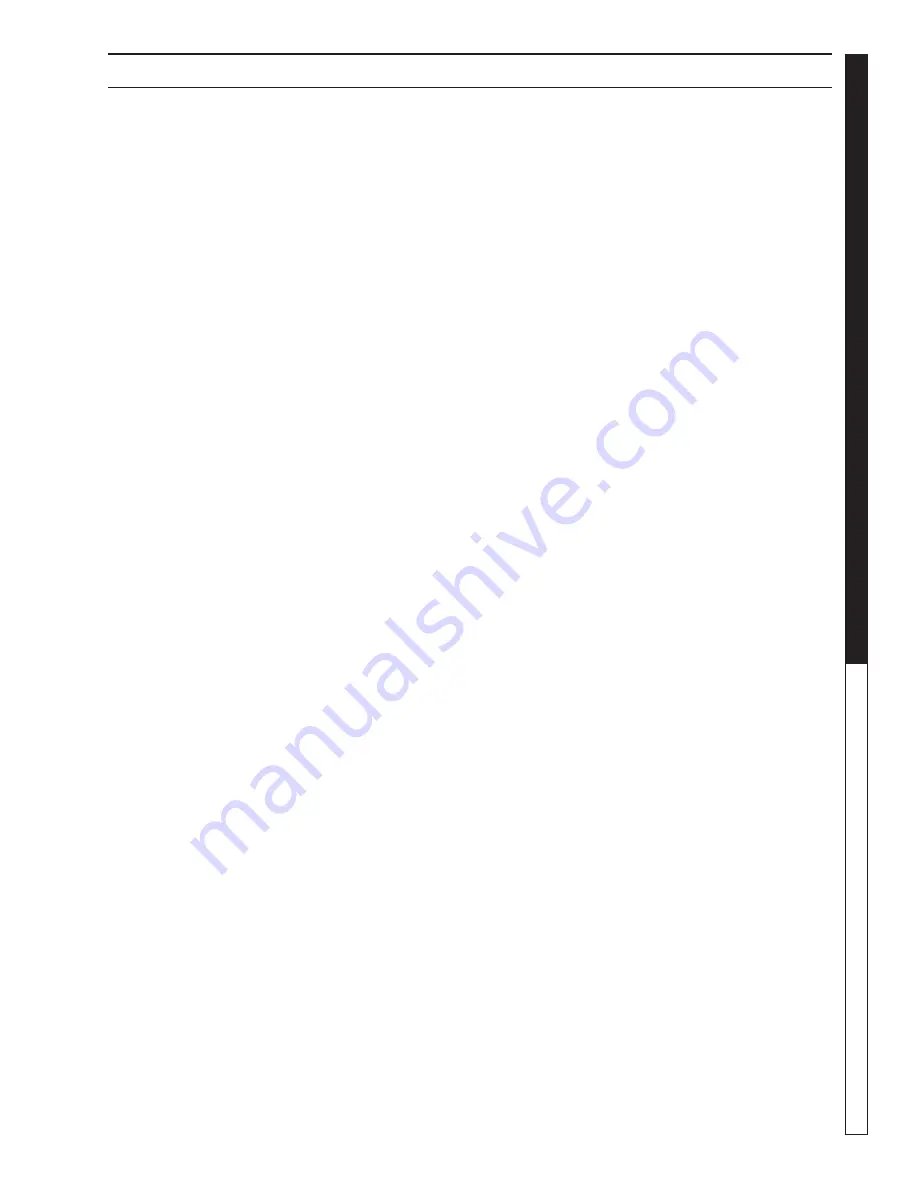
9.801-509.0 - C • Karcher Operator's Manual
11
PRESSURE W
ASHER
MAN
U
AL
containers are equipped with a fi xed liquid level gauge
which contacts the liquid level at 80% of container ca-
pacity, allowing 20% for expansion. LP-gas containers
not equipped with a fi xed liquid level gauge can only
be fi lled by weight.
In cold climates, in order to keep vaporization of LP-
gas at the highest level, keep the fuel levels above
50%.
Room Vents for Combustion and
Ventilation Air
Properly sized vents are vital for the safe and effi cient
operation of a pressure washer installed in a confi ned
space. When combustion and ventilation air are sup-
plied from inside the building, each opening must have
an area of one square inch for every 1,000 BTUH input.
When combustion air is supplied from the outside,
each opening must have an area of one square inch
for every 2,000 BTUH for horizontal ducts and one
square inch for every 4,000 BTUH for vertical ducts
(refer to NFPA 54). See Figure 3.
NOTE:
Air vents for combustion and ventilation
and exhaust fl ue sizing must conform to methods
outlined in current American Standard (ANSI-
Z223.1), National Fuel Gas Code of National
Standard of Canada CSA-149.1 and CSA-149.2
“Installation Code for Gas Burner Appliances”.
Exhaust Stack
The purpose of venting a gas-fi red pressure washer is
to completely remove all products of combustion and
to vent gasses to the outside air without condensa-
tion in the vent or spillage at the draft hood (except in
cases of downdraft or poor stack conditions). Always
use strong, gas-tight, insulated pipe.
The design of this pressure washer depends on natural
draft (heat induced) to pull combustion gasses out of
the combustion chamber. The design of the exhaust
stack can have a signifi cant impact on the proper
operation of the burner and coil.
During vent installation, avoid sharp turns, long hori-
zontal runs and improper pitches. Maintain proper sup-
port of vent connectors and joints, observe clearances
from all combustibles and top the vent outlet with an
approved cap.
Type "B", due to its temperature rating, can only be
used with natural draft pressure washers. A "B" vent
is designed for exhaust temperatures not to exceed
470°F (245°C).
All venting installations must conform to local codes.
In the absence of local codes, refer to "National Fuel
Gas Code" NFPA 54 and be constructed of materials
approved by the Uniform Building Code.
Vents penetrating ceilings or walls should be double-
wall approved appliance vents and should be one to
INSTALLATION
LP-Gas (Liquid petroleum gas or
propane)
LP-gas is gas compressed into liquid form for easy
transportation and storage. It is also known as propane
or bottle gas. (Propane tanks are not supplied with
this equipment.)
LP-gas is fl ammable, is always contained under pres-
sure and the liquid can freeze skin. Therefore, in the
interest of safety, it is important to understand the basic
facts about LP-gas and LP-gas containers.
Federal DOT (Department of Transportation) regulations
require periodic inspections and re-qualifi cations of
cylinders. DO NOT USE damaged or rusted containers.
DO NOT store LP-gas containers indoors or in en-
closed areas. Do not expose LP-gas container to heat.
Always store with service valve closed and plugged
as required.
CAUTION: Use LP-gas containers in proper position.
Most LP-gas pressure washer heaters are designed
to operate on LP-gas vapor only. Therefore, all LP-
gas containers designed for vapor service must be
transported, installed and used in the proper position.
Do not transport, install or use a vertical cylinder in a
horizontal or upside down position. Proper care must
be taken to position a horizontal container in the cor-
rect position for vapor withdrawal. Liquid LP-gas could
enter the system designed for vapor only, possibly
creating a hazardous condition.
Always use a POL plug installed on a POL valve or a
dust cap on an ACME/Type 1 valve when transport-
ing or storing disconnected containers (full or empty).
Check for leaks after connecting. Apply approved leak
detector solution to connection, turn off all burners and
pilots and open service valve. Leaks will be detected
by the growth of bubbles. If bubbles grow, tighten or
repair the connection as needed. Repeat leak test until
problem is corrected.
Check all tank and the line connections periodically
to be sure they are tight. When testing for leaks, use
approved leak detector solution — not matches.
Improved Regulation:
The second stage regulator
receives a relatively uniform pressure from the fi rst
stage regulator. This helps the second stage regulator
to maintain appliance pressure at a nearly constant
11" W.C.
Filling the LP-Gas Container
Only qualifi ed persons should fi ll your LP-gas
containers.
CAUTION: Overfi lling is hazardous!
DO NOT allow your LP-gas container to be overfi lled.
Stop fi lling when liquid appears at the fi xed level gauge.
Bleed off excess propane in a safe area. Most LP-gas
Summary of Contents for HDS3.5/20
Page 31: ......