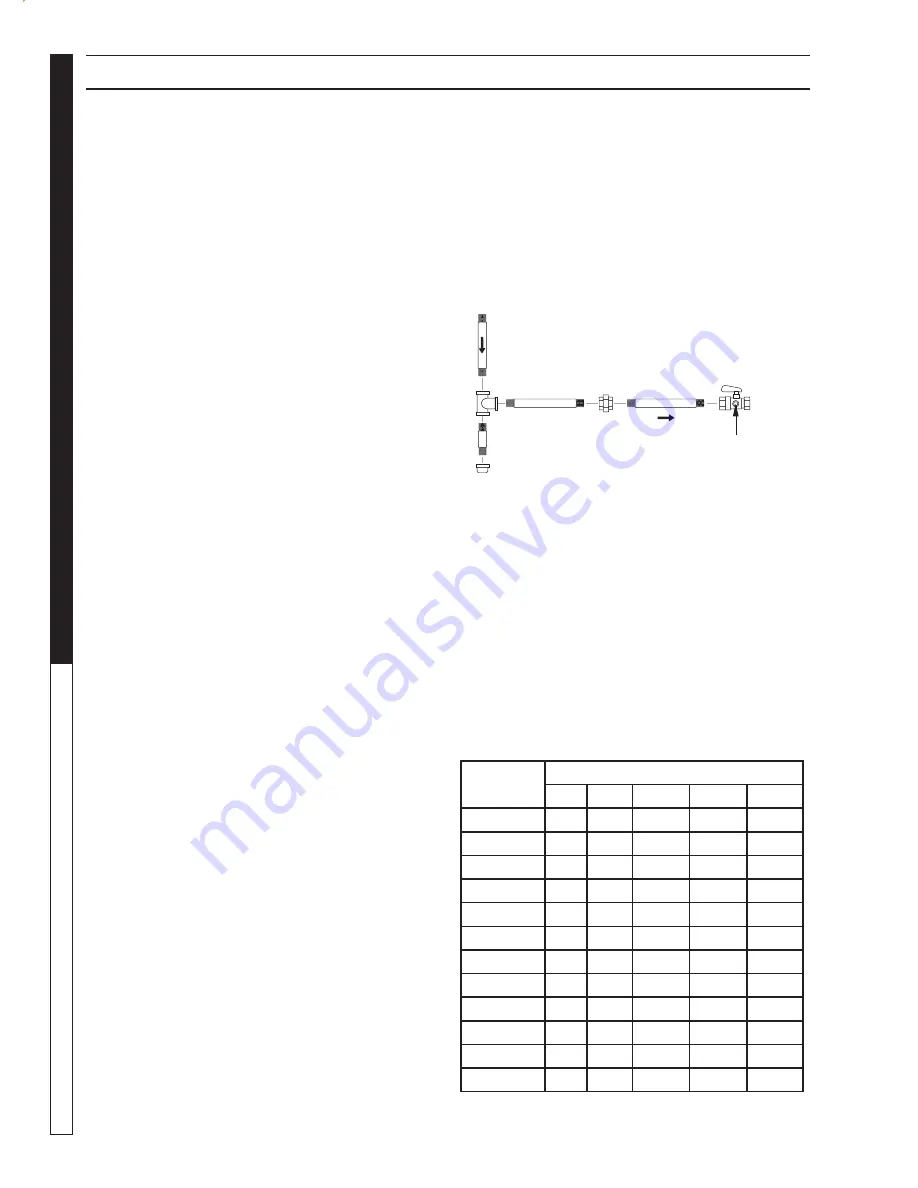
9.801-509.0 - C • Karcher Operator's Manual
MANU
AL
PRESSURE W
ASHER
10
INSTALLATION
Install a gas union in the gas line adjacent to and up-
stream from the con trol manifold and downstream from
the man u al main shut-off valve. A 1/8" NPT plugged
tap ping ac ces si ble for test gauge connection shall
be in stalled im me di ate ly up stream of the gas supply
con nec tion for the pur pose of de ter min ing the gas
supply pres sure to the burn er, and to pre vent damage
to gas valve.
If a manual gas shut off valve is not in the gas supply
line within six feet of the machine and in an ac ces si ble
lo ca tion, one shall be installed.
Figure 1: Union Location
Union Connection
The following pipe sizes are just rec om men da tions.
Always consult a local plumber and vent ing con trac-
tor for local codes and regulations during in stal la tion.
Pipe Sizing Chart for Natural Gas
The following chart is based on gas pressure in the
range 0-0.5 psi, specifi c gravity of 0.6 and pressure
loss of 0.5" W.C. Numbers are for straight schedule
40 pipe; fi ttings further reduce capacity. For example,
in 1" size, an elbow is equivalent to about 2.6 feet of
pipe and a tee is equivalent to about 5.2 feet of pipe.
Maximum capacity of pipe in cubic feet/hr of natural gas
(Multiply values by 1000 to get nominal BTU/hr capacity.
Place machine in a convenient location providing am ple
support, drainage and room for maintenance (pgs 8-9).
Location:
The location should protect machine from damaging en-
vi ron men tal con di tions, such as wind, rain and freez ing.
1. The machine should be run on a level surface
where it is not readily infl uenced by outside sourc-
es such as strong winds, freezing tem per a tures,
rain, etc. The machine should be located consider-
ing ac ces si bil i ty for the re plac ing of com po nents
and the re fi ll ing of detergents, ad just ments and
main te nance. Nor mal precautions should be tak en
by the op er a tor of the machine to prevent excess
moisture from reach ing the machine.
2. It is recommended that a partition be made be-
tween the wash area and machine to prevent direct
spray from the spray gun from coming in contact
with the ma chine. Ex cess moisture reach ing the
power unit or electrical con trols will re duce the
machine’s life and may cause elec tri cal shorts.
3. During installation of the machine, be ware of
poor ly ven ti lat ed lo ca tions or areas where ex haust
fans may cause an insuffi cient supply of ox y gen.
Suf fi
cient com bus tion can only be ob tained when
there is a suf fi
cient sup ply of oxygen available for
the amount of fuel be ing burned. If it is necessary
to install a machine in a poor ly ven ti lat ed area, out-
side fresh air may have to be piped to the burn er
and a fan in stalled to bring the air into the area.
4. Do not locate near any combustible material. Keep
all fl ammable material at least 20 feet away.
Allow enough space for servicing the machine.
Local code will require certain distances from fl oor
and walls. (Two feet away should be adequate).
WARNING: Avoid small areas or near exhaust fans.
Gas Codes:
Confer with local gas company and with proper mu-
nic i pal offi cials regarding any specifi c code or reg u la-
tions gov ern ing the installation. The in stal la tion must
con form to lo cal codes (NFPA 54).
Electrical:
The machine, when installed, must be elec tri cal ly
ground ed in accordance to local codes. Check for
prop er power sup ply using a volt meter; check the
se ri al plate for the cor rect requirements.
Gas Piping:
This machine shall be rigidly connected to the gas pip-
ing outlet and equipped with external manual shut-off
valves adjacent to such machine. All gas piping shall
be approved and installed in accordance with the
Uniform Mechanical Code.
98015100-25
Manual
Shut-Off
Valve
1/8" NPT Plugged Pressure Gauge
Port Location
Union
Drop
Floor Level
Length of
Pipe (ft.)
Iron Pipe Size
3/4"
1"
1 -1/4" 1- 1/2"
2"
10
360
680
1400
2100
3950
20
250
465
950
1460
2750
30
200
375
770
1180
2200
40
170
320
660
990
1900
50
151
285
580
900
1680
60
138
260
530
810
1520
70
125
240
490
750
1400
80
118
220
460
690
1300
90
110
205
430
650
1220
100
103
195
400
620
1150
150
84
160
325
500
950
200
72
135
280
430
800
Summary of Contents for HDS3.5/20
Page 31: ......