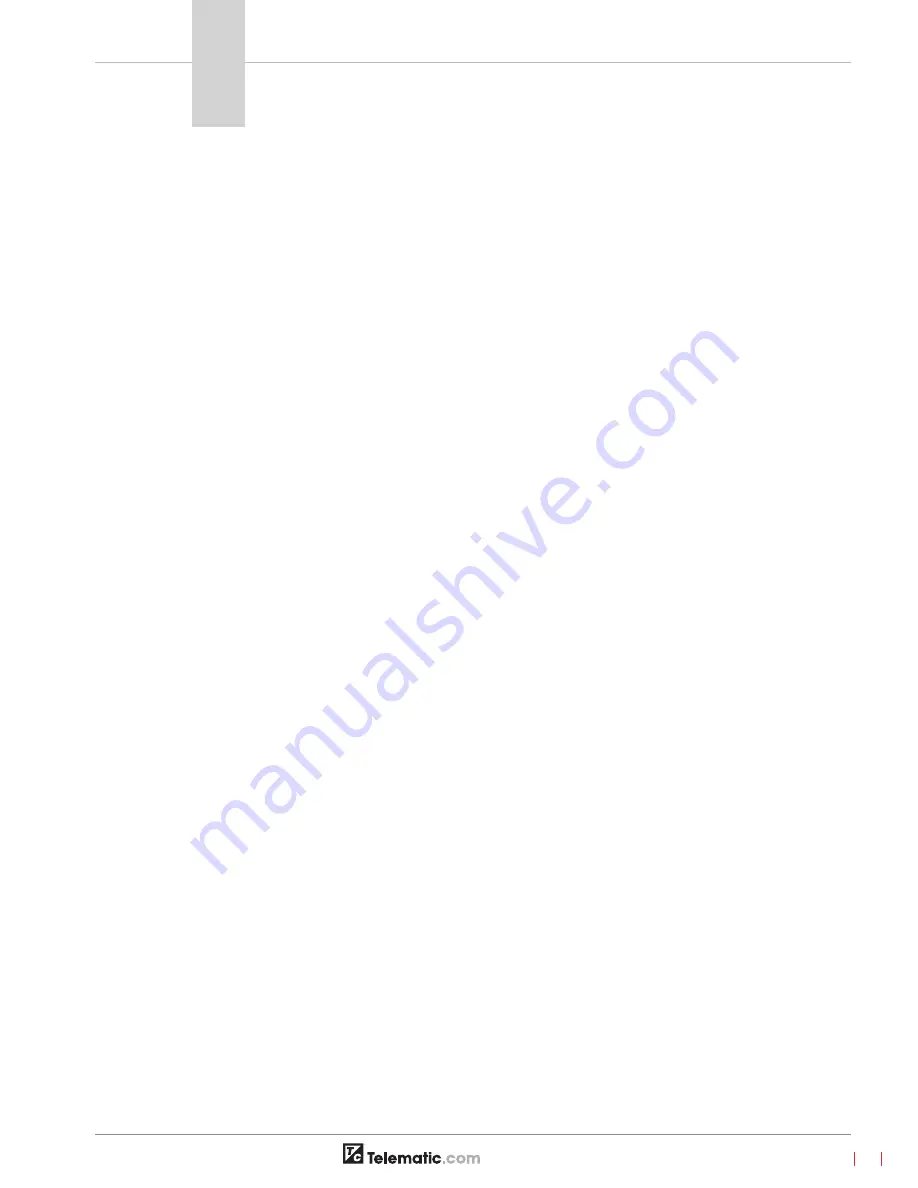
4
Thermal Dispersion
Quick Setup Guide
Shop Online
K
A
Y
D
EN
INSTRUM
EN
T
S
nd
22
ANNIVERSARY
2016
1994
Telematic Controls Inc.
3364 –114th Avenue S.E. Calgary, Alberta, Canada T2Z 3V6
Tel:
(403) 253-7939
Fax:
(403) 255-0042
Web:
telematic.com
DOC#: QG-800-004
Effective: January 2016
Supercedes: October 2015
POWER, AC/DC
Either AC or DC voltage can be used to power the
CLASSIC:
•
For AC power, connect the HOT line to VAC-H,
the NEUTRAL to VAC-N and the GROUND wire to
the green grounding screw, also indicated by the
ground symbol.
•
For DC Power, connect the positive voltage to
+VDC and the common or negative to COM.
CAUTION
Never power on the circuits in a potentially explosive area
without fi rst installing the enclosure cover.
Always lock the cover in place. This may be required by
your local safety or electrical code.
NOTE:
For fail-safe installations, the desirable relay
state is usually energized and the circuit closed. Use
the normally open contacts for fail-safe installations
since they are closed when the relay is energized.
MAINTENANCE
Your Kayden instrument requires very little maintenance
as there are no moving parts.
Without detailed knowledge of the environment
parameters of the application surroundings and
process data media, Telematic cannot make specific
recommendations for periodic inspection, cleaning, or
testing procedures. Telematic does however suggest
general guidelines for maintenance (see the CLASSIC
Product Manual). Use operating experience to establish
the frequency of each type of maintenance.
CALIBRATION
The CLASSIC does not require any calibration for
use as a switch/transmitter. Once properly setup,
the CLASSIC will be as stable and repeatable as the
process in which it is installed. It may be necessary
to check or repeat the setup procedure if the process
changes dramatically over time.
HEATER POWER
The CLASSIC uses a 2-watt heater that can be set
between 0 - 100%, in 5% increments.
•
Since the energy added by the heater is used
in determining the Thermal Signal, altering the
amount of heat changes the Thermal Signal.
•
If the heater power is changed more than 5% (1
LED) this may require the 0% & 100% Thermal
Signal to be similarly adjusted in order not to lose
sensitivity and reaction time.
•
The Factory Default Heater Power setting of 75%
(1.5 watts) is suitable for most Flow applications
with Hydro-carbons.
•
GUIDELINES FOR SETTING HEATER POWER:
•
30 - 60% heater power (7-13 LEDs)
-
Air or Gas (Flow) (depending on velocity)
•
60 - 75% heater power (13-16 LEDs)
-
Oil or Hydrocarbon based liquids (Flow,
Level & Interface)
•
80 - 100% heater power (17-21 LEDs)
-
Water or non-viscous liquids (Flow,
Level & Interface)
The faster the flow rate (velocity) the more heat is
required. In level applications the amount of heat, in
part, determines the reaction time.
The CLASSIC 800 Series has a “Smart Heater” function
(see the
“Classic 800 Product Manual”
). If a heater
operates constantly in a no flow or dry condition, a
“Thermal Offset” can occur. This means the heater
may affect the reading from the reference RTD. The
microprocessor will automatically reduce the heater
power setting to a lower power rating when the probe
is “dry” or in a “no-flow” condition. When the process
media touches the sensors, or flow begins again, the
original heater power setting is restored.
!
RELAY OUTPUTS
The CLASSIC features two independent set points
each with its own mechanical relay for output. The
connections for the contacts of these relays are:
R1COM
Common or pole contact for Relay 1
R1NC
Normally closed contact for Relay 1
when the coil is not energized
R1NO
Normally open contact for Relay 1
when the coil is not energized
R2COM
Common or pole contact for Relay 2
R2NC
Normally closed contact for Relay 2
when the coil is not energized
R2NO
Normally open contact for Relay 2
when the coil is not energized
QG-800-004-[007]
This is a Controlled Document and cannot be changed without the Approval of the Quality Control Manager.
35
Shop Online
CLASSIC 800 Product Manual
Maintenance
Section
5
I. GENERAL INFORMATION
With proper installation the CLASSIC 800 will require very little maintenance, as there are no moving parts
subject to wear. Following a few simple guidelines will ensure years of dependable service.
1. Cover
In accordance with CSA, FM, UL and local codes the cover must be properly installed at all times. The
threads of the cover should be lightly coated with a lubricating compound to prevent seizing, freezing and
corrosion. Spray lubricants are not recommended.
2. Process and Conduit Connections
•
In accordance with CSA, FM and local codes all power and communication wiring should be enclosed
either in conduit or an approved jacketed cable. Ensure that the electrical connection made at the
enclosure of the CLASSIC 800 meets all codes and requirements.
•
As described in detail in Section 2 “Installation Guidelines”, ensure that the sensor is installed with
the proper orientation, to the proper depth and coat threads with a thin layer of thread tape or sealant/
lubricant.
•
Most Fault conditions and reported “failures” are actually caused by loose, broken or improper electrical
connections. Ensure that the connections for the sensor, input power and relay output are correct and
secure.
3. Sensing Elements
•
The alloy (Stainless Steel, Titanium, Hastelloy, etc.) sensors require no periodic maintenance, but any
deposits or scaling should be removed from the sensor tip as necessary. Use the appropriate cleaning
device or material relative to your process (example: cloth, brush, wire brush, steel wool, sandpaper,
water, detergent, compatible solvents to the sensor material, etc.).
Notes:
As described in detail in Section 2 “Installation Guidelines”, proper physical installation of the
sensor is critical to the operation of the switch/transmitter in terms of sensitivity and response
time. Because sediment will collect at the bottom of any vessel, and entrained gases will
always collect at the top of any vessel, ensure sensing tip is inserted to a point where it will be
constantly and fully exposed to the desired process media. Avoid locations where sediment may
accumulate and eventually isolate the sensing tip from the process.