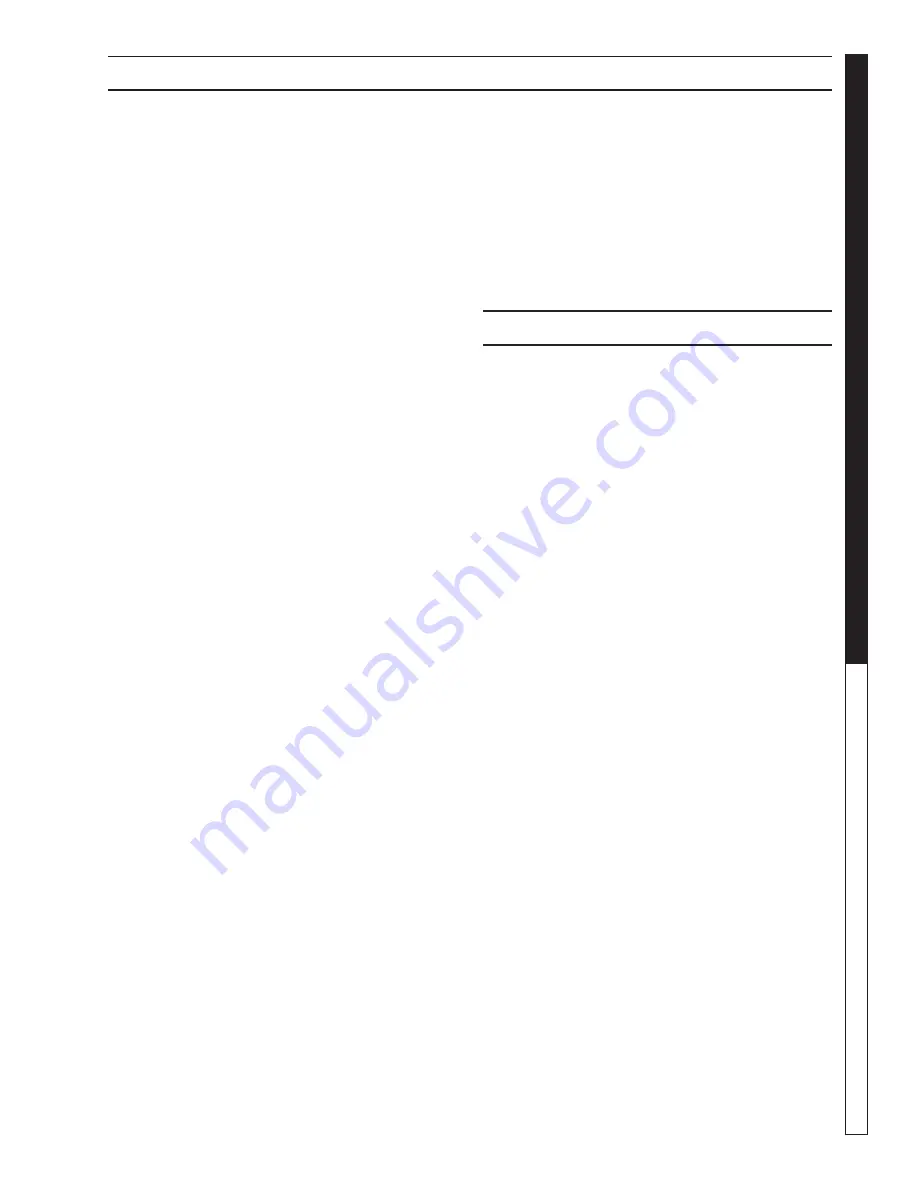
9.801-509.0 - C • Karcher Operator's Manual
25
PRESSURE W
ASHER
MAN
U
AL
MAINTENANCE AND SERVICE
Spray Nozzles:
Each machine is equipped with one or more spray
noz zles, de pend ing on the model. Different spray
noz zles are cal i brat ed for each machine, depending on
the fl ow and pres sure of that particular model. Spray
nozzles vary in bore size and angle of spray. Popular
spray angles are 0°, 15°, 25°, 40°. When ordering,
please specify size and angle of nozzle. Nozzle size
for each machine is located on the serial plate.
Unloader Valves:
Unloader valves relieve pressure in the line when a
spray gun is closed. Unloader valves are pre set and
test ed at the factory before shipping. Oc ca sion al ad-
just ment of the unloader may be necessary to main tain
cor rect pres sure. For valve adjustment contact your
nearest dealer or call technical support. Tampering
with the factory setting may cause personal injury and/
or property damage, and will void the manufacturer's
warranty.
Winterizing Procedure:
Damage due to freezing is not covered by warranty.
Adhere to the following cold weather procedures when-
ev er the wash er must be stored or operated out doors
under freez ing conditions.
It is necessary to protect your machine against freez-
ing when temperatures drop below 32° F. Si phon ing a
small amount of antifreeze into the sys tem is rec om-
mend ed. This is done by pouring a 50-50 mix of an ti-
freeze and wa ter into the fl oat tank and then si phon ing
100% an ti freeze through the detergent line with the
pump on. If com pressed air is avail able, an air fi t ting
can be screwed into the fl oat tank strain er fi t ting, and
by in ject ing com pressed air, all water will be blown out
of the system. The use of a draft diverter will prevent
the wind chill fac tor from freez ing the coil.
Low Pressure Diagnosis:
(Machines with spray gun)
Refer to Troubleshooting Chart for low pressure. If the
trou ble is found to be either the unloader or the pump,
your next step is to determine which is the problem.
This can be done by eliminating the unloader from the
sys tem and at tach ing the 50' discharge hose di rect ly
to the pump. If high pres sure is developed in this man-
ner, the pump is good and the unloader needs to be
repaired or replaced. If low pressure is still present,
then the pump needs re pair ing.
CAUTION: When using this procedure to test
com po nents keep the spray gun open at all times.
High Limit Hot Wa ter Thermostat:
For safety, each machine is equipped with a high limit
con trol switch. In the event the temperature of the wa ter
should exceed its operating temperature, the high limit
control will turn the burner off until the water cools.
Pumps:
Use only SAE 20/40 weight non-detergent oil. Change
oil af ter fi rst 50 hours of use. Thereafter, change oil
ev ery three months or at 500 hour intervals. Oil level
should be checked through use of the dipstick found
on the top of the pump or by the red dot visible through
the oil gauge window. Oil should be maintained at
that level.
HEATING COILS
To Check Water Heater Coil for Leaks:
With the main burners “OFF” start the pumping unit
and allow it to run for a few minutes. Check into the
burner com part ment with a drop light or fl ashlight. If
no leaks are vis i ble, then water dripping from coils is
con den sa tion from the fl ue gases when the burners
are on.
Condensation from Heating Coil:
When cold water is being pumped into the water heat er
coils, and the burners are on, condensation will form on
the coils and drip down into the burner com part ment,
giv ing the ap pear ance of a leaking coil, par tic u lar ly
on cold humid days.
Deliming Coils:
In alkaline water areas, lime deposits can ac cu mu late
rap id ly inside the coil pipes. This growth is in creased
by the extreme heat build up in the coil. The best
pre ven tion for liming conditions is to use high quality
clean ing de ter gents. In areas where alkaline water is
an extreme prob lem, pe ri od ic use of Mongoose Coil
Con di tion er (part # 8.914-296.0) will re move lime and
other de pos its be fore coil be comes plugged. (See the
fol low ing in struc tions for use of Coil Con di tion er.)
Periodic fl ushing of coils is recommended.
1. Fill a container with 2 gallons of water, then add
1 lb. of deliming powder. Mix thoroughly.
2. Remove nozzle from spray gun assembly and put
spray gun into con tain er. Secure the trigger on the
spray gun into the open po si tion.
3. Attach a short section (3-5 ft.) of garden hose to
ma chine to siphon solution from an elevated con-
tain er, or add mixture to the fl oat tank. Turn pump
switch on al low ing so lu tion to be pumped through
coils and back into the con tain er. So lu tion should
be allowed to cir cu late 2-4 hours.
4. After circulating solution, fl ush entire system with
fresh water. Reinstall wand assembly to spray gun.
Summary of Contents for HDS3.5/20
Page 31: ......