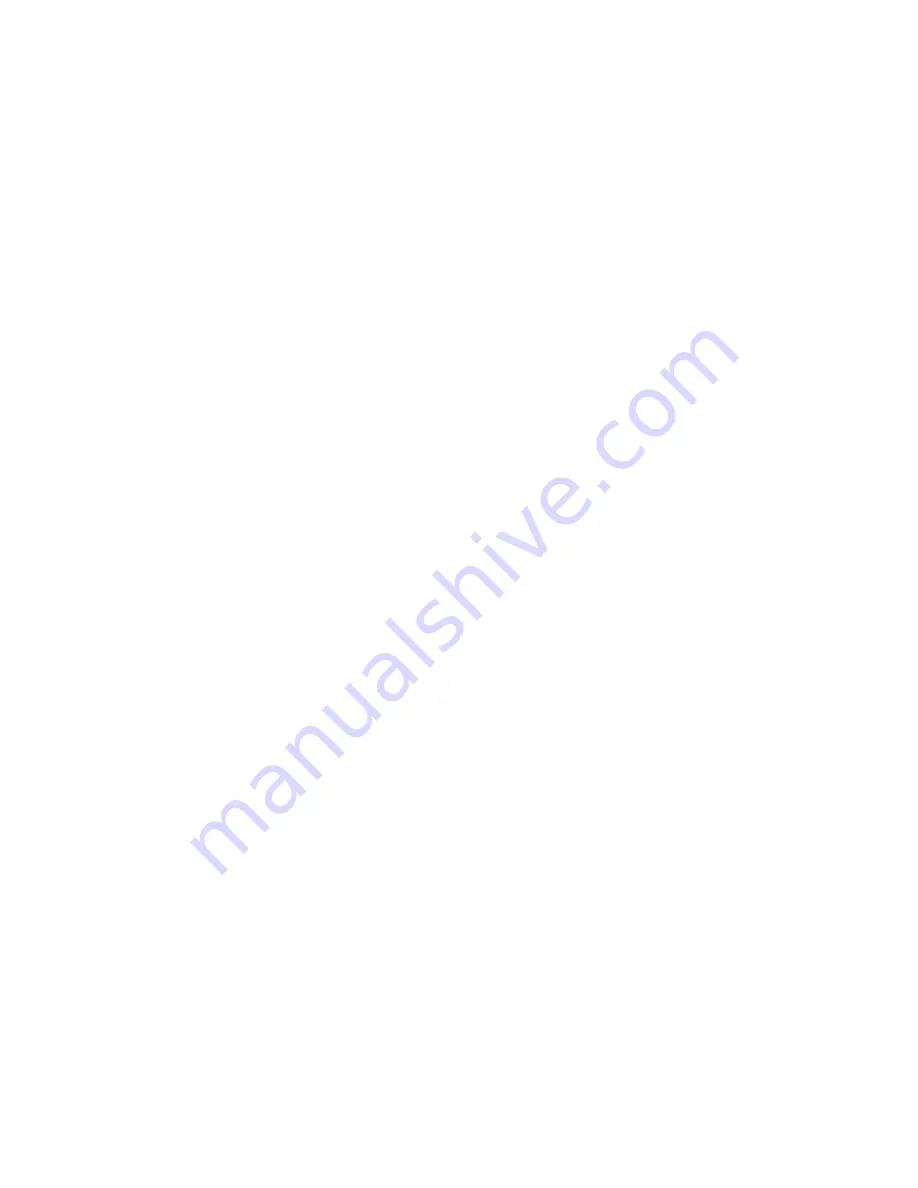
Page 31
Copyright © 2012 Kato Engineering, Inc. All rights reserved
NOTICE: Rotor removal should be
performed only as necessary and based
on the level of contamination and / or a low
Insulation Resistance value.
With generators that have ball or roller bearings, check machine
vibrations and bearing condition with a spectrum analyzer or shock
pulse.
Regrease the regreaseable-type bearings. With generators that have
sleeve oil bearings, inspect bearing oil for proper levels and clarity.
Every 8000 hours or 1 year of operation
Check insulation resistance to ground on all generator windings,
including the main rotating assembly, the main stator assembly, the
exciter fi eld and armature assemblies, and the optional PMG assembly.
Check the space heaters for proper operation.
Check the rotating rectifi er connection tightness.
With generators that have sleeve oil bearings, replace the bearing oil.
Every 20,000 hours or 3 years of operation
With generators that have sleeve oil bearings, perform a sleeve bearing
inspection to include the removal of the upper bearing housing and
bearing liner to inspect the liner, shaft journal, and seal surfaces for wear
or scoring.
Remove the endbrackets, and visually inspect the generator end windings
for oil or dirt contamination. Excessive contamination may necessitate
surface cleaning with compressed air and electrical solvent.
Inspect the fan and fan hub for damage.
Every 30,000 hours or 5 years of operation
(Contact Kato Engineering for assistance)
Disassemble generator.
Clean the generator windings using either (depending upon the severity
of contamination) 1) compressed air and electrical solvent or 2) de-
greaser and high pressure hot water wash. Dry the windings to acceptable
resistance levels (see the dry out procedure).
Inspect the rotor shaft bearing journals for wear or scoring.
With generators that have ball or roller bearings, replace the bearings.
With generators that have sleeve bearings, replace the bearing liners and
oil seals.